Avoid These 5 MIG Gun Myths to Optimize Performance
MIG guns and consumables are sometimes an afterthought when purchasing a welding system, but considering that they are the most handled piece of welding equipment and are exposed to the most environmental and operator abuse, they can have a significant impact on weld quality, productivity and operator downtime.
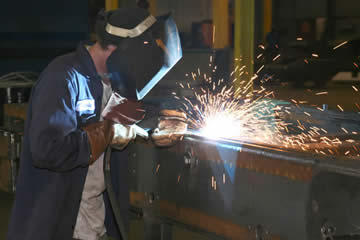
Much of the reason MIG guns and consumables do not receive their fair share of attention within the equipment selection process arises from common misconceptions about their importance in the welding operation.
The following are five of the most common myths surrounding MIG guns and consumables and the corresponding truths that can help you improve productivity, reduce costs and increase operator efficiency.
Myth #1 — MIG guns are all the same, so price should be the deciding factor when purchasing a new gun.
Truth — MIG guns vary substantially in quality, performance and value. Purchasing a quality gun designed with features that minimize downtime, weld quality problems and premature equipment failures can result in significant long-term savings. These efficiencies can save you far more than the price difference between a high performance and inferior quality gun.
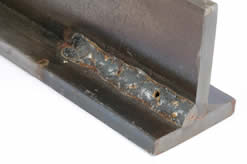
Conversely, a high quality MIG gun will offer features, design elements and construction that allow them to provide reduced operator fatigue and fewer burnbacks, birdnests and other problems.
When evaluating the long term value of a MIG gun and consumables system, you need to consider the service life of the gun, replacement parts costs, the cost of downtime when the gun needs servicing, and the ease with which components can be changed.
First, consider the downtime that can result from choosing MIG guns and consumables without looking into their full long-term cost. If a gun’s only selling point is its price, it could be manufactured with inferior components that don’t last as long as high quality components, are more difficult to replace when they do need replacing and cause the premature failure of other components.
An example of the difference between high and low-quality components can be found in the power cable fittings. Set-screw fittings can loosen over time and result in poor electrical conductivity and increased resistance. On their own, these problems can reduce weld quality and require reworking or scraping parts. Uncorrected, these problems can also lead to increased resistive heat at the point of the fitting. This heat causes additional stress and shortens the service life of the gun and cable. By contrast, a high performance gun often uses compression fittings, which produce a more secure connection between the cable and gun and will be less likely to result in weld defects or cause the deterioration of other components.
Consumables are another component in which trying to save a couple bucks on the purchase price could become very costly in the long run. A high quality consumables system requires fewer tip changeovers and those changeovers are often faster, reducing both equipment costs and operator downtime.
Overall, the cost of operator downtime should be your company’s primary reason to avoid choosing guns and consumables based solely on price. If each of your welders averages three hours a week adjusting and replacing MIG gun components, at an average employee cost of $30/hour, that downtime adds up to $4,680 per year in unnecessary costs (and that’s not even counting the material cost resulting from scrapped work).
Myth #2 — Consumables aren’t very important to weld quality and performance.
Truth — The MIG gun’s consumables — the nozzle, diffuser and contact tip — provide shielding gas and are the last component of the welding system to come into contact with the welding wire before it enters the weld pool. As such, consumables can have a big impact on weld quality and productivity, and selecting high quality ones and properly maintaining them is essential.
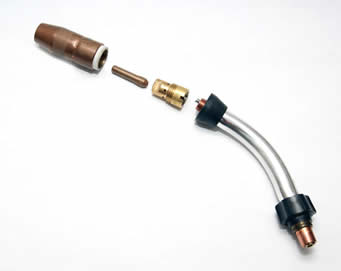
Consumables differ considerably by brand in terms of both design and material quality. Good quality consumables provide a large contact area between the diffuser and the contact tip and feature a secure locking mechanism to keep the contact tip and diffuser fitting tightly together. These features mitigate weld quality problems related to inconsistent electrical transfer, and also the frequency of contact tip burnbacks — a noteworthy source of downtime.
Equally important to selecting the right consumables is maintaining them properly. Good quality consumables resist built-up better than low quality ones, however, no consumables can completely avoid spatter build up. Use a needle nose pliers, nozzle reamer or other device to dislodge built up spatter to prevent interruptions in shielding gas flow and corresponding weld defects. You should inspect the nozzle for spatter build up several times a day and clean it out as needed.
In addition to checking and cleaning out spatter, you should check to ensure the contact tip sits tightly in the diffuser and that the inside bore has not become excessively worn. Non-threaded contact tips can be rotated in place to provide a new contact surface with the welding wire when it becomes worn on one side. Some threaded contact tips allow you to rotate them 180-degrees to also provide extended tip life.
Myth #3 — Preventative gun and consumables maintenance is a waste of valuable time that could be better spent in production.
Truth — Compared to the time spent reworking bad welds and replacing severely damaged components, spending a few minutes each day inspecting and maintaining the MIG gun and consumables is a bargain.
Identifying potential problems early is essential to avoiding the much higher costs that can result from allowing a minor problem to grow into a major headache. For example, a damaged O-ring on the feeder connection is very easy and inexpensive to repair, but left unchecked, it can create very costly weld porosity.
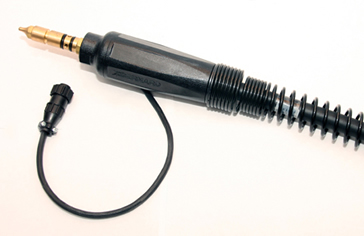
Because MIG guns have few moving parts and are relatively simple to inspect, you should check the connections between the wire feeder, the cable, the gun, the neck and the consumables on a daily basis to ensure they are tight and undamaged. A loose or damaged fitting can create resistive heat build-up, poor weld quality and shortened component life.
Consumables should be checked several times throughout the day to ensure the inside bore of the contact tip is not excessively worn down and that the shielding gas flow is not obstructed by spatter in the nozzle.
The liner is one of the most difficult MIG gun components to inspect, so it’s often best to use compressed air to clean out any metal shavings and debris during each wire changeover.
Routine inspection and maintenance should take up no more than 10 to 15 minutes per day, which averages out to about $1,300 per year in downtime. By contrast, reworking or scrapping bad welds can take up several hours each time it happens. If an operator spends four hours per week fixing weld defects caused by improperly maintained equipment, that non-production time costs his employer roughly $6,240 per year. Even more importantly, it can cause the company to fall behind on product deadlines and threaten their client relationships.
Myth #4 — It’s always better to err on the safe side and overmatch the gun amperage to the application.
Truth — It almost seems contradictory that most companies are making a mistake by purchasing a 400-amp MIG gun when their applications require 375 amps. In truth, the problem with overmatching the gun to the application is that most operators only weld for 30 to 50 percent of the time, which means that they can easily get by with a 300-amp gun and rarely, if ever, exceed its duty cycle in an application requiring 375 amps.
A 400-amp gun could certainly handle the demands of the application, but it is also heavier and bulkier, leading to earlier operator fatigue and reducing productivity.
In order to achieve maximum operator efficiency, companies need to analyze their specific welding demands and purchase a gun that is as small and light as possible while still meeting the amperage requirements of the application.
Another factor you should consider when purchasing a MIG gun is the weight and size differences between brands. In many cases, a gun from one company rated to 400 amps will be considerably heavier and bulkier than a similarly rated gun from another company.
Not all gun manufacturers label and market their guns to a 100 percent duty cycle rating, however, so be sure to verify that you are making an apples-to-apples comparison when evaluating MIG guns from different manufacturers. For example, company A’s 300-amp MIG gun might be able to weld at 300 amps at 100 percent duty cycle, but company B might also make a gun that they call a 300-amp MIG gun that is only rated to 300 amps at 40 percent duty cycle. The amperage to duty-cycle ratings are usually available in the spec sheets from most major MIG gun manufacturers, so check there to make sure the gun is able to handle your applications.
Myth #5 — The MIG gun liner does not have a significant impact on welding performance.
Truth — It’s true, properly functioning MIG gun liners, regardless of brand, do not have a significant impact on welding performance. It’s when the liner is not functioning properly that its importance in the welding operation — and the difference between a high and a low quality liner—becomes clear.
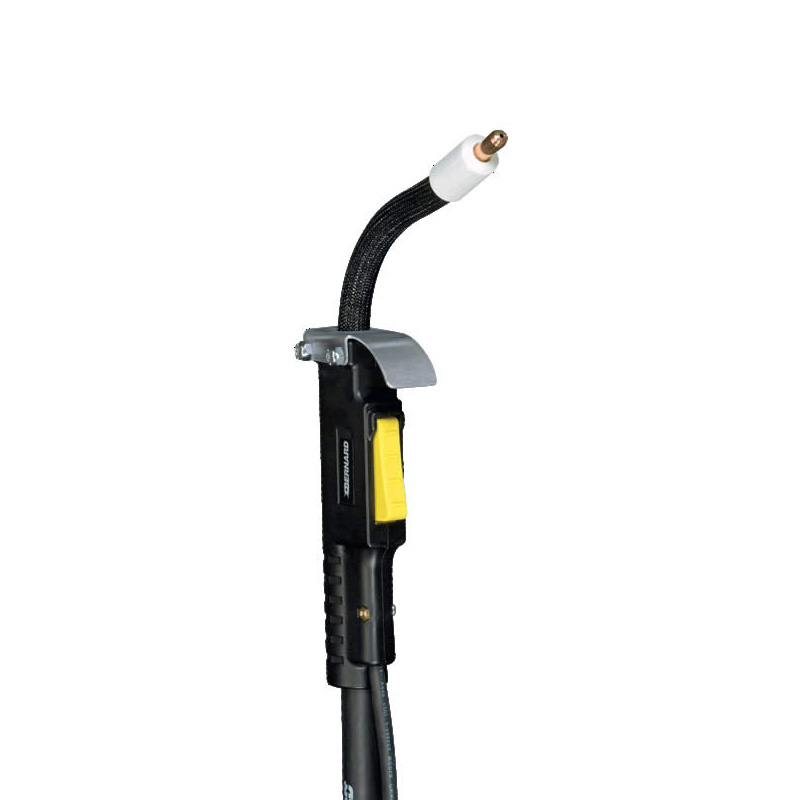
The liner’s main function is to provide unobstructed passage for the welding wire to travel from the feeder, though the cable and gun into the consumables. It’s a very simple role within the welding operation, yet a number of problems can arise in the liner that can lead to weld defects and lost productivity.
A high quality liner can provide a more consistent inside diameter through which the welding wire travels, thereby reducing friction and extending the service life of the liner as well as the time that it takes for wire filings to clog the liner—one of the most frequent sources of liner-related downtime. The liner is most susceptible to this problem when the cable is bent too far and increases the friction between the wire and liner.
Other causes of clogged liners include using an incorrect liner size and trimming it improperly. In both cases, the liner can shave metal filings from the welding wire and become clogged, leading to erratic wire feeding, poor weld quality and birdnests. Because the copper stranding in MIG gun cables is wound in a helix pattern, the cable shrinks when it is twisted. Trimming a new liner to the length of a twisted cable can cause the liner to be too short when the cable is straightened out, leaving an empty space in which the welding wire can become lodged and birdnest.
Additional downtime can be saved by using an easily-replaced partial liner that installs from the front of the gun and only goes through the gun’s neck. The most wire-to-liner friction occurs in the neck, so that part of the liner is usually the first to wear out. Rather than spending 20 minutes replacing the entire liner when only that portion becomes worn, some companies offer partial liners that can be changed in as little as two minutes.
In times of economic uncertainty, it’s understandable that companies would seek to reduce their production costs by purchasing less expensive equipment. However, the true cost of purchasing lower quality equipment — lost productivity, reduced weld quality, increased scrap and excessive downtime — can far outpace the cost of selecting higher quality MIG guns and consumables.
MIG (GMAW) welding with shielding gas and a solid wire electrode produces a clean, slag-free weld without no need stop welding to replace the electrode, as in Stick welding. Increased productivity and reduced clean up are just two of the benefits possible with this process. To achieve these results in your specific application, it helps to understand the role of shielding gas, the different shielding gases available and their unique properties. The primary purpose of shielding gas is to prevent exposure of the molten weld pool to oxygen, nitrogen and hydrogen contained in the air atmosphere. The reaction of these elements with the weld pool can create a variety of problems, including porosity (holes within the weld bead) and excessive spatter. Different shielding gases also play an important role in determining weld penetration profiles, arc stability, mechanical properties of the finished weld, the transfer process you use and more. Choosing MIG gun consumables that provide consistent and smooth shielding gas delivery are also important to making successful MIG welds. Many MIG welding applications lend themselves to a variety of shielding gas choices. You need to evaluate your welding goals and your welding applications in order to choose the correct one for your specific application. Consider the following as you make your selection: The four most common shielding gases used in MIG welding are Argon, Helium, Carbon Dioxide and Oxygen. Each provides unique benefits and drawbacks in any given application. The most common of the reactive gases used in MIG welding is Carbon Dioxide (CO2). It is the only one that can be used in its pure form without the addition of an inert gas. CO2 is also the least expensive of the common shielding gases, making it an attractive choice when material costs are the main priority. Pure CO2 provides very deep weld penetration, which is useful for welding thick material. However, it also produces a less stable arc and more spatter than when it is mixed with other gases. It is also limited to only the short circuit process. For companies that place an emphasis on weld quality, appearance and reducing post-weld clean up, a mixture of between 75 – 95 percent Argon and 5 – 25 percent CO2 may be the best option. It will provide a more desirable combination of arc stability, puddle control and reduced spatter than pure CO2. This mixture also allows the use of a spray transfer process, which can produce higher productivity rates and more visually appealing welds. Argon also produces a narrower penetration profile, which is useful for fillet and butt welds. If you’re welding a non-ferrous metal — aluminum, magnesium or titanium — you’ll need to use 100 percent Argon. Oxygen, also a reactive gas, is typically used in ratios of nine percent or less to improve weld pool fluidity, penetration and arc stability in mild carbon, low alloy and stainless steel. It causes oxidation of the weld metal, however, so it is not recommended for use with aluminum, magnesium, copper or other exotic metals. Helium, like pure Argon, is generally used with non-ferrous metals, but also with stainless steels. Because it produces a wide, deep penetration profile, Helium works well with thick materials, and is usually used in ratios between 25 — 75 percent Helium to 75 — 25 percent Argon. Adjusting these ratios will change the penetration, bead profile and travel speed. Helium creates a ‘hotter’ arc, which allows for faster travel speeds and higher productivity rates. However, it is more expensive and requires a higher flow rate than Argon. You’ll need to calculate the value of the productivity increase against the increased cost of the gas. With stainless steels, Helium is typically used in a tri-mix formula of Argon and CO2. All of your efforts selecting the right shielding gas will be wasted if your equipment isn’t getting the gas to the weld. The MIG gun consumables (diffuser, contact tip and nozzle) play a crucial role in ensuring that the weld pool is properly protected. If you choose a nozzle that is too narrow or if the diffuser becomes clogged with spatter, for example, there might be too little shielding gas getting to the weld pool. Likewise, a poorly designed diffuser might not channel the shielding gas properly, resulting in turbulent, unbalanced gas flow. Both scenarios can allow pockets of air into the shielding gas and lead to excessive spatter, porosity and weld contamination. When selecting MIG gun consumables, choose ones that resist spatter build up and provide a wide enough nozzle bore for adequate shielding gas coverage. Some companies offer nozzles with a built in spatter guard that also adds a second phase of shielding gas diffusion. This results in even smoother, more consistent shielding gas flow. Choosing the right shielding gas for your specific application will require a careful analysis of the type of welding you’re doing as well as your operational priorities. Using the guidelines above should provide a good start to the learning process. Be sure to consult your local welding supply distributor prior to making a final decision.
It doesn’t take much to create a MIG weld. All you really need is a power source, some CO2, a MIG gun, ground cable and a wire electrode. Of course, that doesn’t mean you’ll end up with a mechanically sound or decent looking weld. Achieving those results requires a strong skill set, close attention to detail and the right MIG welding consumables (among other things, of course). Often overlooked during the purchasing process MIG gun consumables — the contact tip, nozzle and diffuser — are the decisive variables in electrical transfer to the wire and shielding gas to the weld pool. No matter how well tuned the rest of your welding equipment is to your application, without the right consumables in properly functioning order, your weld quality will suffer. Obtaining high quality welds and high productivity rates requires attention to the type of consumables you purchase, how they are installed and used by your welding operators and accurately troubleshooting consumables problems when they arise. Selecting high quality consumables is paramount to obtaining high quality welds and avoiding unnecessary downtime. High quality consumables provide better shielding gas coverage of the weld, resulting in less porosity and a more stable arc, as well as longer contact tip and nozzle life, reduced burnbacks and fewer weld defects caused by loose consumables fittings. With labor accounting for roughly 85 percent of a welding operation’s expenses, the slightly higher cost of high quality consumables can quickly be offset by these advantages. Another labor-related factor to consider when selecting consumables is the time it takes to change contact tips. A non-threaded contact tip that can be changed by dropping it into the diffuser, without tools, and locking it in place via the nozzle can often cut changeover time in half. Further, consumables systems that can be mounted to a wide variety of gun brands reduce the time it takes to locate a replacement tip and reduces the inventory footprint and time spent monitoring and ordering new product. Equally important is choosing the right consumables for the application. For example, using heavy-duty nozzles, with thick-walls as well as wide nozzle bores, will only add weight and reduce weld pool visibility in low-amperage, thin-gauge applications. Likewise, using thin-walled brass nozzles with narrow nozzle openings in heavy-duty applications could result in inadequate shielding gas coverage, frequent burnbacks and MIG gun consumables are exposed to more heat and mechanical stress than any other component in your MIG welding system, so even the best consumables you can buy will wear out and need to be replaced on a regular basis. While this can’t be avoided, correctly using the consumables can lengthen their service life and improve weld quality. Maintaining the correct contact tip stick out or recess, as it relates to the end of the nozzle, is crucial to ensuring good weld results. The amount that a contact tip is recessed or extended past the nozzle determines the wire stick-out and how much heat from the arc the contact tip absorbs. High current, high heat applications generally require a contact tip recessed up to 1/4” from the end of the nozzle. Lower amperage applications, or those with narrow joint configuration, might require a flush or extended contact tip. Contact tips are available either as adjustable or with a fixed recess. Adjustable recess contact tips allow you to simply raise or lower the contact tip to your liking, but they also increase the potential for human error, particularly in welding operations where multiple operators use the same gun. Fixed recess contact tips need to be changed when changing to a different application, but they standardize the weld process and eliminate a variable that can affect welding performance. Below is a chart showing the recommended tip recesses for a variety of applications and processes. Regularly inspecting, cleaning and adjusting the consumables is also critical to ensuring weld quality. A nozzle that becomes clogged by spatter can restrict shielding gas flow and lead to porosity. You can use a welder’s pliers or a nozzle reamer to clear out any spatter that builds up. Likewise, the contact tip can develop an oval shaped bore, called keyholing, from the welding wire passing through it, which can cause interruptions in electrical current to the wire, resulting in an unstable arc, porosity and other problems. Some brands of contact tips can be rotated to provide additional contact surface when the wire wears out a portion of the bore. Unfortunately, no amount of deliberation and careful use can completely eliminate problems from occurring. Being able to quickly and accurately troubleshoot problems when they do occur, however, can reduce the impact of the problem and the downtime that you incur. Generally speaking, the best way to troubleshoot a problem is to use the process of elimination to move from the least to the most time consuming equipment to check. Contact tip burnback, where the welding wire fuses to the contact tip, occurs occasionally if the tip gets too close to the weld pool, but it could also indicate an equipment problem if it occurs frequently or happens when the contact tip is not too close to the weld pool. Some common sources of contact tip burnback are: incorrect contact tip recess, a faulty work lead or ground, and erratic wire feeding (discussed below). Erratic wire feeding is usually caused by an obstruction or kink in your liner, incorrect or improperly tensioned drive rolls or a worn out or wrong sized contact tip. If this problem is encountered, inspect the contact tip, then check the drive rolls and finally remove and inspect the liner if the first two items are functioning properly. Replace any of these items that appear worn or damaged. An erratic arc can be caused by erratic wire feed, but is most commonly a result of inconsistent electric current being delivered to the wire. A gun neck that is too straight or a worn out contact tip are common sources of an erratic arc. If the contact tip appears in good working order and the neck is at least a 30 degree bend, check the electrical connections between the components to ensure they are tight and free of debris. Spatter is a common occurrence in MIG welding, but excessive spatter could signal an equipment malfunction. Either too much or too little shielding gas flow as well as an improperly installed contact tip are common causes of excessive spatter. Try adjusting these components first, before moving on to other possible causes. Porosity — small holes in the weld bead — is another common outcome of too much or too little shielding gas. Begin troubleshooting porosity by checking that the nozzle is not clogged by spatter. If the nozzle is clear, move on to check that the gas ports are not blocked by an obstruction, that the solenoid is working properly and that the o-rings at the back end of the MIG gun are not damaged. Also check the electrical connections at the MIG gun, ground clamp and consumables to make sure they are providing good electrical transfer. Although some troubleshooting can’t be avoided, you can greatly reduce your downtime spent changing contact tips and troubleshooting weld defects by carefully choosing your MIG gun consumables and carrying out a regular inspection and maintenance schedule. Laying down a strong, great looking MIG weld is no easy task, but doing so with poor quality or improperly configured equipment is virtually impossible. The little time you spend researching, choosing and maintaining your equipment will save you a considerable amount of time, and headaches, down the road.
Welding contractors seem to do it all. At least at Jolson Welding they do. From welding piles and water lines to beams, heavy wall underground pipe and bridges, owner Bob Jolson and his team of contractors tackle some of the toughest jobs on the West Coast. And they do it quickly, thanks to some recent changes to their welding equipment and consumables. “I always like to try new things with our business. I keep trying them until I find something that I like and that works,” explains Jolson. “It helps keep us a lot more competitive on our bidding.” At Jolson’s company in Wheatland, California, their primary focus is on heavy-duty commercial welding, which includes welding pipe ranging from ½ inch OD to 200-inches in diameter and wall thickness of 1/8 inch to unlimited thickness. Taking on such large projects doesn’t leave much room for downtime if the company is to stay on schedule and remain competitive in their bidding. And while Jolson has always taken care of his customers, since pairing his Bernard’s Q-Guns™ and Dura-Flux™ guns with Hobart Brothers’ Excel Arc™ 71 gas-shielded and Fabshield® XLR-8 self-shielded wires, respectively, he’s been able to do more than just stay on schedule — he’s improved the company’s productivity by 30 percent along the way. Since Jolson founded his company in 1989, he and his business partner and wife, Colleen, have worked diligently to gain welding contracts along the West coast. Supporting the business is welder, Brandon Hobbs. Their efforts haven’t been in vain. Between referrals they receive from other contractors to repeat business and active bidding, they’ve carved a niche for themselves as the ‘go-to’ company for pile driving and pipe welding, especially. Each of the welding contracts Jolson takes on has its own unique requirements. Some require strictly stick welding, which he and Hobbs usually accomplish with AWS E6010 and 7018 stick electrodes, while others require a combination of stick welding and flux-cored welding. Additionally, the projects vary between requirements for gas-shielded flux-cored wires, like AWS E71T-1 wires, and self-shielded products like E71T-8JD H8 wires. Also, some projects entail strict attention to established codes, including the AWS (American Welding Society) D1.5M/D1.5:2002 for bridge welding and AWS D1.1/D1.1M:2006 Structural Welding Code – Steel. But regardless of which requirement Jolson encounters, the contracts he accepts involve close attention to detail, high quality welds and good productivity. For years, Jolson faithfully used a competitor’s wires to achieve those results, until a major pipe project a year ago prompted him to seek out new products that could meet the tight timeline imposed by the hiring company. “We had the option to take on a major project in San Francisco. It was 96-inch diameter pipe job that the company wanted welded on a short timeline,” explains Colleen Jolson. “That’s when we met up with our local Bernard and Hobart Brothers’ representative, Willie Stubblefield. We wanted to look at new products that could help us meet that deadline.” Working with Stubblefield, whom the Jolsons met through a local welding distributor, they set up tests for different types of welding equipment and wires. The goal was to find products that allowed Jolson to weld faster and also that would be user-friendly for the other welding operators that joined them on the project. According to Colleen Jolson, the company (with the exception of fulltime employee, Hobbs) brings on welding operators to meet the demands of a given project. So, while highly experienced, their skill sets often vary. Jolson decided to convert to Hobart Brothers’ Fabshield XLR-8 self-shielded flux-cored wire paired with Bernard’s Dura-Flux guns, which he has been a loyal user of for some time. For gas-shielded welding, he chose to pair his trusted Bernard Q-Guns with Hobart’s Excel Arc 71 flux-cored wire. He’s been using the products together ever since. Jolson was introduced to Bernard’s Dura-Flux gun when he purchased his first SuitCase® X-TREME™ VS wire feeder from Miller Electric Mfg. Co., sister company to both Bernard and Hobart Brothers. The Dura-Flux gun came standard with the feeder. Since then, he says he’s continued using the gun because of its durability and ease of maintenance—features that together have added to his company’s productivity increases. “For me, one of the most important features is the microswitch inside the trigger. It’s water resistant, so if it’s raining or we drop the Dura-Flux in a puddle we can pick it up and go right back to work, as long as all other components are dry,” explains Jolson. The microswitch Jolson refers to is a feature that Bernard added specifically to help increase the durability of the gun in harsh construction environments. Its sealed design helps keep dirt, dust and water from entering the trigger and damaging the internal components. Jolson also likes that he can change out the contact tip on the Dura-Flux gun without tools and says that the gun’s small trigger guard makes it easier for him to maneuver around difficult joints and is more comfortable to hold for long periods of time. Most competitive self-shielded guns have a large heat shield, which he said would often get in the way when he welded in tight areas. But the best part of the Dura-Flux gun according to Jolson? It allows him, Hobbs and his other welding contractors to get a high volume of work done—fast. “We average probably 60 pounds of wire a day going through a gun with only one guy welding,” he says. “That’s a lot of wire.” In this case, it’s Hobart Fabshield XLR-8 self-shielded .072-inch diameter wire that he is using, an all-position wire that provides the high deposition rates and good impact strengths that he and his team need. The wire also has the optional D designator under AWS A5.20:2005 specifications, making it usable for the strict AWS D1.8 Demand Critical welds that Jolson often requires. Fabshield XLR-8 wire also offers a large voltage window and is particularly well suited for vertical-up welds at high current levels. Jolson operates the wire at approximately 19 to 25 Volts and 180 to 350 IPM (inches per minute), depending on the application and explains that the ability to run the wire at such a wide range of IPM helps him and his team stay productive. He says the Fabshield XLR-8 also simplifies set up and makes it easier for the range of skill sets that his contracted welding operators bring to the job. “I could put any guy on the job—from a really experienced welder to a novice and we won’t have any IPM issues. We don’t have to make sure that our wire speed is right on the money,” Jolson explains. “We just set our voltage and amperage and the guys can tinker with the wire speed a bit.” And while Jolson depends on his Dura-Flux gun and Fabshield XLR-8 wire, other parts of his welding arsenal help keep the company’s productivity on track, too. After Jolson discovered Bernard’s Dura-Flux gun, he liked it so much that he sought out an option for his gas-shielded applications. The result? With the help of Stubblefield, he customized a Bernard Q-Gun with the exact neck, consumables and cable length for his applications. (Bernard allows customers like Jolson to create their own style MIG Gun with their online Configurator or by working with a company representative or distributor). In this case, he built a MIG gun with an OXO-style handle and Bernard’s exclusive Centerfire consumables, and then added a six-inch flexible neck. He also uses Bernard’s Jump Liners. “Like the Dura-Flux gun, the Q-Gun has been really convenient, especially welding in tight spots,” explains Jolson. “Plus, it’s very easy to use and maintain—very user friendly. I don’t know that I’ll ever change from it.” According to Jolson, the Bernard Jump Liners have added measurably to his productivity increases. In fact, he estimates that it takes him or Hobbs approximately two to three minutes to change a Jump Liner compared to the 20 or more minutes to change a conventional MIG gun liner. Bernard Jump Liners connect with standard liners at the base of the Q-Gun’s rotatable neck and run through the most common wear point up to the contact tip. Jolson doesn’t have to replace (or trim) the entire gun liner when it becomes worn at the neck (the most common wear point). The jump liner stays with the body tube and the main liner stays within the gun. “It [the Jump Liner] saves me a lot of time because we don’t have to tear the whole gun apart in the middle of a welding process,” he explains. “We just remove the gooseneck, pop out the Jump Liner and slide in a new one. It’s very cost effective, and it gets us back to work faster.” Reducing downtime and adding to his productivity are the Centerfire consumables (contact tips, diffusers and nozzles) that Jolson uses on his Q-Gun. Centerfire series contact tips ‘drop in’ the gas diffuser and lock in place by tightening the nozzle. The nozzles feature a built-in spatter shield to protect the gas diffusers and provide smooth gas flow. “I use a small nozzle for getting into tight spots. Some people think that I’ll have gas diffusion problems because of that, but I just don’t,” says Jolson. “The holes inside the nozzle distribute the gas evenly. There’s not a problem with that. Plus the contact tips last longer than screw-on tips. I would say three to four times longer.” Jolson couples his Q-Gun with Hobart Brothers’ gas-shielded wire, Excel Arc 71—a change that he says has helped the company’s productivity in several ways, including improving weld quality and reducing cleanup. The company uses a .045-inch diameter wire, which Jolson and Hobbs operate at 19 to 24 Volts and approximately 175 to 500 IPM using 100 percent CO2, a set up that they say gives them the exact quality and travel speed they want. In many cases (as the specifications for a given project allow), Jolson says that he and his team can use the wire for the root, fill and cap passes, all with minimal downtime for interpass cleaning. He explains, “We usually run two- or three-foot passes at a time. By the time we get halfway through, usually the slag is already falling off.” The Excel Arc 71 also gives the team the versatility to weld a variety of different size welds—ranging from as thin as ¼ inch to as large as 1 inch, and produces very little spatter in the process, features that keep productivity high and downtime for cleanup at a minimum. “With competitive wires, I find that they are a little more finicky. I get a lot of spatter even if I mess with the gas, voltage and IPM,” says Jolson. “I don’t have time for that. I need to get the job done, and with the Excel Arc 71, we don’t have to worry about those problems.” So what’s the bottom line to benefits like these and the others that Jolson has experienced in the last year? According to him, pairing the Fabshield XLR-8 and Excel Arc 71 welding wires with his Bernard Dura-Flux guns and Q-Guns, respectively, has had a significant impact on his company’s productivity—to the tune of a 30 percent increase. “The changeover has really worked out good for our company,” says Jolson. “We can be a lot more competitive with our bidding now. And a lot more productive.” That’s important for someone like Jolson who never knows what project he’ll be taking on week-to-week, but needs to be prepared for whatever comes down the pipe. Self-shielded flux-cored arc welding (FCAW) has been a viable welding process for structural steel erection, heavy equipment repair, bridge construction and other similar applications for many years. That’s not surprising, as it offers high deposition rates, excellent chemical and mechanical properties, and the weldability required for these jobs. Still, it doesn’t mean that the process is without its challenges. Fortunately, with some know-how and a bit of practice, you can prevent some of the common problems associated with the process and gain the weld quality you need. Wire feed stoppages and malfunctions are common problems on many job sites and they can cause a considerable amount of downtime. The two most prevalent type of wire feeding problems—burnback and birdnesting—tend to extinguish the arc prematurely, which in turn can lead to weld defects. Burnback occurs when the wire melts into a ball at the end of the contact tip and is most often the result of too slow of a wire feed speed and/or holding the welding gun too close to the workpiece. To prevent the problem, be sure to use the correct feed speed for your application and maintain a distance from contact tip to the work of no further than 1 1/4-inch. To prevent birdnesting—a tangle of wire that halts the wire from being fed—during FCAW welding, always use knurled V- or U-groove drive rolls in your wire feeder. Compared to a GMAW solid welding wire (which uses a smooth V-groove drive roll), FCAW wire is much softer (due to its tubular design) and if you use the incorrect drive roll, it can easily compress the wire. Additionally, setting the correct drive roll tension can prevent the wire from flattening and becoming tangled. To set the proper tension, begin by releasing the tension on the drive rolls. Increase the tension while feeding the wire into the palm of your welding glove and continue to increase the tension one half turn past wire slippage. Other causes of birdnesting include blockages in the liner, improperly trimmed liners or using the wrong liner. Promptly replace your liner if you find a blockage during your routine inspection of your welding gun and cables, and always trim the liner (using the correct tools) according to the manufacturer’s recommendation. Be certain that the liner does not have any burrs or sharp edges and always use the correct size liner for your diameter of welding wire. Porosity and wormtracking are both common weld discontinuities that can weaken the integrity of your welds. Porosity results when gas becomes trapped in the weld metal and can appear at any specific point on the weld or along its full length. To prevent this problem, remove any rust, grease, paint, coatings, oil, moisture and dirt from the base metal prior to welding. Using filler metals with added deoxidizers also helps weld through such contaminants, but these products should never replace proper pre-cleaning. Next, maintain an appropriate electrode extension or stick-out. As a general rule, the wire should extend no more than 1 1/4-in. beyond the contact tip. To prevent worm tracking—marks on the surface of the weld bead caused by gas that the flux in the core of the wire creates—avoid excessive voltage for your given wire feed setting and amperage. It is best to follow the parameters recommended by the filler metal manufacturer for the specific diameter of welding wire. If worm tracking does occur, reduce your voltage by increments of one half volt until you eliminate the problem. Slag inclusions occur when the slag generated by the molten flux in the wire’s core becomes trapped inside of the weld. There are four major causes of slag inclusions, all of which can be prevented with proper welding techniques. First, avoid incorrect weld bead placement, especially when making multiple passes on thick sections of metal, such as needed for the root passes of welds or wide v-groove openings. Be certain to provide sufficient space in the weld joint for additional passes, particularly on joints requiring multiple passes. Second, maintain the correct travel angle and travel speed. In the flat, horizontal, and overhead positions your drag angle should be between 15 and 45 degrees. In the vertical up position, your drag angle should be between 5 and 15 degrees. If you experience slag inclusions at these angles, you should increase your drag angle slightly. Maintain a steady travel speed; if you travel too slowly, the weld puddle will get ahead of the arc and create slag inclusions. Next, maintain proper weld heat input, as too low of welding heat input can also cause slag inclusions. Always use the manufacturer’s recommended parameters for a given wire diameter. If slag inclusions still occur, increase the voltage until the inclusions cease. Finally, be certain to clean thoroughly between weld passes, removing any slag with a chipping hammer, wire brush or grinding before beginning your next weld pass. Like other weld defects, undercutting and lack of fusion can both affect the quality of your welds and preventing them can go far in reducing downtime and costs for rework. Undercutting occurs when a groove melts in the base metal next to the toe of the weld, but is not filled by the weld metal. It causes a weaker area at the toe of the weld and often leads to cracking. Using the proper welding current and voltage are key to preventing undercutting (remember to follow your welding parameters), as is adjusting to the right gun angle. Maintain a travel speed that allows the weld metal to fill the melted-out areas of the base metal completely, or if you are using a weaving technique, pause at each side of the weld bead. To prevent lack of fusion, the failure of the weld metal to fuse completely with the base metal (or the preceding weld bead in multi-pass applications), maintain the correct work angle and heat input. Obtain the correct angle by placing the stringer bead in its proper location at the joint, adjusting the work angle or widening the groove to access the bottom during welding as needed. Keep the arc on the trailing edge of the welding puddle and maintain a gun angle drag of 15 to 45 degrees. If using a weaving technique, momentarily hold the arc on the groove sidewalls when welding. Increase your voltage range and/or adjust the wire feed speed as necessary to obtain complete fusion. Also, if you feel that the wire is getting ahead of the work puddle, simple adjustments, such as increasing travel speed or using a higher welding current, can prevent problems. Finally, be certain to clean the surface of the base metal prior to welding to remove contaminants to prevent lack of fusion. Maintaining the appropriate heat input during welding is key to avoiding problems like excessive penetration. Excessive penetration occurs when the weld metal melts through the base metal and hangs underneath the weld. It most often results from too much heat. If the problem occurs, select a lower voltage range, reduce wire feed speed and increase travel speed. Conversely, selecting a higher wire feed speed, a higher voltage range and/or reducing travel speed can prevent problems like lack of penetration—the shallow fusion between the weld metal and the base metal. In addition, prepare the joint so as to permit access to the bottom of the groove, while also maintaining proper welding wire extension and arc characteristics. Self-shielded FCAW is a reliable process for many construction applications, but obtaining high quality welds with it isn’t a matter of luck. It’s the result of good welding technique, the proper choice of parameters and your ability to prevent problems—or identify and rectify them quickly. Remember, arming yourself with some basic information will allow you to prevent most common problems associated with self-shielded FCAW welding without sacrificing time or quality.
A welding operator typically spends much less than 50 percent of an eight-hour day engaged specifically in the act of welding, with the remaining portion allocated to joint preparation, part fit-up and movement, and other activities that contribute to the throughput of the welding operation. Still, during that arc-on time, the importance of helping the welding operator remain comfortable and cool can’t be stressed enough. Simply stated, by ensuring good operator comfort companies can lessen the chances of injuries associated with repetitive movement, reduce overall operator fatigue and lessen insurance rates or worker compensation claims. The result? A more content employee and the potential for greater productivity and profitability. Not surprisingly, the MIG gun that a welding operator uses can have a direct impact on comfort. Factors including the MIG gun’s amperage, along with its handle and cable styles all contribute to the equipment’s weight and maneuverability, and should be considered when selecting a MIG gun for the welding operation. Other factors, such as protecting against the MIG gun’s heat output is also critical, both to the welding operator’s comfort and safety, too. It is not uncommon in a welding operation to find MIG guns that are rated at a higher amperage than necessary for the given application. One of the reasons for this occurrence is the common misconception that the MIG gun used should be rated to the highest amperage at which the welding operator will be welding. For example, if an application requires 400 amps, it’s very common to find a welding operator using a 400-amp gun. While the gun in this example will undoubtedly do the job, the higher amperage gun also weighs more than a lighter amperage one and tends to be less flexible—both factors that impact the welding operator’s comfort and his or her ability to maneuver the MIG gun easily. As a general rule, selecting the lightest, most flexible MIG gun for the application is the best choice. In the case of a 400-amp application, a MIG gun rated at 300 amps may suffice. There are two reasons for this assertion. First, MIG gun amperages, which are established by CE (Conformité Européenne or European Conformity) in Canada and NEMA (National Electrical Manufacturer’s Association) in the United States, reflect the temperatures above which the handle or the cable on a MIG gun become uncomfortable. They do not indicate the point at which the MIG gun risks damage or failure. Secondly, given that a typical welding operator (as mentioned previously) typically welds only a small portion of the workday, it is highly unlikely that he or she would be operating the gun at full amperage and full duty cycle at all times. Duty cycle is defined by the amount of arc-on time in a 10-minute period that the equipment can be operated at maximum capacity. Some MIG guns will offer 100 percent duty cycle, while others are rated 60 percent or below. As a result of these two factors, a lower amperage model can often be used for a slightly higher amperage application without damaging the gun or heating up to the point of making the welding operator uncomfortable. The lower amperage MIG gun also offers the added benefit of being lighter and more flexible for the welding operator. In many cases, these models will also be more cost effective. It is important, however, to research the MIG gun’s duty cycle prior to purchasing it in order to ensure it offers the necessary capacity for the application. Another important factor in maintaining a good comfort level for the welding operator is selecting a MIG gun with the appropriate handle, neck and cables for the application. Typically, as a MIG gun’s amperage decreases so too does the size of the gun handle and the cable, which makes the equipment that much more comfortable for the welding operator. Because every application is different, however, it is not always possible to use a lower amperage MIG gun. For that reason, it is important to implement other safeguards to keep the welding operator comfortable. First, it is important to match the handle style to the welding operator’s preference. MIG gun manufacturers often offer handles in curved and straight models, either of which may be more comfortable for one welding operator compared to another. The goal for both types of handles, however, is the same: to choose a light-weight, comfortable style that also meets the MIG gun and application’s amperage and duty cycle requirements. As a rule, a smaller handle will be easier for the welding operator to maneuver. Additionally, some MIG gun manufacturers offer ventilated handles, which help reduce heat and are more comfortable to hold when welding for longer periods of time. In some instances, a water-cooled MIG gun may provide the smaller size desired for an application and would be a good choice to reduce operator fatigue on higher amperage applications, especially in a shop setting. As when selecting MIG gun or a handle, a good rule of thumb is also to select the smallest and shortest power cable possible that can still meet the needs of the application. Smaller and shorter power cables are lighter and more flexible and can, therefore, reduce operator fatigue. They can also minimize clutter in the work space and prevent excessive coiling that may be cumbersome for the welding operator to rectify and that could also lead to poor wire feeding. An added advantage is that smaller and shorter cables tend to be less expensive, as well. In addition to fixed necks, many MIG guns are available with rotatable and flexible necks in various lengths and angles that can increase the welding operator’s comfort. The advantage of these styles is that they provide the welding operator with the option to select one that will best suit the joint access required for an application. For example, flexible necks can be easily adjusted to fit different welding angles and reach difficult joints that may be restricted or otherwise awkward to reach. This features helps keep the welding operator from straining to reach a particular weld joint and risking fatigue or injury. Similarly, rotatable necks are a good option for welding out-of-position (including overhead), as they can be adjusted to reach the weld joint without changing the gun handle or its position. Both of these type of MIG gun necks can also simplify inventory and reduce downtime for neck changeover, as they can be used on multiple applications. Some MIG gun manufacturers also offer neck couplers, which allow the welding operator to connect multiple necks together to reach especially difficult joints comfortably. There are two main types of heat in a welding operation: radiant heat from the arc and resistive heat from the cable. To protect against both types of heat, it is important that the welding operator always wear the proper protective apparel, including a helmet, welding gloves and a welding jacket or sleeves. Radiant heat is heat that reflects from the welding arc and base metal back to the handle. If the welding operator welds on shiny materials, such as aluminum or stainless steel, it will likely reflect more heat that a duller mild steel, for example. Using a longer neck to the MIG gun can help protect the welding operator from radiant heat by placing the handle further back from the arc. Adding a neck grip can further increase comfort. Neck grips are available through select MIG gun manufacturers and are usually composed of high-temperature silicon rubber. They slide over the neck to protect the welding operator from heat exposure and related fatigue. These accessories offer the added benefit of increasing control for welding operators who like to rest the neck on their hand or forearm, using it as a pivot point to maneuver the MIG gun. Because the neck can also carry heat to the handle, it is important to use front-end consumables—nozzles, contact tips and diffusers—that remain cool. Be certain to look for consumables that fit snugly together, as this feature will minimize electrical resistance and reduce heat output. Also, consider the shielding gas being used for the applications as a means to minimize heat in the welding operation and help the welding operator remain cooler. Argon, for example tends to create a hotter arc than does pure CO2 shielding gas. In fact, MIG guns operating with Argon in the mix often reach the MIG gun’s rated temperature at a lower amperage than when using pure CO2. While it may not be possible to choose which shielding gas to use (a particular application often specifies gas usage), if operating an Argon applications, a welding operator could take other precautions (as mentioned above) to help stay cool. To protect against resistive heat, it is important to have a large enough power cable for the job—but not too large as to make it difficult to maneuver—and also to prevent kinking of the power cable whenever possible. When selecting a MIG gun for any application, the goal is two-fold: to have the right equipment for the application and to keep the welding operator as comfortable as possible. Through careful selection of the proper amperage MIG gun, along with choosing an appropriate handle, cable and neck that goal is reasonable to achieve. Also, by taking precautions against heat exposure, a welding operator can ensure that he or she will be able complete the required welds with minimal discomfort. Remember to research the MIG guns available in the market place, in addition to the application at hand. Consider the actual amount of time the welding operator will be welding and on what type of material, too. Doing so can help ensure that the selected MIG gun strikes a good balance between size and capacity.
Everyone is trying to save money these days. From implementing lean practices to repairing equipment instead of purchasing new, companies are seeking ways to reduce costs without sacrificing quality. Selecting the right MIG gun consumables for your welding application can also help. Not only can the right consumables minimize unscheduled downtime for changeover, but they can also reduce the need to rework weld defects caused by a poorly performing contact tip, nozzle or liner. The bottom line? You can spend more time welding, gain greater productivity and lower your costs. Following are some suggestions for selecting the most appropriate MIG gun consumables for your application and ways you can best care for them. Liners are responsible for guiding the welding wire from the wire feeder, through the gun cable and up to the contact tip. They are typically composed of steel coils, but can also be made of nylon or Teflon®, the latter of which is used for welding with aluminum wire. Selecting a liner is a relatively straightforward process: you need to match the liner’s inside diameter (within a specific range) to the diameter of wire you are using. For example, if you are welding with a .035-inch wire, you can use a liner that measures .035 to .045 inches in diameter. Making this match helps prevent wire-feeding problems that can lead to poor arc stability, bird-nesting (a tangle of wire that prevents the wire from feeding) and/or weld defects. Also, using premium quality liners is best, as these maintain a more consistent inside diameter than less expensive ones and provide better feeding performance. To prevent shielding gas leaks that can increase costs and jeopardize gas coverage of your welding puddle, make certain that your liner has a good O-ring connection at the back of the liner and that you select liners with a durable coating. Replace your liner at a regularly scheduled time and always follow the manufacturer’s recommendation for trimming and installation. Poorly trimmed liners, liners that are worn excessively or ones that are kinked from use can easily cause wire feeding problems or an erratic arc that leads to poor weld quality. They can also cause excessive spatter that will require post-weld grinding, minimizing throughput and adding to your overall costs. Some manufacturers offer partial liners that replace only the most commonly worn part of liner (along the length of the MIG gun) instead of the entire liner. These partial liners help reduce downtime for changeover as they usually take about half the amount of time to install compared to a full-length liner. While they may look like a small, and perhaps insignificant, part of the overall welding system, contact tips play a critical role in helping achieve good weld quality, reducing costs for downtime and minimizing rework. In addition to helping direct the welding wire to the weld puddle, contact tips are responsible for transmitting the current to that wire in order to initiate the arc. The contact tip you select should correspond with the diameter of welding wire you are using. Typically, contact tips are available to accommodate wire diameters ranging from .023 to 1/8 inches. Depending on the type of joint your application requires, you may need to select a tapered style contact tip. These contact tips are good for applications that have restricted joint access, but they tend to be a bit more delicate than non-tapered contact tips. They should be coupled with a tapered nozzle. If joint access is not a factor in your application, however, choosing a non-tapered contact tip is the best option as it has more mass and will last longer. Different manufacturers offer either threaded or non-threaded styles of contact tips. Threaded contact tips are the most common and, as their name implies, they are held in place in the gas diffuser by threading or twisting them. Non-threaded contact tips, conversely, drop into the gas diffuser. This latter style of tips can be rotated when the contact tip starts to wear on one side (called keyholing) in order to create a new wear surface, extend the life of the contact tip and prevent arc instability that can in turn lead to spatter and rework. Non-threaded contact tips also tend to be easier to change out after a burnback, which is the formation of a weld in the contact tip. It most often occurs because of placing the contact tip too close to the workpiece or using too slow of a wire feed speed. Regardless of whether you choose a threaded or non-threaded style of contact tip, it is important that you install these according to the manufacturer’s recommendations. Doing so will help ensure a good electrical connection and, with it, reliable welding performance and quality. Contact tips are generally available in sizes small or large and also in standard or heavy-duty varieties. If you are welding on higher temperature applications (generally, 300 amps and above) you should select a large contact tip, as these have greater mass and provide better cooling capacity than smaller contact tips. For higher amperage applications that also require prolonged welding, heavy-duty contact tips can provide greater conductivity, improve arc starts and they tend to provide longer lasting performance. Lighter amperage applications (generally, below 300 amps) are well-suited to using small, standard style contact tips. To ensure the best welding performance, inspect the contact tip for spatter build-up on a regular basis and replace as needed. Waiting too long to replace a damaged contact tip can lead to arc irregularities and poor weld quality, not to mention unscheduled downtime for replacements, which can cut into your productivity and cost you money. Depending on your application there are a variety of styles of nozzles from which to choose. Like contact tips, nozzles are an important part of gaining good weld quality and reducing costs. The main function of these components is to direct shielding gas to the weld. For that reason, you want to select a high-quality nozzle that is capable of providing smooth gas coverage and resisting damage (e.g., dents, scratches, etc.). Usually, manufacturers offer either brass or copper nozzles. Brass nozzles provide good protection against spatter, while copper nozzles withstand heat better, particularly on heavy-duty applications. There are two main styles of nozzles — threaded and non-threaded — as well as a variety of different shapes and sizes. Threaded nozzles tend to maintain a more secure connection than non-threaded styles, which protects against shielding gas leaks that can lead to weld defects like porosity. These nozzles also help keep the contact tip centered for greater accuracy. Non-threaded nozzles, however, are easier to change over. Nozzles are available with small and large varieties and a range of inside diameter measurements, often from 3/8 to 5/8 inches. Ultimately, the best option for any application is to use the largest nozzle possible that still provides you access to the joint. Doing so provides greater gas coverage to protect against contaminants. For restricted joints, however, you will need to use a small, tapered nozzle that allows you to place the contact tip close to the weld puddle. Or if you have a high-amperage application that requires high gas flow rates, select a large diameter nozzle, as it provides the best shielding gas coverage. Some MIG consumable manufacturers provide nozzles that keep the contact tip at a fixed position: flush, recessed or extended. Each provides distinct attributes. For example, if you are welding in a short-circuit transfer mode, a nozzle that keeps the contact tip flush to the end of the nozzle or slightly extended helps minimize the spatter that tends to be generated in this welding process. Similarly for spray arc transfer or pulsed spray mode when welding with solid wire, having a nozzle that keeps the contact tip slightly recessed can help the contact tip operate at cooler temperatures and provide greater shielding gas coverage. For all styles and sizes of nozzles, regular inspection for spatter is crucial to achieving good gas coverage. Also, careful handling and storage of these consumables is important. Always wear gloves when changing out nozzles to prevent debris or oils from adhering to them and entering the weld puddle. To prevent damage, keep them in the original packaging until you are ready to use them. Remember, whether you are selecting a nozzle, contact tip or liner, having the right MIG gun consumable for your application can go a long way in reducing unnecessary downtime and lowering your overall costs.
For structural steel applications, bridge construction and heavy equipment repair, self-shielded flux-cored welding (FCAW-SS) has become a standard and reliable process due to its ability to provide high-deposition rates and good weld quality. It also provides the chemical and mechanical properties necessary to withstand low temperatures and is equally well-suited for ship and barge construction applications. Like every welding process, however, self-shielded FCAW has its challenges. From selecting the right power source and welding gun to determining the best filler metal for the application, it’s important to take care with each component in order to obtain the best welding performance. It’s also important to know the causes of and solutions to problems when they arise. Doing so can save you time, money and frustration. Here are some frequently asked questions about self-shielded FCAW problems, along with some advice on how to remedy them. Slag inclusions are common problems that can arise during the self-shielded FCAW process. They occur often in out-of-position welding and are the result of molten flux from inside the welding wire becoming trapped inside the weld. The potential for slag inclusions is also prevalent during multi-pass welding applications. There are several ways to prevent slag inclusions. First, be certain to maintain the correct travel speed and angle. When welding in the vertical-up position, keep your gun’s drag angle between 5 and 15 degrees and increase it as necessary if the problem still occurs. If you are welding in the flat or horizontal positions, maintaining a drag angle between 15 and 45 degrees should prevent the problem. Secondly, always use the filler metal manufacturer’s recommended voltage for your welding wire to ensure that you are maintaining the proper heat input. Too low of heat input can cause slag inclusions. Other ways to prevent slag inclusions include cleaning thoroughly between weld passes to remove any slag (use a chipping hammer, grinder or wire brush) and correct bead placement. Allow enough space in the weld joint, especially on root passes and wide groove openings, for the weld metal to fill it. Burnbacks are the result of the welding wire melting into a ball and fusing to the end of the contact tip, and they are a common cause of downtime in the self-shielded FCAW welding process. There are two main causes of this welding problem. Holding your gun too close to the joint or workpiece can cause burnbacks, as can using too low of a wire feed speed. You can prevent the problem by maintaining a work-to-contact-tip distance of no more than 1-1/4 inch. Also, use the correct wire feed speed for your application. When in doubt as to what that wire feed speed should be, contact your local welding distributor and/or consult the manual provided with your wire feeder. Lack of fusion often often occurs as the result of an improper gun angle. If you do not place the stringer bead in the proper location at the joint, the weld metal will fail to fuse completely with the base metal. This problem can also occur in multi-pass welding applications if the weld metal does not fuse with the preceding weld bead. A dirty work surface can also be the culprit. To prevent lack of fusion, be sure to clean thoroughly before the initial weld pass and in between passes if you have a multi-pass application. Adjust your work angle or widen the joint groove so that you can fully access the bottom of the joint. Maintain a gun angle drag of 15 to 45 degrees or hold the arc on the groove’s sidewall if you are using a weaving technique. Consider increasing your voltage range if you experience lack of fusion and adjust your wire feed speed and your travel speed until you see complete weld fusion. Bird-nesting can be caused by a number of factors. This tangle of wire, which prevents the wire from feeding properly through the wire feeder and gun, is often the result of using the wrong drive rolls in your wire feeder and/or setting the wrong drive roll tension. To prevent the problem, use knurled V- or U-groove drive rolls, as these prevent the soft FCAW wire from compressing. Also, set the proper drive roll tension by first releasing the tension on the drive rolls, then increasing it slightly while you carefully feed the wire into a gloved palm. Continue increasing the tension until you reach a half-turn past wire slippage. As with using the correct drive rolls, the proper drive roll tension keeps the FCAW wire from being crushed. Issues with the gun liner can also cause bird-nesting. These include using an improperly trimmed liner or using the wrong size liner for the given diameter of FCAW wire. To prevent bird-nesting, trim the liner according to the manufacturer’s recommendation, and make sure that there are no sharp edges on it afterward. Inspect your liner on a regular basis to look for blockages, and replace the liner if you find any. Good joint penetration is essential to having high-quality, sound welds, and the goal is to prevent too much or too little weld metal going into the joint. To prevent excessive penetration (weld metal melting through the base metal and hanging under the weld), maintain the proper heat input for your application. Lower your voltage range if the problem occurs, while also decreasing your wire feed speed and increasing your travel speed. Conversely, if you find that you are not gaining enough penetration into the weld joint (called lack of penetration — the shallow fusion between the weld and base metal), increase your voltage range and wire feed speed, but reduce your travel speed. Remember, too, to prepare your joint properly. You need to be able to access the bottom portion of the groove in order to maintain the proper wire extension and obtain the arc characteristics needed for a good quality weld. When possible, prepare the joint so that the material you are welding isn’t too thick. The best prevention against porosity — a weld defect that occurs when gas becomes trapped in a weld — is to clean your base material thoroughly before welding. Be certain to remove all dirt, rust, grease or oil, paint and other potential contaminants along the full length of the joint you plan to weld. When you begin welding, maintain a wire extension of no more than 1-1/4 inch beyond the end of the contact tip. For some applications, using a filler metal that contains additional deoxidizers can help prevent porosity, as these products can often weld through light contaminants. Remember, however, no filler metal should be a replacement for proper cleaning procedures. Like any welding process, there are a number of challenges you may encounter with self-shielded FCAW and those discussed here are by no means an exhaustive list. A trusted welding distributor and a welding equipment manufacturer are both good resources to help you address problems related to wire feeding, weld quality and more. And remember, the more that you know about the causes of welding problems, the faster you can resolve them and get back to work.
Selecting the right MIG gun for your welding application, and maintaining it properly, is just as important to your overall productivity as any other part of the welding operation. Unfortunately, MIG guns are very often an overlooked part of the welding system. The reality is, however, that in addition to being responsible for delivering the current, wire and shielding gas to the weld puddle, your MIG gun can also have a significant impact on your weld quality and your bottom line. Similar to selecting your power source or wire feeder, the goal is to find the most cost-effective MIG gun that is capable of providing you with the performance that you need for your welding application. Regularly executing preventive maintenance can then help you protect that investment. Here are some tips to help you select the right MIG gun for your application and maintain it properly. Choose the Right MIG Gun for Your Application It is a common misconception that a welding procedure requiring 400 amps, for example, also requires a 400-amp MIG gun capable of operating at those amperage levels 100 percent of the time (i.e., 100 percent duty cycle). The fact is you spend time moving parts, grinding, tacking and completing other such tasks as opposed to welding nonstop. That means that you can often purchase a smaller amperage MIG gun — a 300-amp model would suffice — for applications in which duty cycle is less than 100 percent (e.g., 60 percent) for less money and still have it operate at the appropriate capacity. A smaller, lower-amperage MIG gun also weighs less and can help reduce wrist fatigue that could lead to downtime. It offers the added benefit of being easier to maneuver, which can help improve weld quality, too, and lessen rework. When possible, using shorter power cables on your MIG gun can further minimize costs and downtime. As a general rule, shorter power cables are less expensive and, like a smaller MIG gun, offer better maneuverability. Shorter power cables also help minimize wire-feeding problems associated with kinking and coiling, so you can spend more time welding and less time resolving these issues. Other factors you should consider when selecting your MIG gun: Consider using the smallest handle that can still meet your amperage needs. As with a smaller gun, smaller handles are easier to maneuver and can lessen fatigue. Some manufacturers also offer ventilated handles that help reduce heat and make it more comfortable to use for longer periods of time. Maintaining Your MIG Gun Check the feeder connection: Regularly check the wire feeder connection (where the power pin plugs into the feeder) to be certain it is tightened properly and that there is no dirt or debris on it. Loose or dirty wire feeder connections can cause heat to build up, leading to voltage drops that adversely affect the welding arc and may cause premature gun failure. Tighten the connection according to the manufacturer’s specifications or replace the direct plug if necessary to obtain a secure fit. Also inspect the O-rings for cracks that could lead to gas leaks, and replace them as necessary. Gas leaks often cause spatter and porosity, which increases downtime for cleanup and rework. Properly care for your MIG gun liner: It is not uncommon during the course of welding for the MIG gun liner to become clogged with debris, particularly from the welding wire. Over time, however, this accumulation of debris can lead to poor wire feeding, bird-nesting and burnbacks that require downtime to rectify. To maintain your liner, you can use compressed air to clear out potential blockages when you change wires. Also, tracking the length of time it takes for your liner to wear can help you better know when to replace the next one before you encounter problems. Always follow the manufacturer’s recommendation for trimming and installing the liner to prevent kinking and wire-feeding problems. Inspect the handle and trigger: Typically these components require little maintenance beyond visual inspection. Regularly look for cracks on the handle or Check the MIG gun neck: Loose connections at either end of the neck can cause electrical resistance that leads to poor weld quality and/or consumable failures. Check regularly to ensure tight neck connections. Also, visually inspect the insulators on your MIG gun neck and replace if damaged. These insulators prevent electrically live components from exposure, ensuring your safety and the longevity of your equipment. Visually inspect the power cable: Power cable maintenance is a very important part of eliminating uncessary equipment costs. Regularly inspect the power cable for damage, including cuts or kinks, and replace it as necessary. Cuts in the cable can expose copper wire and lead to a potential shock hazard, while kinking obstructs gas flow and wire feeding. The latter can lead to weld defects and arc instability that require downtime to remedy. Be mindful of your consumables: Frequently inspect your MIG gun nozzle and contact tip for signs of spatter build-up, which can obstruct shielding gas flow and cause weld defects that will need to be reworked. Spatter build-up can also cause your consumables to fail prematurely. Replace both consumables if spatter build-up appears or clean according to the manufacturer’s recommendation. Also, be certain that these components (and the gas diffuser) are securely connected. Loose connections can increase electrical resistance, which in turn leads to poor welding performance and can shorten the life of your consumables, adding to your overall costs. Remember, just like the power source and wire feeder, your MIG gun can impact your weld quality, productivity and costs. Taking the time to select the proper MIG gun and maintain it regularly, however, can help this equipment last longer and ensure that you spend more time welding instead of resolving problems.
Weld flaws come in all shapes, sizes and degrees of severity. Yet one thing holds true regardless of the application or material on which they occur: They are a common, and costly, cause of downtime and lost productivity. They are also an occurrence that even the most skilled welder can experience. In the GMAW process, specifically, there are several typical weld flaws that can transpire. From porosity to undercut and burn through, each has multiple causes. Fortunately, there are also numerous cures that can help welding operators minimize their frustration over weld flaws and get back to work faster. When gas becomes trapped along the surface or inside of the weld metal, porosity occurs. Like other weld flaws, porosity results in a weak weld that must be ground out and reworked. Causes: Typically, inadequate or contaminated shielding gas is the culprit of porosity. Using a nozzle that is too small for the application, or a nozzle full of weld spatter, can also cause this weld flaw. Having a dirty base metal and/or extending the welding wire too far beyond the nozzle is an additional cause. On warm days, air currents from cooling fans can disrupt the shielding gas envelope around the weld puddle creating this problem. Another common cause is a poor seal or a loose fitting in the shielding gas channel through the welding gun. Any gas leaks have the potential to aspirate air into the gas flow. Cures: To correct porosity, ensure that that there is adequate gas flow (increasing it as needed), and replace any damaged gas hoses or GMAW gun components that may be causing leaks. Also, place a welding screen around the work area if welding outside or in an area inside that is particularly drafty. Check that the nozzle being used is large enough for the application and replace with a larger one if it is not. Remove any spatter build up in the nozzle. Extend the welding wire no more than 1/2 inch beyond the nozzle and make certain that the base metal is clean prior to welding. Slowing travel speed to gain greater shielding gas coverage can also combat porosity, as can keeping the nozzle within 1/4- to 1/2-inch of the base metal during welding. Just as its name implies, burn through results when the weld metal penetrates fully through the base metal, essentially “burning through” it. It is most common on thin materials, particular those that are 1/4 inch or less. Another weld flaw, excessive penetration (too much penetration into the weld joint), can very often lead to burn through. Causes: Excessive heat is the primary cause of burn through. Having too large of a root opening on the weld joint can also result in burn through. Cures: If burn through occurs, lowering the voltage or wire feed speed can help rectify the problem. Increasing travel speed helps, too, especially when welding on aluminum, which is prone to heat build-up. If a wide root opening is the suspected cause of burn-through, increasing the wire extension and/or using a weaving technique during welding can help minimize heat input and the potential for burn through. Incomplete joint penetration or lack of penetration results when there is shallow fusion between the weld metal and the base metal, rather than full penetration of the joint. It can often lead to weld cracking and joint failure. Causes: Insufficient heat input and improper joint preparation are the main causes of incomplete joint penetration. The shielding gas mixture and wire diameter can also be a factor. Cures: There are several cures for incomplete joint penetration, including using higher wire feed speed and/or voltages. Reducing travel speed also allows more weld metal to penetrate the joint, as does preparing and designing the joint properly. The joint should allow the welding operator to maintain the proper welding wire extension (no more than 1/2 inch beyond the nozzle) and still access the bottom of the weld joint. Make sure that the shielding gas or gas mixture, wire type and diameters are recommended for the application. Undercutting is a groove or crater that occurs near the toe of the weld. When this weld flaw occurs, the weld metal fails to fill in that grooved area, resulting in a weak weld that is prone to cracking along the toes. Causes: Excessive heat, as well as poor welding techniques, can both lead to undercutting on a weld joint. Cures: Reducing the welding current and voltage is the first step to rectifying undercutting. Using a weaving technique in which the welding operator pauses slightly at each side of the weld bead can also help prevent this weld flaw. Additional cures include reducing travel speed to a rate that allows the weld metal to fill out the joint completely and adjusting the angle of the GMAW gun to point more directly toward the weld joint. Hot cracking typically appears along the length of a weld or directly next to it almost immediately after the weld puddle solidifies. This weld flaw occurs at temperatures greater than 1,000 degrees Fahrenheit (538 Celsius). There are multiple variations of hot cracking including centerline, bead shape and crater cracks. Causes: Hot cracking can result from several factors. These include poor fit-up or joint design, creating too thin of welds and welding at too high of voltages. High levels of base metal impurities can also cause this weld flaw. In some cases, high levels of specific alloys (boron, for example) in filler metals can cause the problem. Cures: Having the proper joint design and good part fit up is one way to help prevent hot cracking, as it keeps the weld puddle the appropriate size and minimizes the chance of the throat of the weld being too thin. In the case of crater cracking, in particular, using a backfill technique (backing up to fill in the joint fully) can minimize cracking by adding throat thickness to the crater weldment. Careful filler metal selection and shielding gas selection is also imperative. Causes: Most often the cause of incomplete fusion is an incorrect gun angle, although contaminants on the base metal can also cause this weld flaw. In some instances, insufficient heat can be the culprit. Cures: First, clean the base metal properly prior to welding, making sure it is free of dirt, oil, grease or other debris. Next, welding operators should place their GMAW gun at an angle of zero to 15 degrees in order to access the groove of the weld joint fully and keep the arc on the leading edge of the weldpuddle. Increase travel speed as necessary to keep the arc from getting too far ahead of the weld puddle. For joints requiring a weaving technique, holding the arc on the sidewall for a moment can help prevent incomplete fusion. Make certain, too, that there is enough heat input to fuse the weld metal and base metal fully. Increase the voltage range and adjust the wire feed speed as necessary to complete the weldment. Remember, even the most skilled welding operators can experience weld flaws. The key to keeping them from affecting productivity and increasing costs in the welding operation is to identify and rectify the problems as quickly as possible. Proper maintenance of the welding equipment is also imperative. Repair or replace any worn or defective items.
With so many factors to monitor — equipment, weld procedures, filler metals and consumables — it’s inevitable that mistakes will occur in most welding operations on any given day. Human error dictates that a welding operator can easily set a power source and wire feeder to the wrong parameters or trim and install a MIG gun liner improperly. But there are other mistakes that can occur in welding operations on a regular basis — ones that many companies may not even realize that they are making. The reality is, however, that these mistakes can have a significant impact on quality, productivity and a company’s bottom line. Fortunately, they don’t have to happen. Consider these top 10 mistakes involved in running a welding operation, along with some recommendations for solving them. Storing filler metals in an area where they are prone to accumulating moisture or exposed to other contaminants (e.g., dirt, oil or grease) can have an adverse effect on their welding performance. To prevent damage, companies should store filler metals in a dry, clean area with a relatively constant temperature until they are ready for use. Spools and coils of wire that are kept on the wire feeder for an extended period should be covered securely with a plastic bag or removed from the wire feeder and stored in the original packaging. An enclosed wire feeder can also protect against contaminants. Such precautions prevent damage that can lead to poor weld quality, and ultimately, rework. It is important for companies to use the best equipment for the job. Repurposing old or dilapidated power sources, welder/generators or wire feeders can cause quality issues, not to mention downtime and additional costs for troubleshooting problems that inevitably arise from using dated equipment and technology. Instead, companies should consider the newer technologies available in the marketplace, recognizing the advantages these can offer in terms of improving weld quality and productivity. In most cases, newer equipment can provide companies with a quick return on investment and greater long-term savings – in a relatively short payback period. Newer technologies often offer benefits like improved power efficiency, better deposition rates, lower weld prep time and faster training, all of which ultimately add up to greater arc-on time and productivity. Performing a thorough cost-savings analysis before buying new equipment can help companies assess their potential return on investment, as well as justify the capital expenditure. Using a too-low or too-high amperage MIG gun can lead to unnecessary costs for purchasing and replacing this equipment. Welding operators rarely spend the entire day welding or welding continuously, as there is downtime for part preparation, movement and/or fixturing. For that reason, it may be possible to use a lower amperage MIG gun or one with a lesser duty cycle on some applications. For example, using a lighter and smaller 300-amp MIG gun instead of a 400-amp model can provide welding operators with greater maneuverability and reduce downtime for fatigue. Lower amperage MIG guns tend to cost less, as well. Conversely, on higher amperage applications and/or those that require longer periods of welding, it is important to use a higher amperage gun. Skimping and purchasing a lower amperage MIG gun in this situation can lead to overheating, premature failure and greater long-term costs. Companies should consult with a trusted welding distributor for MIG gun recommendations for their application. It is not uncommon for companies to preheat too little or skip this portion of the Preventive maintenance (PM) is a frequently overlooked part of the welding operation, but it is critical to preventing unscheduled downtime and keeping repair costs low. A well-performed PM program can also help increase productivity, extend equipment life and create a workplace philosophy that encourages shared responsibility for, and interest in, preserving the integrity of the welding equipment. Companies should develop a regular timetable to inspect their power sources, wire feeders and MIG gun or TIG torches during scheduled downtime in production. Between welding shifts is often enough time to perform routine inspections. Checking consumables regularly for spatter build-up — and replacing these components as needed — is also an important part of a viable PM program. Using the correct type and/or mixture of shielding gas can help companies prevent weld defects, minimize excessive spatter and reduce costs for rework or post-weld cleanup. Shielding gases also determine arc characteristics and weld penetration on a given application. Straight CO2 provides good weld penetration, but it is prone to spatter and has a less stable arc than mixtures that include argon. High argon mixtures (a minimum of 85 percent argon for solid wire or as low as 75 percent for metal-cored wires) are the best choice. These mixtures can be used in the spray transfer process to promote higher deposition rates and generate less spatter. For TIG welding, the appropriate argon/helium mixture can improve speed, quality and arc characteristics. For both MIG and TIG welding operations, companies should purchase their shielding gas from a reputable welding distributor and be certain that it meets the purity requirements for their application. All gas delivery systems should be free of contaminants that could enter the weld puddle and welding operators should use the correct shielding gas flow rate. Too little gas flow won’t properly shield the molten weld pool, while too much flow can cause turbulence and aspirate air into the weld puddle. Protecting the weld puddle from drafts is also critical. Due to the initial up-front cost savings, the temptation may be great for companies to purchase less expensive filler metals. However, doing so can often lead to greater long-term costs and lower productivity levels. It is not uncommon, for example, to experience downtime associated with poor wire feeding, excessive spatter or, potentially, weld defects when using lower quality filler metals. Companies may also find themselves experiencing an excessive amount of time for non-value-added activities (those that do not directly contribute to their throughput), such as applying anti-spatter and post-weld grinding or rework. For that reason, it is important to look at the total cost of using particular filler metals, as opposed to the per-unit cost. If more expensive, higher quality filler metals can minimize labor costs for non-value-added activities and provide better weld quality and/or greater productivity, then the higher up-front cost makes good sense in the long run. Skipping steps in weld preparation can lead to weld defects, rework or scrapped parts. Welding operators should always take care to clean the base material before welding to prevent contaminants like dirt, oil or grease from entering the weld puddle. Similarly, monitoring part fit-up is a critical part of the pre-weld process. Welding operators should carefully assess the weld joints to ensure there are no excessive gaps, as poor part fit-up can lead to issues like burn-through or distortion on all materials, but particularly when welding on materials like aluminum or stainless steel. Clamping or fixturing a part in the correct position is also a good practice to help protect materials like stainless steel against distortion or buckling. It is not uncommon for companies to overlook the importance of their MIG gun consumables. Unfortunately, that oversight can lead to a host of problems, including unscheduled downtime for changeover and/or rework of weld defects caused by a poorly performing contact tip, nozzle or liner. To help avoid problems, select consumables with a tapered design that locks conductive parts together to reduce heat buildup. Contact tips with coarse threads are a good way to speed up replacement and make sure installation is accurate. Look for consumables where the diffuser locks and aligns the liner with the contact tip and power pin for flawless wire feeding. These systems also offer error-proof liner installation with no measuring required; the liner is simply locked in and trimmed flush with the power pin at the back of the gun. As with other parts of the welding operation, investing time and money in training can yield significant long-term benefits for companies. Not only do welding operators benefit individually from process and equipment training, but in many cases it can also help them optimize the welding operation for greater efficiency. Too, proper training can give companies a competitive edge over those who have less-skilled labor and it promotes greater teamwork among employees. Typically, training opportunities are available through equipment and filler metal manufacturers or through welding distributors. In some cases, working with a local technical college can lead to training for specific applications and markets, allowing companies to bring in welding operators who are already trained for a given application and better promote their position in a given industry. Making mistakes is human nature, but with some careful consideration, it is easy to avoid some of the more common ones associated with running a welding operation. Measuring out long-term savings, versus cutting costs up front, is a particularly good way to avoid pitfalls that could lead to excessive downtime, quality issues or lost productivity. And it can have an excellent impact on a company’s bottom line.
When you have a company that fabricates its projects by the tons and measures its man-hours by the thousands, downtime simply isn’t an option. The welding operators and supervisors at Brooklyn Iron Works know that fact better than most. The Spokane, Wash.-based company, whose steel fabrication spans from bridges in Alaska to projects in Antarctica, tackles some of the highest-profile, high-inspection jobs around. And they rely on some good old-fashioned teamwork, among other attributes, to meet their deadlines. “Everything we do is a team effort,” QA Manager Phil Zammit explains. “We’re a good company with skilled employees and good management. It makes us a premium company here in the Northwest.” It also makes them a reputable one. Brooklyn Iron Works doesn’t maintain a sales force, but instead relies — and successfully so — on its reputation and word of mouth to generate business. Scott Allen, the company’s general manager, explains that they are invited to bids based simply on the quality work they do and the timeliness in which they do it. Last year, Norco Gas & Supplies representative Tim McGrath approached Zammit and Allen with a proposition to make their welding operations even better: a two-week trial of Bernard Centerfire™ consumables on their existing MIG guns. According to Zammit, they had tried Bernard products years before and didn’t think they were the right fit for their application. Still, he decided to keep an open mind and agreed to the trial. Two weeks later, he invited McGrath to convert the front-end of all 25 of the company’s MIG guns to Centerfire consumables and shortly thereafter, converted to Bernard’s Q-Gun™ MIG guns too. The reason? Less downtime. Brooklyn Iron Works, according to Allen, fabricates projects ranging from 650 to 2,000 tons or more, including fracture critical structural components for bridges, demand-critical welding on columns, beams and moment connections bound for seismic locations, like California. Not surprisingly, the company maintains a workforce of highly skilled certified welders certified to the AWS D1.1 (Structural Welding Code – Steel), D1.8 (Structural Welding Code – Seismic) and D1.5 (Bridge Welding Code). Many projects take between nine months and a year from start to finish. Depending on contract and/or code specifications, every weld at Brooklyn Iron Works is visually inspected and oftentimes includes 100 percent NDE (nondestructive examination) including MT, UT or RT. Others undergo random NDE testing for quality monitoring purposes. The company maintains a staff of certified welding inspectors (CWIs), as well as hosting contracted NDE inspectors, to manage these tasks. They also have a cleaning and painting facility to finish products after welding and prior to shipment to customers. Gaining access to the weld joints is one of the biggest challenges welding operators at Brooklyn Iron Works encounter while creating these welds. They weld mostly structural steel grades, with the majority being A36, A572 Grade 50, A500 and A709 steel including weathering types. Thicknesses range from 1/4 to 2-1/2 inches. On deep and tight joints, reaching the root of the joint for the initial root pass requires not only the right type of MIG gun and nozzle, but also welder dexterity. With the company’s previous consumables, welding operators often had to extend their electrode stickout as far as 2 inches to access the joints, a practice that risked generating porosity since it could compromise the necessary shielding gas coverage. Another challenge the company faced was the occurrence of burnbacks, the formation of a weld inside the contact tip, when using their old brand of contact tips. Brooklyn Iron Works welding personnel run their weld beads at high amperages (300 to 400 amps) using typically .052- or 1/16-inch FCAW wire diameters, which often proved too harsh on their previous contact tips. They would loosen after routine welding, causing the wires to arc back and create the burnback. The trial of Centerfire consumables gave Zammit and his team of welding operators a solution to these two problems—and it led to a MIG gun conversion that provided some additional benefits, too. When McGrath initiated the trial of Centerfire consumables at Brooklyn Iron Works, he started by installing them on just two MIG guns, using a conversion adapter offered by Bernard. Zammit and his welding operators quickly realized that the design of the Centerfire consumables provided a better solution for their welding operation. The Centerfire nozzles they trialed, and now use, feature a tapered design that stays fixed flush with the end of the contact tip and allows welding operators to reach into the deep weld joints without having to extend their welding wire as much. As a result, the welding operators can gain better gas coverage and lessen the risk of porosity. The Centerfire consumables also include a built-in spatter shield that acts as an additional gas diffuser and ensures a more consistent gas flow, a feature that Zammit particularly likes. “These consumables direct the gas exactly where we need it,” he explains. “It keeps our gas shielding coverage right at the weld, even when the doors are open or we have a breeze. We’ve never had a huge problem with porosity, but now we have even less of one.” Just as importantly, Zammit and his welding operators have almost completely resolved their issue with burnbacks. Compared to the company’s previous contact tips, which threaded into the diffuser and tended to loosen after welding, the Centerfire contact tips “drop in” the diffuser and are held in place by tightening the nozzle. This non-threaded tip design features a tapered base and large diameter seat that helps generate consistent electrical conductivity and heat transfer—and it stays in place during welding. We rarely get burnbacks anymore with the Bernard contact tips, before we had a substantial amount of downtime. And that’s money. It’s lost arc time for tip maintenance. On the few occasions when a burnback does occur, Zammit notes that the Centerfire contact tips can be easily removed— without tools— and changed because of the threadless design.He also goes on to explain that the company is saving money by having to replace fewer contact tips. By his calculation, Brooklyn Iron Works now uses about a third fewer contact tips than before. Shortly after converting their front-end consumables, Zammit and his welding operators also decided to convert to Bernard MIG guns. They now use 400-amp, air-cooled Q-Gun MIG guns with 15-foot cables and have, since the conversion, found additional ways to reduce downtime. According to Zammit and Maintenance Supervisor John Dahl, the maintenance on their Q-Gun MIG guns is much simpler than with the competitive guns they used previously. Changing the neck or liner on those guns required an Allen wrench to remove setscrews on the front and backend of the MIG guns, a process that Dahl says required disassembling the MIG gun and could take nearly an hour to complete. To change the necks on the Q-Gun MIG guns Dahl simply unscrews a plastic ring surrounding the neck by hand and inserts the new neck or liner. It takes less than five minutes. And he finds that he doesn’t have to conduct maintenance as often, either. In fact, he said that one of the Q-Gun MIG guns has been used with the same liner for a year. “Maintenance on these guns is so much easier and quicker now,” says Dahl. “Plus, we’ve gotten good feedback from the welding operators in terms of the neck options on the Q-Guns.” The Q-Gun MIG guns have necks available in fixed, rotatable and flexible options in various lengths and bend angles, with the rotatable versions being able to changeover without tools. According to Zammit, these neck options help the welding operators better accommodate the varying welding angles they encounter on projects. They can reach the weld joints easier and reduce downtime to address issues like wrist fatigue. Welding operator Ricky Curtis agrees — especially when it comes to using the flexible neck versions of the Q-Gun MIG guns “I can bend the neck in any direction I need,” he explains. “Even around the corners. I like that the gun does the work for me, instead of my wrist.” Zammit and Allen also like that the welding operators are more comfortable and that it is taking less time to maintain the guns. Simply put, more arc-on time means better productivity. Keeping an open mind isn’t always easy. It’s often human nature to stay with the routine of “doing things as they’ve always been done.” But sometimes, taking a chance can yield unexpected benefits. Brooklyn Iron Works clearly learned this lesson when they agreed to the trial of Bernard consumables. Now they are reaping the positive results that come with it, and passing those results on to their customers. From the power source to the welding wire, each of the components in an arc welding operation can have a significant impact on productivity. The welding gun and consumables — nozzles, contact tips and diffusers — in particular, are often an overlooked aspect of the whole process, but these components directly affect quality, welder comfort, rework, downtime and more. There are three key ways in which guns and consumables used in flux cored arc welding (FCAW) and gas metal arc welding (GMAW) can lead to improved productivity: The contact tip is the last point of contact between the welding equipment and the welding wire, as well as the consumable responsible for generating the electrical connection to create the arc. As the wire passes through the contact tip, it can often erode the inside of the tip bore, leading to interruptions in the electrical current and causing poor arc stability. During the normal course of welding, especially at higher amperages, the contact tip can also become loose and cause a burnback (or the formation of a weld inside the contact tip). Burnbacks are often a significant source of downtime in a welding operation — and a big hindrance to productivity. Having a contact tip that stays securely placed during the course of welding is key to combating burnbacks. Brooklyn Iron Works (Spokane, Wash.) found just such a solution when they converted to Centerfire™ contact tips last year. Like other structural fabrication companies, Brooklyn Iron Works faces stringent deadlines for its projects, so the ability to minimize downtime for burnbacks and any other equipment management is imperative. Their welding personnel run their weld beads at high amperages (300 to 400 amps) using typically .052- or 1/16-inch FCAW wire diameters, which often proved too harsh on their previous contact tips. They would loosen after routine welding, causing the wires to arc back and create the burnback. “Before we converted to the new contact tips, we had a substantial amount of downtime for contact tip changeover,” explains QA Manager, Phil Zammit. “And that’s money. It’s lost arc time for tip maintenance. Now we are using a third fewer tips and don’t have to worry about the downtime like before.” The company’s new contact tips don’t loosen because they “drop in” the diffuser and are locked in place by tightening the nozzle. They also feature a non-threaded tip design with a tapered base and large diameter seat. The other benefit of the design is that it helps generate consistent electrical conductivity and heat transfer, both of which help the consumables last longer and perform more reliably. Brooklyn Iron Works’ welding operators frequently encounter weld joints up to 2-in. deep. In the past, they often had to extend their electrode stickout as far as 2 inches to access the joints, a practice that risked generating porosity since it could compromise the necessary shielding gas coverage. Brooklyn Iron Works has found their solution to porosity is to have the right size and shape of nozzle for the application. Switching to Centerfire consumables now allows them to reduce electrode stick-out and gain better gas coverage at the same time. “These consumables direct the gas exactly where we need it,” Zammit explains. “It keeps our gas shielding coverage right at the weld, even when the doors are open or we have a breeze. We’ve never had a huge problem with porosity, but now we have even less of one.” The nozzles feature a tapered shape that stays fixed flush with the contact tip. They also include a built-in spatter shield that acts as an additional gas diffuser and ensures a more consistent directional gas flow, even on deep joints or if there is a slight breeze present. The typical welding operator spends time during a shift allocated to joint preparation, part fit-up and movement, along with other activities that contribute to the throughput of the welding operation. But during the actual process of welding, it is critical that he or she remain comfortable. Good welding operator comfort lessens the chances of injuries associated with repetitive movement and reduces overall operator fatigue. And a more content employee also brings forth the potential for greater productivity. Welding operators at Brooklyn Iron Works have addressed the issue of comfort through the various necks available on their Bernard 400-amp Q-Guns. The Q-Guns are available with fixed, rotatable and flexible necks in various lengths and bend angles. These neck options help the welding operators better accommodate the varying welding angles they encounter on projects. They can reach the weld joints better and minimize downtime to address issues like wrist fatigue. The flexible necks are especially helpful on difficult joints, as they can be adjusted to weld around corners or to fit into complex shaped steel components. Welding operator Ricky Curtis explains, “I can bend the neck in any direction I need. Even around the corners. I like that the gun does the work for me, instead of my wrist.” According to the company’s maintenance supervisor, John Dahl, there have been additional benefits to the design of the gun as well. “It takes only about five minutes to change a neck on these guns, compared to nearly an hour with our previous guns,” he explains. This ease of maintenance is another way in which having the equipment has helped Brooklyn Iron Works reduce downtime and get back to welding faster. Remember, in the long run, companies can benefit from looking at how every aspect of their welding operation impacts downtime. Time spent for changing out contact tips or maneuvering unnecessarily into difficult joints can ultimately hinder productivity, as can having welding guns that are time-consuming to maintain. Addressing the problem of productivity may be as simple as looking at a new consumable option or finding ways to make the welding operators more comfortable.
Consumables for the welding gun can significantly impact the productivity and welding quality in an operation. This makes it important to keep consumables properly cleaned and maintained, to help minimize unplanned downtime, extend consumable life and optimize performance. The heat produced in the welding process can have a significant impact on the cleanliness and longevity of MIG consumables. Processes like pulsed MIG and/or higher amperage applications tend to subject consumables to higher levels of heat, as do applications in which there is a large amount of reflective heat. Those include applications with tight tooling or those that require welding in restricted areas. The hotter the consumables become during the welding process, the softer the material (usually copper or brass) becomes, resulting in a surface area that is much more prone to accumulating spatter and failing prematurely. To avoid such problems, it is important to determine the best consumables for each application and consider how they will be managed throughout the course of a welding shift. For example, high-amperage applications (those above 300 amps) most often benefit from using heavy-duty consumables because they have greater mass and are capable of dissipating the heat more readily. However, if the welding procedure dictates that the contact tip must be changed frequently, a standard-duty contact tip may suffice. The goal is for companies to determine which consumables — heavy- or standard-duty — are most capable of withstanding the duty cycle and heat of the application. A reliable welding integrator can often help with the selection. Using an anti-spatter compound can help keep MIG consumables clean on both semi-automatic and robotic welding applications; however, it must be used sparingly. On a semi-automatic application, welding operators should dip only the front inch and a half of the nozzle into the anti-spatter compound. Submerging the nozzle in the anti-spatter compound can saturate the nozzle’s fiberglass insulator and also potentially plug up the gas holes on the diffuser. This build-up may cause the nozzle to fail prematurely or result in porosity in the welds due to the unbalanced gas coverage. In robotic applications, only the minimum amount of anti-spatter compound required for the application should be used. Using too much can cause build-up on the consumables and/or cause debris to accumulate and clog the nozzle, leading to poor gas coverage, inconsistent electrical conductivity or shortened consumable life. Another important way to combat spatter is to inspect the nozzle for build-up on a regular basis and clean it with a soft wire brush or spatter-cleaning tool as needed. Welding operators should never hit the nozzle against the tooling or work piece to loosen spatter. Doing so can dent, misshape or compromise the smooth surface finish of the nozzle, which creates greater areas for spatter to adhere to and reduces the life of the consumable. Always keep MIG consumables in their original packaging until they are ready for use. Opening them and placing them in a bin can lead to scratches or dents that allow spatter to adhere and will ultimately shorten the products’ life. Similarly, removing contact tips or diffusers from their packaging and storing them in open or dirty containers can cause dirt and oil to accumulate in the threads, which can impede them from properly seating together. Also, companies should always keep storage containers for new consumables separate from those for discarded ones to avoid selecting an old contact tip or nozzle that may have dents or scratches and be prone to spatter accumulation. Finally, welding operators should always use clean gloves when handling or replacing contact tips, nozzles and diffusers to prevent dirt, oil or other contaminants from adhering to them. Installing MIG consumables correctly and inspecting them periodically for good connections minimizes the chance of poor conductivity and with it, spatter accumulation or premature failure. Welding operators should always follow the GMAW consumable manufacturer’s suggestions for contact tip and gas diffuser installation, using a pair of channel lock pliers, welpers or other such recommended installation tool. Never use wire cutters or side cutters — too much pressure from these tools can damage the inside diameter of the contact tip, which leads to poor welding performance and a shortened lifespan. Also these tools tend to scratch the surface of the consumables leaving marks that attract spatter. A good rule of thumb is to hand tighten the contact tip until it is fully seated into the diffuser, then grip the contact tip with an appropriate tool as close to the base as possible, tightening it 1/4 to 1/2 turn past finger tight. This procedure helps ensure a good connection that minimizes electrical resistance, overheating and damage to the consumables, as well as excessive spatter accumulation. Follow the same procedure for installing and tightening the diffuser so that it fully connects with the neck. Also note, some contact tips available in the marketplace can be installed and held in place by hand tightening the nozzle. Check the manufacturer’s recommendation for proper installation instructions. Inspect consumable connections regularly to ensure that they are secure. An improperly trimmed and installed liner can cause a host of wire-feeding problems that lead to downtime to rectify. It can also affect the performance of MIG consumables, how clean they stay and their longevity. Cutting a liner too short can cause the liner to be misaligned with or in the gas diffuser. The result is a welding wire that feeds off-center, leading to premature contact tip failure. Liners that are too short can also lead to the build-up of debris between the liner and retaining head, which causes wire feeding issues and poor weld quality. In some cases, the gap that is present between the gas diffuser and liner when a liner has been cut too short may cause the welding wire to catch, resulting in small shavings that can plug up the contact tip and cause it to fail quickly. A liner that’s too long can cause kinking that again leads to wire-feeding issues that shorten the life of the contact tip. Always make sure that to remove any burrs or sharp edges after cutting a liner to ensure smooth and consistent feeding of the welding wire. Welding operators should always consult with the liner manufacturer’s recommendation for proper trimming and installation instructions. It is also important that they wear gloves when handling the liner and avoid dragging it on the ground to prevent debris from being introduced into the MIG gun. Such debris can lead to weld contamination and/or poor consumable performance. The position of the contact tip (extended or recessed) affects how well consumables last, along with how clean they stay. So too does the nozzle used in conjunction with a specific contact tip and the wire size. The farther the contact tip extends from the nozzle, the closer it is to the arc and the more prone it is to reflective heat. The result is a greater tendency toward spatter accumulation and a greater opportunity for burnbacks. Using a recessed contact-tip-to-nozzle relationship when possible can minimize this problem and provide better shielding gas coverage at the same time. For companies with applications that require access into restricted areas, it is important to select a nozzle that provides that access, but isn’t tapered so much that it minimizes the space around the contact tip. If there isn’t enough space for shielding gas to flow out of the nozzle, it can cause the shielding gas to hit the work piece and begin jetting back and/or swirling. The result is the pulling of oxygen into the weld pool and an increase in spatter. Too, the smaller the bore size on the nozzle, the more prone it is to absorbing heat (because there is less mass to that portion of the consumable) and having spatter adhere to it. As a general rule, companies should select the largest consumable that will work for the application and provide the necessary joint access. Larger consumables are more able to resist heat and spatter build-up, and they often last longer as a result. Selecting consumables with the right material for the application is important, too. For example, brass nozzles tend to resist spatter well and are good for lower-amperage applications (100 to 300 amps), whereas copper nozzles are better for high-amperage applications (above 300 amps) or for those with longer arc-on time. Lastly, companies should always pay attention to the manner in which they manage consumables. When possible, having the same consumables throughout the welding operation can help welding operators better maintain the consistency of the consumable performance and troubleshoot problems more quickly when they occur. The result can be longer-lasting, cleaner consumables that provide more reliable performance and quality.
Gas metal arc welding (GMAW) involves more than just arc-on time. Welding operators also need to be mindful of other activities that contribute to the overall productivity and quality in the welding operation, including proper joint preparation, following correct weld parameters and ensuring good part fit-up. Selecting the proper GMAW gun, consumables and shielding gas is also critical to achieving good results. Unfortunately, it is not uncommon for there to be confusion as to how these components affect the welding operation. The reality is, however, that they can have a significant impact on downtime and costs, not to mention operator comfort. The goal is to make sure that impact is positive. Following are answers to some common questions about GMAW guns, consumables and shielding gas to help you select the best ones for your welding operation and manage them in a way that provides optimal results. When it comes to GMAW guns, bigger isn’t always better. In fact, selecting a larger amperage gun than needed for your application may cost you money in the long run and lead to discomfort, which results in unnecessary downtime. Duty cycle is defined as the amount of arc-on time within a 10-minute period, so a 20 percent duty cycle would constitute two minutes of arc-on time in a 10-minute time frame. Because most welding operators don’t weld 100 percent of the time, it is often possible to use a lower amperage gun for a welding procedure that calls for a higher amperage one. For example, in many cases you could use a 300-amp gun model in place of a 400-amp gun model, since actual arc-on time often does not exceed the amperage to duty cycle ratio of a 300-amp gun. The benefit is that the lower amperage gun generally costs less money — and it also weighs less, which can help reduce wrist fatigue, commonly associated with downtime. The lower amperage GMAW gun will still be capable of operating at the appropriate capacity, while also offering the benefit of being easier to maneuver – a factor than may help you improve weld quality and lessen rework, too. There are several factors to consider when choosing your GMAW gun. After determining your amperage needs, you should also look for features like a rigid, strong strain relief. Strength in this area between the power pin and cable can help minimize kinking, which often leads to an unstable arc and/or poor wire feeding. Next, consider selecting a smaller handle gun (but one that can still meet your amperage needs), as it may help reduce wrist fatigue and be easier to maneuver into complex joints. You may also want to consider looking for a specific style of neck for your application. Many GMAW gun manufacturers offer fixed, rotating and flexible necks in various lengths and angles, allowing you to reach joints more easily. Regardless of the style of neck you choose, you should find one with good armor to protect it against damage that could lead to electrical shorts or premature failure. Finally, select a GMAW gun with a comfortable and easy-to-service trigger. Typically, you will be able to find a variety of trigger options, including standard style, locking or dual schedule. Regardless of the specific style, look for sturdy triggers that will withstand work site abuse and that can be easily replaced should one of the mechanics fail. Shielding gas prevents exposure of the molten weld pool to oxygen, nitrogen and hydrogen contained in the air atmosphere, in order to protect the weld from contamination and/or defects. The type you use can impact everything from the penetration profile to arc stability and the mechanical properties of the finished weld. If you need deep weld penetration, particularly on thick materials, carbon dioxide (CO2) is a good choice and it is also the least expensive. This gas, however, does tend to create spatter and is limited to use in short circuit welding. Adding 75 to 95 percent argon to the CO2 can provide better arc stability and puddle control, both of which reduce spatter compared to straight CO2. This mixture will also allow you to use a spray transfer process, allowing you to weld faster in many cases. Argon also produces a narrower penetration profile that is useful for fillet and butt welds. If you’re welding a non-ferrous metal — aluminum, magnesium or titanium — you’ll need to use 100 percent argon. In some cases, oxygen or helium is used in the GMAW process, but it is not as common. Consumable service life can vary dramatically from application to application. There are a few steps you can take to make them last longer, however. First, use the correct contact tip for the size wire who have and be certain it fits securely with the gas diffuser. A solid connection between these components helps ensure good conductivity and minimize overheating, making them last longer. Also, inspect your nozzle on a regular basis for spatter and clean as necessary. Use a pair of welding pliers or a special nozzle-cleaning tool for the job, as directed by the consumable manufacturer. Be sure, too, that you have the appropriate type of consumables for your application. Applications above 300 amps, for instance, can often benefit from heavy-duty consumables, which have greater mass and can dissipate heat more readily. The result, in many cases, is longer service life. Finally, set the drive roll tension on your wire feeder so that the wire feeds properly. Doing so prevents deformities in the wire (in the case of too high of tension) that may cause the wire to wear out the contact tip prematurely. Cutting a GMAW liner too long can cause it to become misaligned with the gas diffuser. Conversely, cutting a liner too short may lead to debris build-up between the liner and gas diffuser. Both instances can lead to poor wire feeding, weld quality issues and premature contact tip failure. To prevent this problem, always follow the manufacturer’s instructions for installation, making certain that the liner is free of any burrs or short edges after you trim it. A smooth cut helps ensure smooth and consistent feeding of the welding wire. Some manufacturers offer a liner gauge to help you determine the proper length for your particular liner, while others print markings on the outside of the weld cable to show when the liner is twisted, allowing for more accurate trimming. If your gun does not have these markings, make sure the cable is fully extended when inserting the new liner. Remember to wear gloves when handling the liner and avoid dragging it on the ground. These precautions help prevent debris from being introduced into the GMAW gun and causing weld contamination and/or poor consumable performance. Burnback is one of the most common causes of downtime in a GMAW application and is a significant cause of premature contact tip failure. Proper equipment setup is one of the key defenses to protect your consumables. First, be sure that you have established the appropriate contact tip recess and wire stick out for your application, and that you maintain a correct contact-tip-to-work distance. Check electrical connections regularly and replace worn work leads or cables, as faulty ones can also cause the problem. Make sure to maintain the proper drive roll tension and install your liner properly, too. Both precautions minimize erratic wire feeding that could lead to burnbacks. Storing and handling GMAW consumables properly not only helps them last longer, but also perform better. Never store your GMAW consumables loose in a bin, since it can cause scratches on them that attract spatter and may lead to premature failure. Instead, keep them in their original packaging until you are ready to use them. Doing so will also protect the components from contaminants such as dirt or oil. Finally, always wear clean gloves when handling or replacing contact tips, nozzles and diffusers. Again, it helps prevent dirt, oil or other contaminants from adhering to them and also potentially entering the weld puddle. Like any welding process, GMAW has many factors to consider in order to achieve the best results. Make sure that you don’t overlook the impact of your GMAW gun, consumables and shielding gas as part of those. Being mindful of the selection process, storage and handling, and installation, among other things, can be beneficial to both your productivity and your bottom line in the long run.
It’s tough to stay cool in the hot summer months, let alone when you are “under the hood” welding. Unfortunately, that heat can take a toll on your body, mind and performance. In addition to affecting your mental acuity – causing loss of concentration or, in extreme cases, confusion – excessive heat can also affect your motor skills, cause irritability and increase fatigue. Consuming liquids throughout the day is a critical part of staying cool. It is also helpful to supplement that approach with smart equipment selection and other cooling options. Consider these tips. As a general rule, selecting the lightest, most flexible MIG gun for the application is the best choice. In the case of a 400-amp application, a MIG gun rated at 300 amps may suffice for your application. That is because MIG gun amperages reflect the temperatures above which the handle or the cable on a MIG gun becomes uncomfortable. They do not indicate the point at which the MIG gun risks damage or failure. Also, you spend time in the day doing other things besides welding – moving parts, prepping materials or fixturing them. It’s highly unlikely that you will be operating the MIG gun at full amperage and full duty cycle at all times. Duty cycle is defined by the amount of arc-on time in a 10-minute period that the equipment can be operated at maximum capacity. Some MIG guns will offer 100 percent duty cycle, while others are rated 60 percent or below. It is important to research the MIG gun’s duty cycle prior to purchasing it in order to ensure it offers the necessary capacity for the application. But in most cases you don’t have to match your MIG gun amperage to the exact amperage of your application to get the job done. A lower amperage MIG gun can often suffice and keep you cooler. Selecting a MIG gun with the appropriate handle, neck and cables for your application can also help you stay cool. Typically, as a MIG gun’s amperage decreases so too does the size of the gun handle and the cable. That decrease in size and weight can help minimize the amount of energy you exert and reduce heat stress. Decide what type of MIG gun handle is most comfortable for you. MIG gun manufacturers often offer handles in curved and straight models. Regardless of the one you choose, make sure it is a lightweight, comfortable style that also meets the MIG gun and application’s amperage and duty cycle requirements. Typically, a smaller handle will be easier for you to maneuver. Additionally, some MIG gun manufacturers offer ventilated handles, which help reduce heat and are more comfortable to hold when welding for longer periods of time. In some instances, a water-cooled MIG gun may provide the smaller size desired for an application and would be a good choice to reduce fatigue on higher amperage applications, especially in a shop setting. When selecting power cables, choose the smallest and shortest power cable possible that can still meet the needs of your application. Smaller and shorter power cables are lighter and more flexible, and can help reduce your fatigue. They can also minimize clutter in the workspace and prevent excessive coiling that may be cumbersome to unravel or that could lead to poor wire feeding. An added advantage is that smaller and shorter cables tend to be less expensive, as well. Also, consider using a MIG gun with a rotatable or flexible neck to minimize unnecessary movement. Flexible necks can be easily adjusted to fit different welding angles. This feature helps minimize additional straining to reach a particular weld joint, and reduces the risk of fatigue or injury. Similarly, rotatable necks are a good option for welding out-of-position (including overhead), as they can be adjusted to reach the weld joint without changing the gun handle or its position. Bernard offers neck couplers, too, which allow you to connect multiple necks together to reach especially difficult joints more comfortably. Cooling vests are one option for beating the summer heat, but these can make some people uncomfortable and actually increase fatigue. Instead, you may want to consider a lighter cooling option like a cooling belt. For example, the CoolBelt™ from Miller Electric Mfg. LLC (an Illinois Tool Works company that Bernard is a division of) provides constant airflow over the welder’s head and face. The fan on the CoolBelt is secured on the lower back. Air flows upward through a piece of tubing that fits into your helmet; it’s then dispersed through the vents. The CoolBelt can reduce the temperature as much as 17 degrees. One advantage of the CoolBelt, compared to a cooling vest is its weight — it is significantly lighter so it helps improve stamina throughout the workday. Additionally, the CoolBelt doesn’t obstruct your range of motion, allowing you to perform more efficiently. Find Additional Safety Gear to Meet Your Personal Protection Needs
For companies faced with training new welders, it is important to instill good habits early in the process. Doing so helps ensure the welders are well prepared not only to create quality welds, but also to contribute positively to the operation’s productivity. It can also help the welders gain the confidence they need to become increasingly proficient. Following are 10 important things to teach new welders, to help them improve their skills and stay safe in the process. 1. Make safety a priority: It is critical that welders protect themselves from the heat and electricity generated by the welding process with the proper personal protective equipment (PPE). The arc is dangerous to both the eyes and skin. PPE includes: flame-resistant gloves, safety glasses, a welding helmet and a long-sleeved welding jacket. Flame-resistant clothing and steel-toed shoes are also recommended. Both the American Welding Society (AWS) and OSHA offer guidelines for PPE for specific environments. Be sure to use enough ventilation, local exhaust at the arc, or both to keep the fumes and gases below the Permissible Exposure Limit (PEL)/Threshold Limit Value (TLV)/Occupational Exposure Limits (OELs) in the breathing zone and the general area. Always train new welders to keep their heads out of the fumes. Explain the importance of reading and understanding the manufacturer’s instructions for equipment, your company’s safety practices, and the safety instructions on the label and the material safety data sheet for the filler metals being used. Routinely check for proper ground connections and stand on a dry rubber mat (indoors) or a dry board (outdoors) during welding to minimize the possibility of electrical shock 2. Install consumables properly: Good conductivity (the ability for the electrical current to flow along the welding circuit) helps gain good weld quality. New welders should always install their consumables – diffusers, nozzles, contact tips – according to the manufacturer’s recommendation, making sure that each component is securely tightened. In a gas metal arc welding (GMAW) operation, for example, the connection between the GMAW gun neck and diffuser needs to be secure to prevent shielding gas leaks. Secure connections also provide the surface area necessary to carry the electrical current throughout the GMAW gun to create a stable arc. Good connections also help prevent weld defects, support consistent productivity and reduce the risk of premature consumable failure due to overheating. 3. Cleanliness is critical: Dirt, oil, grease and other debris can easily enter the weld pool causing contamination that leads to poor weld quality and costly rework. Excessive oxidation and moisture can compromise quality weld. New welders need to learn proper cleaning procedure for the base material they are welding. In some cases, wiping the base material with a clean, dry cloth may suffice. However, welding on aluminum, for example, requires the use of a stainless steel wire brush designated for aluminum to clean out the joint before welding. A wire brush removes dirt and any of the oxides that may still reside on material surface. Regardless of the material, it is important to follow the proper instructions for cleaning before welding. 4. Always follow welding procedures: Welding procedures are the “recipe” needed to create consistent welds and should be followed at all times. The procedures for a given application have been carefully determined and qualified by experts to ensure that the recommended parameters are capable of yielding the desired results. Weld procedures include the required shielding gas mixture, recommended gas flow rate, and voltage and amperage ranges. These procedures also provide information on the type and diameter of filler metal to use, as well as the proper wire feed speed in the case of a GMAW or flux-cored arc welding (FCAW) application. 5. Understand the importance of filler metals:New welders can benefit from familiarizing themselves with the attributes of various types of wires, including flux-cored and metal-cored wires, as well as the techniques for welding with each type. For example, they should learn whether their filler metal requires a “push” or “pull” technique. Following old adages like, “If there’s slag, then you drag,” can help; it indicates that flux-cored wires, which produce slag, should be operated using a pull technique. New welders should also become familiar with the manufacturer’s specification sheet for additional operating recommendations. Learning to handle and store filler metals properly is also critical for new welders to learn. They should always wear clean gloves when handling filler metals and if they are responsible for storing them, should do so in a clean, dry environment. 6. Stay comfortable: Keeping cool and comfortable during the welding process can help welders lessen the chance of injuries associated with repetitive movement and reduce overall fatigue. When possible, new welders should learn to minimize cumulative strength moves, material handling or constant motion. They should also use a GMAW gun with a comfortable handle and cable style, as these factors contribute to the equipment’s maneuverability. New welders should be encouraged to play an active role in improving workspace ergonomics. Typically, the more input a welder offers about the job, the more satisfied he or she will be. Plus, that involvement can help ensure greater safety compliance and lower workers’ compensation costs for injuries. 7. Know the material properties: Every material has different mechanical and chemical properties. Helping new welders understand the difference between materials — particularly how they react to heating and cooling — is a key component of training. For example, austenitic stainless steel conducts heat at around half the rate of mild steel, but has a much higher rate of thermal expansion when welded; it also has a more localized heat affected zone (HAZ) that can lead to buckling when the weld cools. Welders who are aware of such properties can take precautions such as clamping to prevent distortion. Similarly, many materials require pre- and post-weld heat treatments to control the cooling rate and prevent cracking. When welders are familiar with such material attributes, they’re better prepared to make necessary adjustments during the welding process. 8. Visually inspect the welds:Knowing how to conduct an accurate visual inspection of a completed weld is the first step in quality control. It is also the quickest and least expensive method of inspection. New welders should learn how to identify weld defects that have porosity, for example, since the presence of this weld defect on the surface often indicates a similar problem throughout the weld. Identifying the defect early on helps prevent the time and cost associated with other testing methods, including x-ray or NDT (non-destructive testing) inspections. Other defects that new welders should learn to identify include lack of penetration (high, ropey welds), excessive penetration (sunken welds) and undercutting (characterized by a notch in the base material). It is important that welders inspect for weld cracks, which are among the most common weld defects to occur. 9. Learn how to troubleshoot: Identifying and rectifying welding problems quickly is a key skill for new welders to learn. Good troubleshooting skills not only help reduce downtime, but they also contribute to good weld quality and productivity. Such skills can also help reduce costs associated with rework. New welders can benefit from learning how to adjust gas flow rates properly and/or identify gas leaks in order to solve instances of porosity. They should also know how to make adjustments to amperage and voltage settings if they encounter issues such as lack of penetration, excessive penetration or undercutting. Identifying welding problems associated with worn consumables is also important, since poor conductivity can result in an unstable arc and lead to a variety of weld defects. 10. Maintenance makes a difference: From the power source to the GMAW gun and consumables, every part of the welding system requires maintenance to keep it operating efficiently and effectively. New welders should become familiar with proper maintenance procedures — preferably preventive ones — as part of the ongoing upkeep of the entire welding system. Regularly checking that the connections throughout the length of their gun or torch are tight is important, as is visually inspecting the front-end consumables for signs of wear. In the case of a GMAW gun, the welder should replace nozzles or contact tips that have spatter buildup on them to prevent issues such as poor gas coverage or an erratic arc that will likely lead to weld defects. Welders should regularly check the power source, primary power line, gas cylinders and gas distribution system to ensure that they are working properly. They also need to replace faulty gas regulators or cables and hoses that show signs of wear, cracks or damage.MIG Welding Shielding Gas Basics
MIG Welding Shielding Gas Basics
Choosing The Right Shielding Gas
of the weld bead, can be caused by inadequate shielding gas and can dramatically weaken
the weld. Carbon Dioxide (CO2)
Argon
Oxygen
Helium
in shielding gas coverage. The photo on the left shows good coverage, while the coverage in the photo on the right allows
the air environment contaminate the shielding gas.Getting the Shielding Gas to the Weld Pool
contact tip is seated in the diffuser and held in place
by the spatter guard inside the nozzle.Don’t Let Consumables Consume Your Profits
Don’t Let Consumables Consume Your Profits: Choose, Use and Troubleshoot Wisely
Choose Wisely
Use Wisely
Troubleshoot Wisely
Contractor increases productivity…
Jolson Welding Improves Productivity with New MIG, FCAW Equipment
Making the Change
The result of the testing
The New Approach to Self-Shielded Welding
Gaining the Most Out of Gas-Shielded Welding
Tips For Avoiding Common Flux-Cored Problems & Improving Your FCAW Welds
Tips For Avoiding Common Flux-Cored Problems & Improving Your FCAW Welds
Tip One: Avoid Wire Feeding Problems
Tip Two: Stop Porosity and Worm Tracking
Tip Three: Eliminate Slag Inclusions
Tip Four: Prevent Undercutting and Lack of Fusion
Tip Five: Avoid Excessive Penetration or Lack of Penetration
Final Tips
Related Articles
Finding a MIG Gun That Fits
Finding a MIG Gun That Fits: Stay Cool and Comfortable While Welding
Selecting the Right Amperage
Getting a Handle On the Selection
Staying Cool
Putting It All Together
Choosing Wisely Simple Ways to Save Money and Reduce Downtime
Choosing Wisely: Simple Ways to Save Money and Reduce Downtime by Selecting the Right MIG Gun Consumables
Line Up for the Best Performance
Tips for Making the Right Contact
Know Your Nozzles
Your FAQs About FCAW…
Your FAQs About FCAW-SS Problems Answered
What are slag inclusions and how can I prevent them?
How can I prevent burnbacks?
Why does lack of fusion occur?
What are the causes of and solutions for bird-nesting?
What can I do to ensure I get the best joint penetration?
What can I do to prevent porosity?
More FAQs?
Maintaining Your MIG Gun… and Your Welding Costs
Maintaining Your MIG Gun… and Your Welding Costs
We all have the tendency to fall victim to the “bigger is better” philosophy. When it comes to purchasing a MIG gun, however, that thinking may cost you more money than is necessary for this equipment. It can also lead to costly downtime.
Regularly inspecting your MIG gun can be an important part of reducing costs and gaining good welding performance. Fortunately, preventive maintenance (PM) for a MIG gun doesn’t have to be time consuming or difficult. Consider these key factors.
missing screws. Check that your MIG gun trigger is not sticking or otherwise malfunctioning. Replace these components as necessary.
The Causes of GMAW Flaws
The Causes of GMAW Flaws … and the Cures to Help Welding Operators Get Back to Work Faster
Porosity
or the GMAW gun are free of leaks can help solve the problem.Burn Through
Incomplete Joint Penetration (Lack of Penetration)
Undercutting
Hot Cracking
Incomplete Fusion
When the weld metal fails to completely fuse with the base metal or with the preceding weld bead in multi-pass applications, incomplete fusion can occur. Some people also refer to this weld flaw as cold lap or lack of fusion.10 Mistakes in Running a Welding Operation and How to Fix Them
10 Mistakes in Running a Welding Operation and How to Fix Them
Mistake No. 1: Improper Filler Metal Storage and Handling
Mistake No. 2: Repurposing Old Equipment
Mistake No. 3: Using the Wrong Size MIG Gun
Mistake No. 4: Improper Preheat or Interpass Temperature Control
weld procedure altogether. Yet preheating is one of the biggest deterrents against cracking, as it slows down the cooling rate after welding. The type and thickness of the material being welded will determine preheat and interpass temperature. These requirements can be found in the application’s welding procedure, welding codes or other fabrication documents. For the best results, welding operators need to preheat the material completely through and extend the heated area to approximately three inches on either side of the weld joint. Welding should commence while the material is at or above the preheat temperature. Allowing the weldment to cool below the required interpass temperature may also lead to cracking.Mistake No. 5: Ignoring Preventive Maintenance
Mistake No. 6: Shielding Gas Inconsistencies
Mistake No. 7: Purchasing Filler Metals Based on Cost Only
Mistake No. 8: Improper Weld Preparation
Mistake No. 9: Disregarding MIG Gun Consumables
Mistake No. 10: Overlooking Training Opportunities
Keeping an Open Mind and Reaping the Benefits
Keeping an Open Mind and Reaping the Benefits: How One Company Reduced its Downtime and Costs Through a Simple Product Trial
The Projects and Challenges
The First Solution
Finding Additional Benefits with New MIG Guns
Reaping the Benefits
Three Ways Welding Guns and Consumables Can Improve Productivity
Three Ways Welding Guns and Consumables Can Improve Productivity
Contact Tips
Better Shielding
In addition to inadequate shielding gas, porosity can also occur if a welding operator uses too small of a nozzle for the application, extends the welding wire too far beyond the end of the nozzle or tries to weld with a nozzle full of spatter. Air from outside or from fans can create the problem, too, by blowing away much needed shielding gas.The Benefits of Comfort
MIG Gun Consumables: Tips to Extend Life
MIG Gun Consumables: Tips to Extend Life
The Heat Factor
The Anti-Spatter Solution
Proper Storage and Handling
Establish and Maintain Good Connections
Trim Liners Correctly
Recess/Extension Amperage Wire Stick-Out Process Notes 1/4-in. Recess > 200 1/2 – 3/4in. Spray, high-current pulse Metal-cored wired, spray transfer, argon-rich mixed gas 1/8-in. Recess > 200 1/2 – 3/4in. Spray, high-current pulse Metal-cored wired, spray transfer, argon-rich mixed gas Flush < 200 1/4 – 1/2in. Short-current, low-current pulse Low argon concentrations or 100 percent CO2 1/8-in. Extension < 200 1/4 in. Short-current, low-current pulse Difficult-to-access joints Mind the Contact Tip Position and Nozzle Size
Other Considerations
GMAW Guns, Consumables and More – Common Questions Answered
GMAW Guns, Consumables and More: Common Questions Answered
How do I determine what amperage GMAW gun I need
Besides amperage, what else should I consider when selecting a GMAW gun?
What type of shielding gas is best for my application?
How can I make my GMAW consumables last longer?
What is the proper way to trim and install my GMAW gun liner?
How can I protect my contact tips from burnback?
What’s the best way to store and handle my GMAW consumables?
Stay Cool When Welding In The Summer Heat
Stay Cool When Welding In The Summer Heat
Tip One: Don’t go over amperage
Tip Two: Get a good handle
Tip Three: Stay light and flexible
Tip Four: Consider a cool option
Teaching New Welders to Improve Quality and Productivity
Teaching New Welders to Improve Quality and Productivity