PRODUCT IMPROVEMENT –
LSR+ Unicables with SmoothTurn™ Technology
October 11, 2022
For use with TOUGH GUN® TA3 ThruArm® series robotic MIG guns, LSR+ (Low-Stress Robotic) unicables incorporate new SmoothTurn™ technology to maximize production uptime.
Conventional style unicables typically come with a connection that limits rotational capabilities and produces torsional stress in the cable. Unlike conventional unicables, the LSR+ incorporates a rotating power connection that reduces this stress during rotation. Additionally, a protective external conduit contributes to cable longevity by shielding components from harsh welding environments.
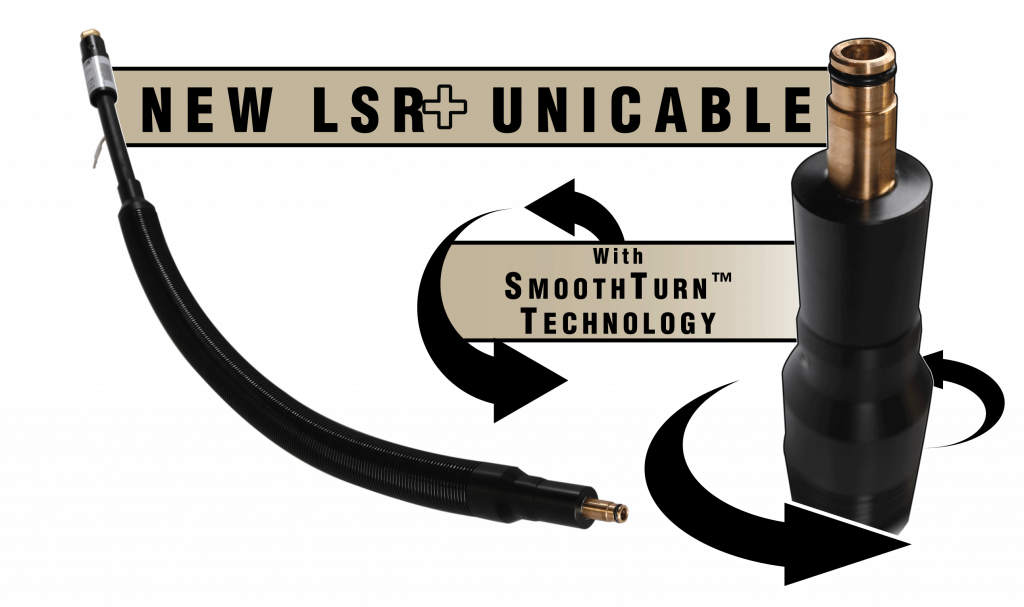
Stress Relieving Features
- SmoothTurn Technology reduces frictional forces on internal components increasing overall cable life up to 300%
- Enhanced electrical connections provide a more stable arc, resulting in less spatter and longer cable life
- Unique internal components improve support and bend radius of the cable during heavy robot articulation
The Importance of Cutting a Welding Liner Properly
Installing a welding liner correctly is, first and foremost, a matter of proper training. For traditional systems, it’s critical that welding operators understand how to measure and cut the liner to the required length for the gun.
A welding liner that has been cut either too short or too long can lead to a host of issues, most often poor wire feeding. That, in turn, can lead to weld quality issues and rework — both factors that contribute to unnecessary and costly downtime.
The Bernard® AccuLock™ S Consumable System can help eliminate installation issues. First, however, it’s important to understand the pitfalls of standard liner installation to understand the value of this solution.
The problem
The position of the gun and power cable factors significantly into whether liner installation is successful. If the gun and power cable are twisted or coiled before the welding operator trims the liner, the liner can end up either too long or too short, due to how the cable is constructed.
Inside the power cable is copper that is wound around a central conduit in a helix or spiral. If the cable is twisted or coiled, it will grow or shrink based on how the copper helix is also twisted. Think of a spring — if it is twisted one way, it grows; if twisted the other way, it shrinks.
For this reason, it’s important to lay the gun and cable straight to avoid any kinks that would lead to an incorrect reading when trimming the liner. Generally, longer power cables are more prone to twisting, so welding operators must take even more care when installing liners in them.
Welding operators may experience the following due to an improperly trimmed liner:
• Poor wire feeding
• Erratic arc
• Birdnesting
• Burnbacks
• Wire chatter
A new solution
The Bernard® AccuLock™ System eliminates the need to measure the liner for replacement. The liner locks into place so it can then be trimmed flush with the power pin cap at the back of the gun and power cable. It is still important to lay the gun and cable flat, avoiding twists.


The welding operator can conduct a visual check to determine the liner is in the proper place. This check isn’t possible with a traditional liner if it has been cut too short; the liner will be hidden under the nozzle and gas diffuser, and not visible to the welding operator.
The AccuLock System reduces wire feeding issues through the gun, as well, since the liner is locked and concentrically aligned at both the power pin cap and contact tip. This dual lock helps ensure the liner won’t extend or contract as the welding operator changes positions and the power cable naturally bends. The result is the elimination of gaps or misalignments at the front and back of the gun for a flawless wire-feeding path.
As an added benefit the concentric alignment of the liner reduces mechanical wear on the contact tip that could lead to burnbacks or keyholing, both of which shorten the contact tip life.
For more information please visit the AccuLock S consumables product page.
AccuLock™ R Consumables Now Available on Fixed Automatic and Robotic Water-Cooled MIG Guns
AccuLock™ R Consumables Now Available on Fixed Automatic and Robotic Water-Cooled MIG Guns
WINDSOR, Ontario (October 27, 2020) – Tregaskiss announced its fixed automatic MIG guns and robotic water-cooled MIG guns are now available with AccuLock™ R consumables. This consumable system has been designed to increase contact tip life and virtually eliminate cross-threading issues, leading to a reduction in both planned and unplanned downtime for changeover.
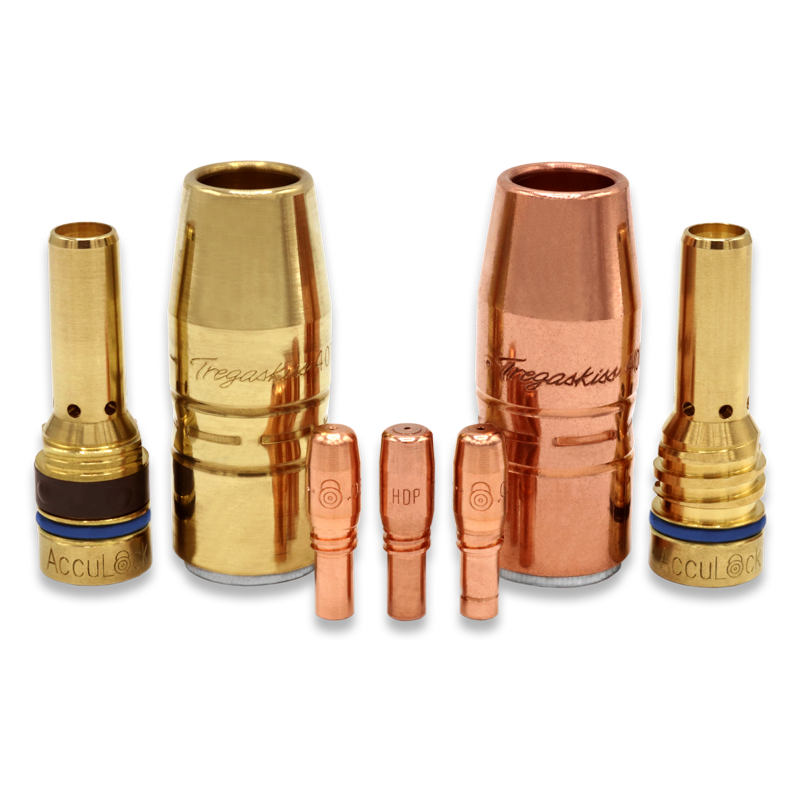
AccuLock R consumables are compatible with the Tregaskiss MA1 fixed automatic air-cooled MIG gun, as well as the Tregaskiss MW1 and AW2 fixed automatic water-cooled guns for hard tooling automation applications. They are also available on the Tregaskiss 600-amp robotic water-cooled MIG gun, which is designed to improve productivity on demanding applications, such as welding thick plate or running prolonged duty cycles. Customers currently using TOUGH LOCK® consumables on their 600-amp robotic water-cooled gun can convert to AccuLock R consumables with no impact on Tool Center Point (TCP).
The consumables, including contact tips, gas diffusers and nozzles, are an option to select when customizing any of the guns using the Tregaskiss online configurators.
AccuLock R contact tips feature coarse threads that are responsible for virtually eliminating cross-threading, along with a long contact tip tail. The tail concentrically aligns inside the diffuser before engaging to ensure quick and accurate contact tip replacement, reducing time spent troubleshooting.
The AccuLock R contact tip has an increased mass at the front of the tip; plus, 60% of the tip is buried in the diffuser so it is protected from the arc’s heat. Tapered mating surfaces provide excellent electrical conductivity and also keep the consumables locked in place.
DISCONTINUED PRODUCTS — Various Part Numbers
DISCONTINUED PRODUCTS —
Various Part Numbers
October 23, 2020
Effective December 31, 2020, we will be discontinuing a variety of part numbers due to low demand and sales volume. A majority of these items are configured MIG gun part numbers and special products.
Please refer to the appendix for the list of affected part numbers.
Customer Testimony | Tico Adopts Bernard MIG Welding Guns & Consumables
Tico Adopts Bernard MIG Welding Guns & Consumables
Using Bernard® Q-Gun™ semi-automatic air-cooled MIG guns and Centerfire™ consumables, Tico Terminal Trucks and Trailers improved productivity and reduced welding costs.
Bob Jolson, owner of Jolson Welding, discusses the benefits of Bernard’s Q-Gun™ semi-automatic air-cooled MIG gun, Dura-Flux™ self-shielded flux-cored gun and Centerfire™ consumables in his welding operation.
Bob Jolson, owner of Jolson Welding, talks about the benefits of Bernard’s Centerfire™ consumables.
Bob Jolson, owner of Jolson Welding, talks about why he swears by the Bernard® Dura-Flux™ self-shielded flux-cored gun.
Contractor Bob Jolson talks about how Bernard’s Q-Gun™ semi-automatic air-cooled MIG gun has increased his productivity and reduced his back pain while welding large diameter pipe.
Jolson Welding (Wheatland, Calif.) relies on the durability and comfort of the Bernard® Dura-Flux™ self-shielded flux-cored gun for its tough structural, pile and pipe welding projects. Learn how the features of this gun help them get the job done.
Learn what Graham Corporation has to say about Bernard® MIG guns and consumables.
Bernard® MIG welding consumables help Taylor Machine Works save time by reducing contact tip changeover in its forklift welding operations. Since converting to Centerfire™ consumables, the company has gone from requiring multiple contact tip changes per day to only one on average per welder. The contact tips can be changed without tools, which saves time, plus they are heavier duty than Taylor’s previous brand, so they last longer. During the original trial of the consumables, Taylor even had one welder go 27 days without changing a contact tip! The gas diffusers and nozzles are also long lasting, so Taylor’s welders can spend more time welding and have less downtime for changeover.
Taylor Machine Works saves money by welding its forklifts with Bernard® MIG guns — all parts are replaceable, and the necks adjust to fit tight joints. The company’s previous MIG welding guns required downtime to take apart for maintenance and repair and were typically disposed of instead. The Bernard MIG guns make it quick to connect new parts, including swapping out necks. The necks are also rotatable so welders can adjust them to new angles to make it more comfortable to weld in hard-to-reach areas.
Tulsa Welding School’s Houston campus needs reliable equipment that can handle any process. Bernard® MIG guns and consumables are the answer. You can count on Bernard BTB semi-automatic air-cooled MIG guns to deliver industrial-grade performance and reliability in the most demanding environments as well as optimize welder ergonomics and weld access. Bernard contact tips, nozzles and diffusers are easy to use and high performing – they provide better arc starts, less spatter and more consistent welds – and also last up to three times longer than competitive brands.
Blinn College welding school instructors and students agree – Bernard® MIG guns and consumables are the welder’s best choice in dependability and easy to use. You can count on Bernard BTB semi-automatic air-cooled MIG guns to deliver industrial-grade performance and reliability in the most demanding environments as well as optimize welder ergonomics and weld access. Bernard contact tips, nozzles and diffusers are easy to use and high performing – they provide better arc starts, less spatter and more consistent welds – and also last up to three times longer than competitive brands.
Watch as we compare the time it take to change Bernard® Centerfire™ consumables on our BTB MIG Gun compared to our competitor.
Watch as we compare the strength of our Bernard® BTB semi-automatic air-cooled MIG gun handle to those of our competitors.
For a cleaner, more compliant work environment, get right to the source and extract fumes at the weld with the Bernard® Clean Air™ fume extraction gun. Closely matching the weight, handle size, durability and industrial grade performance of Bernard BTB semi-automatic air-cooled MIG guns, Clean Air fume extraction guns are fully configurable with your choice of curved or straight handles.
Build your ultimate MIG gun. Choose from a variety of necks, handles and trigger styles to optimize welder ergonomics and weld access. Then standardize with a single line of consumables to simplify maintenance and contain costs. You can count on Bernard® BTB semi-automatic air-cooled MIG guns to deliver industrial-grade performance and reliability in the most demanding and abusive environments.
Now mobile friendly! Configure your Bernard® semi-automatic MIG gun – anytime, anywhere! We recognize that welding applications differ for every welder and that sometimes only a customizable, industrial-duty MIG gun will get the job done. That’s why we allow you to configure a custom MIG gun for your specific application.
As you support more inexperienced welders, choosing equipment with fewer points of failure and simplified maintenance can reduce training and shorten your troubleshooting list. Learn more about Bernard® AccuLock™ S consumables.
Meet Sam, a semi-automatic MIG Welding Supervisor at an Industrial Company. Sam’s faced with increasing manufacturing growth putting production throughput and quality targets at an all time high. Everyday Sam wastes valuable time troubleshooting welding issues related to poor wire-feeding such as birdnesting, burnbacks and erratic arc, which all leads to poor weld quality. What if there was a solution for Sam? Introducing AccuLock (Semi-Auto) Consumables: Shorten Your Troubleshooting List: With AccuLock Consumables, SAM (and you) can… Load and Lock for Better Productivity, reduced troubleshooting, downtime and rework. Load and Lock with Bernard® AccuLock™ S consumables.
Maintaining quality, productivity and cost savings is important in any semi-automatic MIG welding operation, but the steps companies take to achieve those goals vary. Still, there is one constant: the value of skilled welders. They are at the heart of the operation and help ensure its success. Having the right equipment and understanding how to care for it are also important, as is Consider these tips to help along the way: Welder training Gaining good weld quality depends on welders knowing proper techniques like gun angle and gun travel speeds and the impact of welding parameters on the process. Even if a company sets lockouts that keep welding parameters within a specific range, it’s valuable for welders to understand the impact voltage, amperage, wire feed speed and shielding gas have on the application. It’s also important to provide training on other best practices in the MIG welding operation, such as: Assessing the process Time studies, for example, offer excellent insight into the entire workflow and allow companies to record the amount of time each task takes to complete. These studies include a breakdown and analysis of parts handling, welding and more. By recording every activity in the operation, it is possible to see whether each one is adding value. If not, adjustments and re-sequencing can be made. Analyzing the operation can also help identify the need for more welder training. For instance, if a significant amount of time is spent grinding after welding, it can indicate that there are issues contributing to overwelding or poor weld quality. The company can then take proactive steps for additional welder training to improve quality and reduce or eliminate the need for grinding and rework. Similarly, if welders are spending more time transferring parts than they are welding or there are bottlenecks of parts entering the welding cell, that indicates the workflow needs to be adjusted. The goal is to minimize the amount of time welders spend handling or double handling parts and helps avoid parts from backing up or having welders sit idle waiting for them. Improving the organization of the workstation as part of a general assessment can also help improve welding productivity. This could include adjusting welding tables and part racks to be more ergonomic so welders are more comfortable and can weld longer. Welding gun selection and use One of the first things to consider is cost. Quality MIG welding guns carry a higher price, but they are worth it in the long term. A better gun (when used properly) lasts longer and can help improve weld quality and efficiency over time. Guns that feature mechanical compression fittings, as opposed to crimped fittings, are a good choice. They typically last longer from wear and tear and can also be repaired if damaged, which saves money on replacement guns. Be certain to choose a gun with the appropriate amperage rating and duty cycle for the application to prevent overheating. A lower amperage MIG welding gun may be appealing to a welder due to its lighter weight and flexibility; however, it will not be able to withstand an application requiring higher amperages and long arc-on times. Effectively grounding the weld circuit is another way to gain weld quality and productivity in a semi-automatic welding operation. It can also protect the welding gun from overheating and from wearing out consumables too quickly. Installing the ground clamp as close to the weld as possible and limiting the amount of connections can help to prevent one or more from coming loose over time or creating electrical resistance. Always choose correctly sized ground cables for the weld circuit and the right type of ground clamp. A C-clamp is a good option as it is a tighter connection versus a spring clamp, which helps prevent arcing at the ground that could lead to an erratic arc. As with other quality components in a MIG welding operation, C-clamps can be more expensive, but they offer a connection that can better protect the gun and save on replacement or repair costs. Lastly, take care to inspect the welding gun cable regularly for damage and replace as necessary. Nicks or cuts in the cable can expose bare copper, causing a safety hazard of electrical shock, as well as erratic welding issues. Adding a cable jacket cover is a proactive step in avoiding these problems. The role of consumables and wire Always trim the liner properly — per the guns owner’s manual — to avoid erratic arcs and burn backs or look for liners that lock into place and require no measurement to avoid trimming them too long or too short. For semi-automatic MIG welding, copper contact tips work well; however, if more tip life is desired or needed, chrome zirconium tips are an alternative to better resist physical tip wear (also known as keyholing). It helps to monitor how often contact tips are being changed to avoid straying too far from the originally planned frequency of tip changeover. If tip changes begin to increase drastically, then this points to incorrect installation of consumables, a liner being cut too short or other damage in the system. Monitoring consumables usage can also help identify when contact tips could still have life left in them. If contact tips are changed too early, this results in unnecessary downtime. Also consider the wire being used. Quality is key here, too. Less expensive wires often have an irregular cast or helix or an inconsistent layer of lubricant. All of these factors can lead to weld quality issues and additional wear on the contact tips. Keeping on track Challenged by increasing welder retirements and turnover while orders keep growing year over year? As you support more inexperienced welders, choosing equipment with fewer points of failure and simplified maintenance can reduce training and shorten your troubleshooting list. Bernard® AccuLock™ S consumables provide error-proof liner replacement every time — no measuring required!
Customer Testimony | Jolson Welding Discusses Bernard MIG Guns, Flux-Cored Guns and Welding Consumables
Jolson Welding Discusses Bernard MIG Guns, Flux-Cored Guns and Welding Consumables
Customer Testimony | MIG Welding with Bernard Centerfire Consumables
MIG Welding with Bernard Centerfire Consumables
Customer Testimony | Flux-Cored Welding with a Bernard Dura-Flux Gun
Flux-Cored Welding with a Bernard Dura-Flux Gun
Customer Testimony | MIG Welding with a Bernard Q-Gun MIG Gun
MIG Welding with a Bernard Q-Gun MIG Gun
Customer Testimony | Contractor Shares Benefits of Bernard Dura-Flux Self-Shielded Flux-Cored Gun
Contractor Shares Benefits of Bernard Dura-Flux Self-Shielded Flux-Cored Gun
Customer Testimony | Graham Corporation Adopts Bernard MIG Guns and Consumables
Graham Corporation Adopts Bernard MIG Guns and Consumables
Customer Testimony | Bernard MIG Welding Consumables Save Time and Last Longer
Bernard MIG Welding Consumables Save Time and Last Longer
Customer Testimony | Bernard Replaceable MIG Gun Parts Save Money, Improve Performance
Bernard Replaceable MIG Gun Parts Save Money, Improve Performance
Customer Testimony | Welding students in Tulsa benefit from Bernard MIG guns and consumables
Welding Students in Tulsa Benefit from Bernard MIG Guns and Consumables
Customer Testimony | Blinn Instructors Choose Bernard MIG Guns and Consumables for Dependable Welding Equipment
Blinn Instructors Choose Bernard MIG Guns and Consumables for Dependable Welding Equipment
Video | Bernard Centerfire Changing Consumables Challenge
Bernard Centerfire Changing Consumables Challenge
Video | Bernard BTB MIG Gun Handle Impact Test
Bernard BTB MIG Gun Handle Impact Test
Animation | Bernard Clean Air Fume Extraction MIG Welding Guns
Bernard Clean Air Fume Extraction MIG Welding Guns Animation
Animation | Bernard BTB Semi-Automatic Air-Cooled MIG Welding Guns
Bernard BTB Semi-Automatic Air-Cooled MIG Welding Guns Animation
Video | Configure your Bernard Semi-Automatic MIG Gun Online
Configure your Bernard Semi-Automatic MIG Gun Online
Video | Bernard AccuLock S Consumables for the Inexperienced Welders
Bernard AccuLock S Consumables for the Inexperienced Welders
Video | Bernard AccuLock S Consumables for Better Productivity
Bernard AccuLock S Consumables for Better Productivity
Tips for Improving MIG Welding
revisiting the welding process regularly to ensure its efficiency. Companies should take care to watch for common pitfalls that could negatively affect their progress toward streamlining and improving their operation.
With the industry facing an anticipated welder shortage of 400,000 by 2024, providing training to new welders is critical to supporting a productive and profitable MIG welding operation. In many cases, employees being hired are entirely new to welding or only have limited experience. Learning best practices early on is necessary to achieve the best performance and avoid excessive downtime for troubleshooting.
MIG welding operation, it’s a good
idea to regularly assess each aspect of it.
To support the long-term efficiency of a MIG welding operation, it’s a good idea to regularly assess each aspect of it.
Having the correct MIG welding gun for the application can help enhance performance in a MIG welding operation.
Contact tips, nozzles, gas diffusers and liners all affect MIG welding performance. Ideally, select consumables and wire designed to complement one another as a system. These can help maintain solid connections that provide the best electrical conductivity and arc stability.
Maintaining an efficient MIG welding operation takes time and resources, but it’s worthwhile to make an investment in welders and equipment to achieve the best results. Continue to monitor the process for improvement opportunities and engage welders whenever possible. Since welders are responsible for moving quality and productivity forward, their ideas can be a valuable asset.Animation | Bernard AccuLock S Consumables No Measuring Required
Bernard AccuLock S Consumables | No Measuring Required