How Can Customizing a MIG Gun Benefit the Welding Operation?
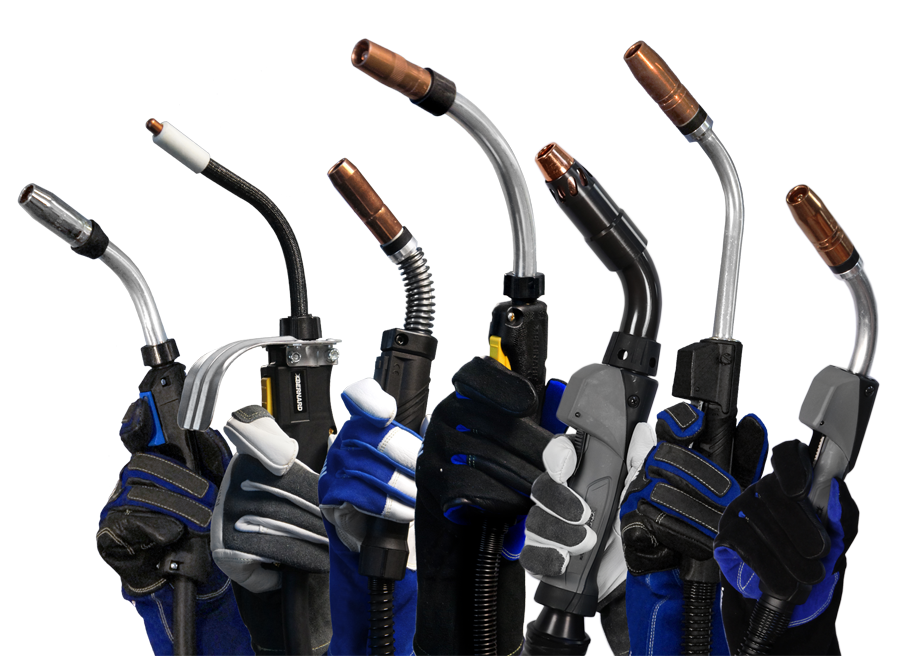
When choosing the right MIG gun for a semi-automatic welding application, there are many factors to consider — from the material being welded and the filler metal type to the weld cell layout and expected arc-on time.
Customizing a MIG gun for the specific needs of the application, in addition to choosing the proper consumables, can pay off in greater productivity, better comfort and improved quality in the completed welds.
There are easy-to-use tools, such as online configurators, available to help users customize a MIG gun. In addition, keep some key factors in mind to help configure a gun that best suits the application needs.
Why customize?
Customizing a MIG gun offers numerous benefits compared to using a standard gun out of the box. Customization can maximize efficiency and productivity in a welding operation, and provide greater comfort — which can improve safety and offer longer arc-on time. Essentially, customization ensures that the welding operator has the exact MIG gun for the application.
Also, some standard MIG guns may require extra time for assembly right out of the box or require extra components be added before welding can begin. This is not the case with customized MIG guns, which are ready for welding immediately.
Customizing a MIG gun can be viewed as a pre-emptive strike against issues or challenges that otherwise would add time and money to a welding operation.
Getting started
To choose or customize the right MIG gun, look at several aspects of the welding operation. Like a decision tree, one answer impacts the next choice.
First, consider the type and thickness of the base material, since both impact the filler metal selection. Once the material and filler metal are known, these dictate the welding parameters for the application.
Understanding the welding parameters is important because the gun selected must meet the amperage and voltage requirements. While it’s important to choose a gun with enough amperage for the job, the larger the gun, the heavier it is, which impacts operator comfort.
Next, think about the expected arc-on time and length of the welds. In addition to impacting the necessary amperage of the gun, these factors also play a role in ergonomics. For example, what length of gun is best for the physical space and length of the welds, and what handle style does the operator prefer?
These factors come together in building the right gun for the job.
Consider the welding cell
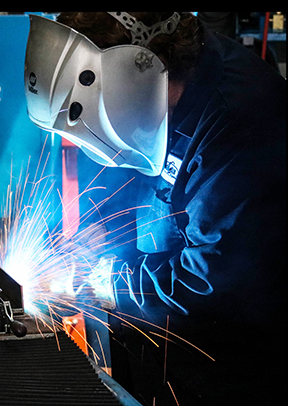
because the MIG gun selected must meet the amperage and
voltage requirements.
The physical space of the welding cell is also an important factor. If there are fixtures or jigs to work around, consider these when configuring the gun and selecting consumables.
For example, space limitations in the welding cell can impact cable length — the goal is always to have the shortest cable possible that still meets the needs of the application to avoid unnecessary coiling. The length and bend angle of the gun neck are also factors based on the available workspace and joint access. Remember, it is easier to make design choices like these up front rather than make changes to the gun after it’s purchased.
Also consider if the application requires table welding or out-of-position welds. For flat welds at a table, the operator may repeat the same motion over and over. In this case, comfort and repeatability is key and a gun with a shorter cable can likely be used, which helps reduce overall weight.
For out-of-position welds, the operator may need to move around a lot to complete the welds. Choosing a longer cable is helpful. Be aware, however, that a cable that is too long can be a tripping hazard for the operator or it can curl and tangle, causing wire feeding issues.
Choosing the cable
There are two main options when choosing a MIG gun cable: steel mono-coil or industrial-grade cables. Industrial-grade cables are more commonly used.
Steel mono-coil cables are well-suited for heavy-duty applications in harsh environments. These cables offer more rigidity and support to minimize feeding issues in applications where the wire must travel through a longer cable. Steel mono-coil cables are also used in applications where there is a risk they may get run over by equipment, such as a forklift.
Cable lengths can vary greatly — from 10 feet to 25 feet or longer. While a longer cable may be necessary in applications that require the operator to move around, again, try to use the shortest cable possible that will get the job done.
Smaller filler metal wire sizes typically call for a shorter cable, since it’s more difficult to push a smaller wire over a greater length. As wire size increases, the cable length can also increase.
Neck and handle options
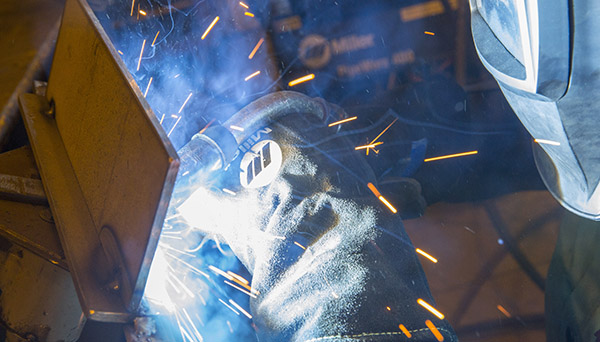
Deciding the best gun neck and handle choices for the application depends on several factors, including operator preference and comfort, as well as weld cell space limitations or fixtures. The type of filler metal being used also plays a role. For example, necks with less bend reduce the chances for bird-nesting or other feeding issues with thicker wires and softer wires.
Neck options are available with bends ranging from 30 degrees up to 80 degrees for applications where an extreme angle is needed to reach the weld joint. The choice of neck angle is often tied to the style of gun handle being used.
Gun handles are available in straight or curved options, and the decision typically comes down to operator preference. For a straight-handled gun, a neck with a 60-degree bend is a frequent choice, whereas pairing a curved-handled gun with a 45-degree neck is a popular combination.
Gun necks are also available in fixed or rotatable options. A rotatable neck makes it easier for the operator to change angles to access the weld joint without having to change out the gun. Straight handles are often paired with fixed necks, while curved handles are often paired with rotatable necks. Other features, such as trigger locking on the handle, which eliminates the need to hold the trigger during welding and increases comfort, can also be added when choosing the gun neck and handle.
The bottom line: Choose the option that makes it easiest and most comfortable for the operator to reach the weld joint.
Matching consumables to the gun
Some MIG gun configuration tools also allow users to choose specific styles or types of consumables. Consumables must be able to handle the amperage of the application; some higher amperage applications may require heavy-duty consumables. Inventory management may be another factor — selecting the same consumables across multiple weld cells, when possible, is typically more convenient and cost-effective. The three key consumables to consider are contact tips, nozzles and liners.
- Contact tips: Know the wire size and type when choosing the right size and style of contact tip. Some tips have finer threads, while others are designed for quick installation with a quarter or half-turn. Contact tips that “drop” into the nozzle are good for flat and horizontal welding, but they may not offer as good of performance out of position. Some styles offer longer life than others, too, so keep that in mind when making the choice. Pulsed MIG welding, for example, is a more aggressive mode of metal transfer that is tougher on consumables. Therefore, choose a more durable contact tip made of chrome zirconium to help extend contact tip life in these applications.
- Nozzles: Joint access, operating temperatures and arc-on time are important considerations in choosing the right nozzle. Brass nozzles are good for reducing the spatter adhesion in lower amperage applications, but does not perform well at higher temperatures. Therefore, copper nozzles are a better choice for higher amperage applications due to the ductility of the material.
- Liners: When the weld cell has a wire feeder mounted on a boom, front-loading liners help make changing liners faster, easier and safer. Specialty liners also exist that can aid feedability of the wire, especially in metal-cored or flux-cored applications.
Choosing the right MIG gun
Consider the challenges or needs of a specific welding application — and the preferences of the welding operator — when selecting the right MIG gun for the job. A customized MIG gun can improve operator comfort, extend the longevity of consumables and offer greater productivity and efficiency in the operation.
Being as comfortable as possible contributes to welding operator safety and productivity — and it’s a factor that can impact the quality of the finished weld. There are numerous issues that play a role in welding operator comfort, including the heat generated by the welding process, the repetitive motions and, at times, cumbersome equipment. These challenges can take a toll, resulting in aches, fatigue and physical and mental stress for welding operators. There are some steps, however, to help reduce the impact of these factors. These include choosing the right equipment for the job, utilizing tools and accessories designed to improve operator comfort, and following some best practices that promote proper operator form. Promoting operator comfort can lessen the chance of injuries associated with repetitive movement, as well as reduce overall fatigue. Choosing a GMAW gun that meets the needs of the application — and in some cases customizing the gun — is a critical way to impact welding operator comfort so he or she can achieve the best results. A gun’s trigger, handle, neck and power cable design all help determine how long a welding operator can comfortably weld without experiencing fatigue or stress. The application’s weld joint geometry also plays a role in welding operator comfort, and it impacts what components to choose for optimal joint access. Here are some issues to consider in GMAW gun selection that can impact comfort, as well as quality and productivity: Different welding guns can offer different “balance,” which refers to the feel and ease of movement experienced when the welding operator holds the gun. For example, a heavier gun that is balanced properly can lessen operator fatigue compared to a heavier gun that is not balanced properly. A gun that is properly balanced will feel natural in the operator’s hands and be easy to maneuver. When a gun is not balanced correctly, it might feel more unwieldy or uncomfortable to use. This can make a difference in operator comfort and productivity. Because welding applications differ for every welding operator, customizable GMAW guns can be a good option to gain greater comfort. Poor welding operator comfort can directly impact productivity and efficiency. Some gun manufacturers offer online resources to help welding operators configure a GMAW gun for the exact specifications of the job. This helps ensure the gun is suited to operator preferences and the needs of the application — for greater comfort and productivity. ttFor example, most welding operators do not make huge, sweeping movements when using a GMAW gun. Instead, they tend to use more minute, delicate maneuvering of the gun. Some configurations allow users to choose an option available for fume extraction guns — for example, a ball and socket swivel design that helps the vacuum hose to move separately from the handle. This improves flexibility and reduces the wrist fatigue for the welding operator. Utilizing proper weld position and form are additional ways that welding operators can maximize comfort on the job. Repetitive strain or prolonged uncomfortable postures can result in operator injury — or even the need for costly and time-consuming rework due to poor quality welds. Whenever possible, place the workpiece flat and move it into the most comfortable position. It’s also important to maintain a clean working environment. In some cases, a fume extraction gun paired with the proper portable fume extraction system can be a viable option to replace wearing a powered air purifying respirator and lessen the amount of equipment the welding operator must wear. To maintain compliance and safety, it’s always a good idea to consult an industrial hygienist to be certain that’s an appropriate step. In addition, operator comfort can be maximized by using stable posture and avoiding awkward body positioning, and by not working in one position for long periods. When welding in a seated position, operators should also have the workpiece slightly below elbow level. When the application requires standing for long periods, use a foot-rest. Having the right equipment, choosing equipment or accessories that are easy to operate and promote operator comfort, and utilizing proper welding technique and form are all important steps toward achieving a comfortable, safe work environment for welding operators. Lightweight welding guns with appropriate handle and neck designs for the job and for the operator can help achieve safe and productive results. The reduction of heat stress, wrist and neck fatigue and repetitive motions can also help decrease overall physical and mental stress for welding operators. To achieve optimal results, consider the numerous options available in tailoring a GMAW gun that is right for the application and operator preference.
When it comes to welding, too much of a good thing can often add up to unnecessary costs, potential downtime and lost productivity — especially if you have too large of a MIG gun for your application. Unfortunately, many people believe a common misconception: that you need a MIG gun rated to the highest amperage you expect to weld (e.g., a 400-amp gun for a 400-amp application). That is simply not true. In fact, a MIG gun that provides a higher amperage capacity than you need typically weighs more and may be less flexible, making it less comfortable to maneuver around weld joints. Higher amperage MIG guns also cost more. The truth is, because you spend time moving parts, tacking them and performing other pre- and post-weld activities, you rarely weld continuously enough to reach the maximum duty cycle for that MIG gun. Instead, it’s often better to choose the lightest, most flexible gun that meets your needs. For example, a MIG gun rated at 300 amps can typically weld at 400 amps and higher — for a limited amount of time — and do just as good of a job. In the United States, the National Electrical Manufacturers Association, or NEMA, establishes the MIG gun rating criteria. In Europe, similar standards are the responsibility of Conformité Européenne or European Conformity, also called CE. Under both agencies, MIG guns receive a rating that reflects the temperatures above which the handle or cable becomes uncomfortably warm. These ratings, however, do not identify the point at which the MIG gun risks damage or failure. Much of the difference lies in the duty cycle of the gun. Manufacturers have the option of rating their guns at 100-, 60- or 35-percent duty cycles. For that reason, there can be significant differences when comparing different MIG gun manufacturer’s products. Duty cycle is the amount of arc-on time within a 10-minute period. One MIG gun manufacturer may produce a 400-amp MIG gun that is capable of welding at 100 percent duty cycle, while another manufactures the same amperage MIG gun that can weld at only 60 percent duty cycle. In this example, the first MIG gun would be able to weld consistently at full amperage for a 10-minute time frame, whereas the latter would only be able to weld for 6 minutes. Before deciding which MIG gun to purchase, it is important to review the duty cycle ratios for the product. You can typically find this information in the product literature or on the manufacturer’s website. Based on the gun rating explanation above, it is also essential for you to consider the length of time you spend welding before you make your MIG gun selection. Look at how much time you actually spend welding over the course of 10 minutes. You may be surprised to discover that the average arc-on time is usually less than 5 minutes. Keep in mind that welding with a MIG gun rated to 300 amps would exceed its rated capacity if you were to use it at 400 amps and 100-percent duty cycle. However, if you used that same gun to weld at 400 amps and 50-percent duty cycle, it should work just fine. Similarly, if you had an application that required welding very thick metal at high current loads (even 500 amps or more) for a very short period of time, you might be able to use a gun rated at only 300 amps. As a general rule, a MIG gun becomes uncomfortably hot when it exceeds its full duty cycle temperature rating. If you find yourself welding for longer on a regular basis, you should consider either welding at a lower duty cycle or switching to a higher rated gun. Exceeding a MIG gun’s rated temperature capacity can lead to weakened connections and power cables, and shorten its working life. There are two types of heat that affect the handle and cable temperature on a MIG gun and also the amount of time you can weld with it: radiant heat from the arc and resistive heat from the cable. Both of these types of heat also factor into what rating of MIG gun you should select. Radiant heat is heat that reflects back to the handle from the welding arc and the base metal. It is responsible for most of the heat encountered by the MIG gun handle. Several factors affect it, including the material being welded. If you weld aluminum or stainless steel, for example, you will find that it reflects more heat than mild steel. The shielding gas mixture you use, as well as the welding transfer process, can also affect radiant heat. For example, argon creates a hotter arc than pure CO2, causing a MIG gun using an argon shielding gas mixture to reach its rated temperature at a lower amperage than when welding with pure CO2. If you use a spray transfer process, you may also find that your welding application generates more heat. This process requires an 85 percent or richer argon shielding gas mixture, along with a longer wire stick out and arc length, both of which increase the voltage in the application and the overall temperature. The result is, again, more radiant heat. Using a longer MIG gun neck can help minimize the impact of radiant heat on the handle by placing it further from the arc and keeping it cooler. The consumables you use can in turn affect the amount of heat that the neck absorbs. Take care to find consumables that connect tightly and have good mass, as these absorb heat better and can help prevent the neck from carrying as much heat to the handle. In addition to radiant heat, you may encounter resistive heat in your welding application. Resistive heat occurs by way of electrical resistance within the welding cable and is responsible for most of the heat in the cable. It occurs when the electricity generated by the power source cannot flow through the cable and cable connections. The energy of the “backed up” electricity is lost as heat. Having an adequately sized cable can minimize resistive heat; however, it cannot eliminate it entirely. A cable large enough to completely eliminate resistance would be too heavy and unwieldy to maneuver. Using a lighter MIG gun can often improve productivity since it is easier to maneuver for longer periods of time. Smaller MIG guns can also reduce your susceptibility to repetitive motion injuries, such as carpal tunnel syndrome. When choosing your MIG gun, remember that not all products are created equal. Two MIG guns rated to 300 amps could vary widely in terms of their overall size and weight. Take the time to research your options. Also, look for features like a ventilated handle that permits air to flow through it and keeps it running cooler. Such features can often allow a gun to be rated to a higher capacity without adding any size or weight. Finally, assess the time you spend welding, the process and shielding gas you use, and the materials you are welding. Doing so can help you select a gun that strikes the ideal balance between comfort and capacity.
The heat and repetitive motions that accompany gas metal arc welding (GMAW) can take their toll. Customizing your GMAW gun to match your application, however, can make a big difference in improving your comfort, and gaining the best welding performance. A GMAW gun’s trigger, handle, neck and power cable design all impact how long you can comfortably weld without experiencing fatigue or stress. By ensuring your comfort, you lessen the chance of injuries associated with repetitive movement and reduce overall fatigue. To help, some manufacturers offer online systems to help you configure a gun to your exact specifications.
When choosing a gas metal arc welding (GMAW) gun, there are several factors to consider. After all, welding is simply the result of one large electrical circuit — and the gun reflects that. The general rule is to select the lightest, most flexible gun for the application. The following considerations impact that selection: duty cycle, amperage requirement and work site location. Striking the right balance between gun size and capacity can increase the efficiency of a welding operation and decrease the risk of issues that could damage the equipment — including overheating. No matter the cause, there are several signs that precede catastrophic gun failure. Knowing these signs and taking steps to prevent them can minimize the cost for unnecessary downtime, reduce gun and consumable replacement costs, and prevent weld quality issues. Consider some simple troubleshooting tips and best practices.
Planned downtime for preventive maintenance in the welding operation is not time wasted. Rather, it is a crucial part of keeping production flowing smoothly and avoiding unplanned downtime. Proper maintenance can extend the life of consumables and equipment, and help prevent issues such as birdnesting or burnback that can lead to costly and time-consuming troubleshooting and rework. Keep in mind a few simple maintenance tips and best practices to get the most from your MIG gun and consumables. Prior to welding, ensure all connections are tight and that consumables and equipment are in good condition and free from damage. Start with the front of the gun and work your way back to the feeder. A tight neck connection is essential to carry the electrical current from the welding cable to the front-end consumables. Loose connections at either end of the neck can cause poor electrical conductivity, leading to weld defects and, potentially, overheating of the gun. When using a rotatable neck — one that allows the gun neck to be rotated to the desired position for welding, for increased flexibility and operator comfort — make sure the hand nut on the neck is tight and that the neck is secure in the cable fitting. Also, be sure to visually inspect the handle and trigger to check there are no missing screws or damage. The cable should be free of cuts, kinks and damage along the outer cover. Cuts in the cable can expose the internal copper wiring and create a potential safety hazard to the welding operator. In addition, these issues can lead to electrical resistance that causes heat buildup — and ultimately cable failure. In checking the feeder connection, make sure the power pin is fully inserted and tightly connected, otherwise it can cause birdnesting of the wire at the feeder. A loose connection can also cause electrical resistance at the joint, which could lead to an overheated gun. A clean liner that is the correct size is important in producing quality welds. The liner is often both the most difficult part of the gun to inspect and maintain, and one of the most frequent sources of weld troubles. A liner that is cut too short can cause wire feeding problems. Follow the manufacturer’s instructions for proper trimming and installation of the wire for the best results. Also, take care to keep the liner off the floor during installation to avoid picking up dirt and debris that could enter the weld pool and cause defects. A dirty liner reduces shielding gas flow, which can lead to porosity in the weld. Fragments of welding wire can also chip off and accumulate in the liner. Over time, this buildup can cause poor wire feeding, birdnesting and burnback. To maintain your liner, periodically blow clean compressed air through it to clear out dirt and debris. This task can be done in a few extra minutes during wire changeovers or when removing the wire from the gun — and helps save considerable time in troubleshooting problems later. MIG gun front-end consumables are exposed to heat and spatter and therefore often require frequent replacement. However, performing some simple maintenance can help extend consumable life and improve gun performance and weld quality. The gas diffuser provides gas flow to the weld pool and also connects to the neck and carries the electrical current to the contact tip. Make sure all connections are tight, and check the diffuser’s O-rings for cracks, cuts or damage. The nozzle’s main role is to focus the shielding gas around the weld pool. Watch for spatter buildup in the nozzle, which can obstruct gas flow and lead to problems due to inadequate shielding coverage. Use welper pliers to clean spatter from the nozzle. The contact tip is the last point of contact between the welding equipment and the welding wire. Keyholing of the contact tip is a concern to watch for with this consumable. This occurs when the wire passing through the tip wears an oblong-shaped slot into the diameter of the tip. Keyholing can put the wire out of center and cause problems such as an erratic arc. If you are experiencing wire feeding issues, try changing the contact tip or switching to a larger-size contact tip. Tips that look worn should be replaced. Taking the time for preventive maintenance can pay off in less downtime in the long run. Along with that, always remember to properly store your MIG gun consumables to help you achieve the best results and extend the life of your equipment. When not in use, the gun should be stored in a coiled position, either hanging or lying flat, such as on a shelf. Do not leave MIG guns on the floor of the shop, where there is a chance the cable could be run over, kinked or damaged. Ultimately, the better care you take care of this piece of equipment, the better results you can achieve in the weld cell.
MIG welding is considered among the easiest welding processes to learn and is useful for a variety of applications and industries. Since the welding wire constantly feeds through the MIG gun during the process, it doesn’t require frequent stopping, as with stick welding. The result is faster travel speeds and greater productivity. The versatility and speed of MIG welding also make it a good option for all-position welding on various metals, including mild and stainless steels, in a range of thicknesses. In addition, it produces a cleaner weld that requires less cleanup than stick or flux-cored welding. To maximize the benefits this process offers, however, it is imperative to select the right MIG gun for the job. In fact, this equipment’s specifications can significantly impact productivity, downtime, weld quality and operating costs — as well as welding operators’ comfort. Here is a look at different types of MIG guns and some key factors to consider when making the selection. It is important to select a MIG gun that offers adequate amperage and duty cycle for the job in order to prevent overheating. Duty cycle refers to the number of minutes in a 10-minute period that a gun can be operated at its full capacity without overheating. For example, a 60 percent duty cycle means six minutes of arc-on time in a 10-minute span. Because most welding operators don’t weld 100 percent of the time, it is often possible to use a lower amperage gun for a welding procedure that calls for a higher-amperage one; lower-amperage guns tend to be smaller and easier to maneuver, so they are more comfortable for the welding operator. When evaluating a gun’s amperage, it is important to consider the shielding gas that will be used. Most guns in the industry are tested and rated for duty cycle according to their performance with 100 percent CO2; this shielding gas tends to keep the gun cooler during operation. Conversely, a mixed-gas combination, such as 75 percent argon and 25 percent CO2, makes the arc hotter and therefore causes the gun to run hotter, which ultimately reduces duty cycle. For example, if a gun is rated at 100 percent duty cycle (based on the industry-standard testing with 100 percent CO2), its rating with mixed gases will be lower. It is important to pay attention to the duty cycle and shielding gas combination — if a gun is rated at only 60 percent duty cycle with CO2, the use of mixed gases will cause the gun to operate hotter and become less durable. Deciding between a water- or air-cooled MIG gun depends largely on the application and amperage requirements, welding operator’s preference and cost considerations. Applications that involve welding sheet metal for only a few minutes every hour have little need for the benefits of a water-cooled system. On the other hand, shops with stationary equipment that repeatedly weld at 600 amps will likely need a water-cooled MIG gun to handle the heat the applications generate. A water-cooled MIG welding system pumps cooling solution from a radiator unit, usually integrated inside or near the power source, through hoses inside the cable bundle, and into the gun handle and neck. The coolant then returns to the radiator, where a baffling system releases the heat absorbed by the coolant. The ambient air and shielding gas further disperse the heat from the welding arc. Conversely, an air-cooled system relies solely on the ambient air and shielding gas to dissipate the heat that builds up along the length of the welding circuit. These systems, which range from 150 to 600 amps, use much thicker copper cabling than water-cooled systems. By comparison, water-cooled guns range from 300 to 600 amps. Each system has its advantages and disadvantages. Water-cooled guns are more expensive upfront, and can require more maintenance and operational costs. However, water-cooled guns can be much lighter and more flexible than air-cooled guns, so they can provide productivity advantages by reducing operator fatigue. But because water-cooled guns require more equipment, they can also be impractical for applications that require portability. While a lower-amperage gun can be appropriate for some applications, be sure it offers the necessary welding capacity for the job. A light-duty MIG gun is often the best choice for applications that require short arc-on times, such as tacking parts or welding sheet metal. Light-duty guns typically provide 100 to 300 amps of capacity, and they tend to be smaller and weigh less than heavier-duty guns. Most light-duty MIG guns have small, compact handles as well, making them more comfortable for the welding operator. Light-duty MIG guns offer standard features at a lower price. They use light- or standard-duty consumables (nozzles, contact tips and retaining heads), which have less mass and are less expensive than their heavy-duty counterparts. The strain relief on light-duty guns is usually composed of a flexible rubber component and, in some cases, may be absent. As a result, care should be taken to prevent kinking that may impair wire feeding and gas flow. Also note, overworking a light-duty MIG gun can lead to premature failure, so this type of gun may not be appropriate for a facility that has multiple applications with various amperage needs. At the other end of the spectrum, heavy-duty MIG guns are the best choice for jobs that require long arc-on times or multiple passes on thick sections of material, including many applications found in heavy equipment manufacturing and other demanding welding jobs. These guns generally range from 400 to 600 amps and are available in air- and water-cooled models. They often have larger handles to accommodate the larger cables that are required to deliver these higher amperages. The guns frequently use heavy-duty front-end consumables that are capable of withstanding high amperages and longer arc-on times. The necks are often longer as well, to put more distance between the welding operator and the high heat output from the arc. For some applications and welding operations, a fume extraction gun may be the best option. Industry standards from the Occupational Safety and Health Administration(OSHA) and other safety regulatory bodies that dictate allowable exposure limits of welding fumes and other particulates (including hexavalent chromium) have led many companies to make the investment. Similarly, companies that seek to optimize welding operator safety and attract new skilled welding operators to the field may want to consider these guns, as they can help create a more appealing work environment. Fume extraction guns are available in amperages typically ranging from 300 to 600 amps, as well as various cable styles and handle designs. As with all welding equipment, they have their advantages and limitations, best applications, maintenance requirements and more. One distinct advantage to fume extraction guns is that they remove the fumes at the source, minimizing the amount that enters the welding operator’s immediate breathing zone. Fume extraction guns can, in combination with many other variables in the welding operation — welding wire selection, specific transfer methods and welding processes, welding operator behavior and base material selection — help companies maintain compliance with safety regulations and create a cleaner, more comfortable welding environment. These guns operate by capturing the fumes generated by the welding process right at the source, over and around the weld pool. Various manufacturers have proprietary means of constructing guns to conduct this action but, at a basic level, they all operate similarly: by mass flow or the movement of material. This movement occurs by way of a vacuum chamber that suctions the fumes through the handle of the gun and into the gun’s hose through to a port on the filtration system (sometimes informally referred to as a vacuum box). Fume extraction guns are well-suited for applications that use solid, flux-cored or metal cored welding wire as well as those conducted in confined spaces. These include, but are not limited to, applications in the shipbuilding and heavy equipment manufacturing industries, as well as general manufacturing and fabrication. They are also ideal for welding on mild and carbon steel applications, and on stainless steel applications, as this material generates greater levels of hexavalent chromium. In addition, the guns work well on high amperage and high deposition rate applications. When it comes to cable selection, choosing the smallest, shortest and lightest cable capable of handling the amperage can offer greater flexibility, making it easier to maneuver the MIG gun and minimize clutter in the workspace. Manufacturers offer industrial cables ranging from 8 to 25 feet long. The longer the cable, the more chance it can get coiled around things in the weld cell or looped on the floor and possibly disrupt wire feeding. However, sometimes a longer cable is necessary if the part being welded is very large or if welding operators must move around corners or over fixtures to finish the task at hand. In these cases, where operators are moving back and forth between long and short distances, a steel mono coil cable might be the better choice. This type of cable doesn’t kink as easily as standard industrial cables and can provide smoother wire feeding. A MIG gun’s handle and neck design can impact how long an operator can weld without experiencing fatigue. Handle options include straight or curved, both of which come in vented styles; the choice often boils down to welding operator preference. A straight handle is the best choice for operators who prefer a trigger on top, since curved handles for the most part do not offer this option. With a straight handle, the operator can rotate the neck to place the trigger on top or on bottom. In the end, minimizing fatigue, reducing repetitive motion and decreasing overall physical stress are key factors that contribute to a safer, more comfortable and more productive environment. Choosing a MIG gun that offers the best comfort and operates at the coolest temperature allowed by the application can help improve arc-on time and productivity — and, ultimately, increase the profitability of the welding operation.
As with any piece of equipment in the shop or on the jobsite, proper storage and care of MIG guns and welding consumables are important. These may seem like rather insignificant components at first, but they can have a big impact on productivity, costs, weld quality and even safety. MIG guns and consumables (e.g. contact tips, nozzles, liners and gas diffusers) that are not properly stored or maintained can pick up dirt, debris and oil, which can hinder gas flow during the welding process and lead to contamination of the weld. Proper storage and care is especially important in humid environments or on jobsites near water, such as shipyards, since exposure to moisture can lead to corrosion of welding guns and consumables — particularly the MIG gun liner. Proper storage of MIG guns, cables and consumables not only helps protect the equipment from damage, but it also improves jobsite safety. Leaving MIG guns or consumables lying on the floor or the ground can lead to tripping hazards that can negatively impact worker safety. It also can cause damage to the welding cables, which could be cut or torn by workplace equipment, such as forklifts. The risk of picking up contaminants is greater if the gun is left on the ground, and can lead to poor welding performance and possibly a shorter life span. It is not uncommon for some welding operators to place the whole MIG gun nozzle and neck into a metal tube for storage. However, this practice puts extra force on the nozzle and/or front end of the gun each time the welding operator removes it from the tube. This action can cause broken parts or nicks on the nozzle where spatter can adhere, causing poor shielding gas flow, poor weld quality and downtime for rework. Another common storage mistake is to hang the MIG gun by its trigger. This practice will naturally change the activation point for the way the trigger level engages the switch. Over time, the MIG gun will not start in the same manner because the welding operator will have to pull the trigger progressively harder each time. Ultimately, the trigger will no longer function properly (or at all) and will require replacement. Any of these common, but poor, storage practices can weaken the MIG gun and/or consumables, leading to poor performance that impacts productivity, quality and costs. For proper storage of MIG guns, keep them out of the dirt; avoid hanging them in a way that could cause damage to the cable or trigger; and keep them in a safe, out-of-the-way location. Welding operators should coil the MIG gun and cable into as small of a loop as possible for storage — make sure it’s not dragging or hanging in the path of high traffic areas. Use a gun hanger when possible for storage, and take care that the gun is hanging from near the handle and that the neck is in the air, as opposed to pointing downward. If a gun hanger is not available, coil the cable and place the MIG gun on an elevated tube, so that gun and cable is off the floor and away from debris and dirt. Depending on the environment, welding operators may choose to coil the MIG gun and lay it flat on an elevated surface. When implementing this measure, make sure the neck is at the topmost vertical point after coiling the gun. Also, minimize a MIG gun’s exposure to the atmosphere when it’s not being used for welding. Doing so can help keep this equipment in good working condition for longer. MIG gun consumables benefit from proper storage and handling, as well. A few best practices can help to achieve a high-quality weld and maintain productivity. Storing consumables, unwrapped, in a bin — especially nozzles — can lead to scratching that can negatively impact performance and cause spatter to adhere more readily. Keep these and other consumables, such as liners and contact tips, in their original, sealed packaging until they are ready for use. Doing so helps protect the consumables from moisture, dirt and other debris that can damage them and minimizes the opportunity to cause poor weld quality. The longer consumables are protected from the atmosphere, the better they will perform — contact tips and nozzles that are not stored properly can wear before they are even used. Always wear gloves when handling consumables. Oil and dirt from the welding operator’s hands can contaminate them and lead to problems in the weld. When installing MIG gun liners, avoid uncoiling the liner and letting it drag on the floor when feeding it through the gun. When that happens, any contaminants on the floor will push through the MIG gun and have the potential to impede gas flow, shielding gas coverage and wire feeding — all factors that can lead to quality issues, downtime and potentially, cost for rework. Instead, use both hands: Hold the gun in one hand and uncoil the liner naturally with the other hand while feeding it through the gun. Proper storage of MIG guns and consumables can seem like a small issue, especially in a large shop or jobsite. However, it can have a great effect on costs, productivity and weld quality. Damaged equipment and consumables can lead to shorter product life, rework of welds and increased downtime for maintenance and replacement.
There are many considerations that factor into a company’s ability to achieve the best quality and highest productivity in the welding operation. Everything from selecting the right power source and welding process to the organization of the weld cell and workflow play a role in that success. Although a smaller part of the whole operation, MIG guns also play an important part. In addition to being responsible for delivering the current to create the arc that generates the weld, MIG guns are also the one piece of equipment that directly impacts the welding operator — day in and day out, shift after shift. The heat of the gun, along with the weight and repetitive motion of welding make it necessary to find the right gun to improve comfort and allow the welding operator the opportunity to put his or her best skills forward. With that in mind, MIG gun manufacturers throughout the industry have identified ways to make MIG guns more ergonomic and perform better. Changes that help expedite welding operator training and improve the welding environment also continue to emerge, as do MIG guns designed to reduce costs. Manufacturers continue to build features into MIG guns to help welding operators gain the highest level of quality, while also assisting them in producing a greater level of throughput. While it may seem like a minor advancement, the addition of a swivel at the base of the MIG gun handle has become an important feature that contributes positively to welding operator comfort and productivity. MIG guns that provide a 360-degree swivel offer greater maneuverability for accessing weld joints and are less fatiguing to adjust throughout the course of a welding shift. This feature also reduces the strain on the power cable, resulting in less downtime and costs for changeover. The addition of rubber handle over-molding, which is becoming more popular in industrial settings, can further improve MIG gun ergonomics by providing welding operators with a more secure and comfortable grip. The over-molding can also help reduce vibrations during the welding process, minimizing hand and wrist fatigue. MIG gun manufacturers are also adding in features to their products that help minimize costs. Among those are front-loading liners. These liners, as their name implies, load from the front of the gun (after the initial installation of the system), as opposed to conventional liners that load from the back of the gun. The benefit to front-loading liners is that they simplify installation. After the initial installation of the front-loading liner system (completed similarly to a conventional liner), the welding operator or maintenance personnel needs only to remove the nozzle and retaining head, pull out the existing front-loading liner and replace it with a new one; the gun remains attached to the feeder during this process, and wire also remains in place. As a rule, front-loading liners can cut installation time in half, minimizing costly downtime. Some manufacturers also offer a spring-loaded module that works in conjunction with a front-load liner to help minimize issues if the liner has accidentally been trimmed to an incorrect length. These modules sit in the power pin and put forward pressure on the liner after installing it from the front of the gun, providing up to 1 inch of forgiveness if the liner is too short. As companies seek out ways to address environmental regulations and create a safer, cleaner and more compliant welding operation, fume extraction guns have increased in popularity. These guns capture weld fume and visible smoke right at the source, over and around the weld pool. They operate by way of a vacuum chamber that suctions the fumes through the handle of the gun, into the gun’s hose through to a port on the filtration system. While effective in helping remove weld fume, fume extraction guns in the past have been rather heavy and bulky; they are larger than standard MIG guns in order to accommodate the vacuum chamber and the extraction hose. This extra bulk could increase welding operator fatigue and limit his or her ability to maneuver around the welding application. Manufacturers today offer fume extraction guns that are smaller (near the size of a standard MIG gun) and that feature swiveled handles to make them easier to manage. Some fume extraction guns now also feature adjustable extraction control regulators at the front of the gun handle. These allow welding operators to easily balance suction with shielding gas flow to protect against porosity. As the fabrication and manufacturing industries evolve, companies need to seek out welding equipment that can meet those changing demands — and no single MIG gun can do the job for every application. To ensure companies have the exact MIG gun necessary, many manufacturers have moved toward configurable products. MIG guns can be custom built, usually using an online configurator, according to multiple options: amperage, cable type and length, handle type (straight or curved), and neck length and angle. These configurators also offer the option to select the type of contact tip and MIG gun liners. Upon selecting the desired features for a given MIG gun, companies can purchase the unique part number through a welding distributor. Adding to the configurability of many of today’s MIG guns are accessories designed to augment their performance. Flexible necks, for example, can save labor and time by allowing the welding operator to rotate or bend the neck to the desired angle. Neck grips can add to operator comfort by reducing heat exposure and helping the welding operator maintain a steady position, leading to less fatigue and better weld quality. With the advent of advanced welding information management systems — software-driven solutions that gather weld data and can monitor most every aspect of the welding process — specialized MIG guns with a built-interface have also been introduced to the marketplace. These guns pair with the weld sequencing functions of the welding information management system, using the screen to guide the welding operator through the order and placement of each weld. Similarly, some welding performance training systems feature MIG guns with built-in displays that provide visual feedback regarding proper gun angle, travel speeds and more, allowing the welding operator to make corrections as he or she trains. Both types of guns have been designed to help streamline welding operator training and, like other MIG guns in today’s marketplace, can help support the creation of high-quality welds and positive levels of productivity in the welding operation. Equipment repairs are a fact of life on most jobsites, so finding ways to reduce costs and downtime while making them is important for overall efficiency and productivity — and the bottom line. The welding operation on a jobsite, just like any other portion of the business, offers opportunities to conserve resources and extend equipment life. Proper selection, handling and use of welding consumables and accessories can be helpful when it comes to getting the most out of a MIG gun, as can proper gun maintenance. Jobsites are often exposed to many environmental challenges, including extreme hot and cold temperatures, and the presence of rain and mud. It’s important to keep nozzles, gas diffusers and contact tips in the original packaging to protect against these elements until they are ready for use. Doing so also prevents scratches and/or dents from forming where spatter can accumulate and cause the consumables to fail prematurely. In addition, it prevents dirt, oil or other debris from adhering to the consumables and inadvertently entering the weld puddle, which can lead to poor weld quality. Remember, proper storage and handling doesn’t just lower actual costs for consumables by extending consumable life, it can also prevent weld defects that require costly and time-consuming rework. Choose the most appropriate neck for a MIG welding application in order to increase comfort and control, and save money. Rotatable necks, for example, can be adjusted without tools, so neck angles can be quickly changed during a welding repair once the desired position is determined. This feature is important on a jobsite where welding may be done in various positions or in tight spaces, and it helps reduce downtime for changing over MIG guns or for purchasing and inventorying extras. Rotatable necks are especially useful for welding on different angles. For hard-to-reach areas, consider a neck coupler, which allows for two existing necks to connect to extend their reach — again without the cost of purchasing a new or specialized neck. Flex necks are another good option for saving money and gaining greater comfort and control, particularly for applications with tighter joints. The operator can bend the neck to multiple angles to work around corners or get into small spaces for greater flexibility during repairs, without the expense of stocking different neck angles. Regularly perform a visual inspection of the nozzle — inside and outside — to look for spatter build-up. If there is accumulation, either clean the nozzle with a tool designed specifically for the job or replace the nozzle when necessary. During the inspection, also check that the nozzle, contact tip and retaining head are tightened properly, as these components can naturally loosen during welding. Inspecting and tightening consumables help ensure good shielding gas coverage, reliable electrical conductivity and consistent weld quality, as well as reduce costs for purchasing and replacing new consumables. It is also important to inspect the power cable on the MIG gun for any wear or damage, replacing it as necessary to avoid potential problems. Always trim MIG gun liners according to the manufacturer’s recommendations, using the proper tools and cutting the liner to the correct length. Too long of a liner can cause kinking, while cutting it too short allows debris to build up between the liner and the gas diffuser. Either way, the wrong liner length can cause poor wire feeding and premature failure of both the liner and the contact tip, adding unnecessary costs. Use a liner gauge when possible to determine the proper length for the particular liner being used. Also be certain that there are no burrs or sharp edges after the liner is cut. Also, keep the liner away from contaminants (e.g., don’t let it drag on the ground) during installation. As further protection, the welding operator’s hands or gloves should be clean when handling the liner. These precautions protect against contaminants that could enter the weld puddle and cause costly weld quality issues or downtime for rework. Use the shortest length MIG gun cable possible for the welding application, as it minimizes the opportunity for kinking, as well as premature wear of both the cable and the MIG gun liner. A shorter cable also helps prevent wire-feeding problems that could lead to an erratic arc, poor weld quality and unnecessary downtime for rework or consumable replacement. It also tends to cost less, adding to savings for repair jobs. In addition, remember to choose the correct diameter liner and contact tip for the welding wire, as this prevents similar problems and helps extend the life of these consumables. While up-front cost is an important factor when choosing consumables, consider the long-term savings offered by purchasing sturdier and more expensive consumables. These consumables likely will last longer — especially in the face of the harsh conditions of some jobsites — reducing the downtime associated with changeover and the cost of more frequent replacement of the consumables themselves. As an additional defense against spatter accumulation, purchase nozzles that have a smooth, non-porous surface. Be sure to check that the nozzles are free of any sharp edges or flat spots that would further allow spatter to adhere. Whenever possible, purchase MIG guns and consumables that are backed by a reliable manufacturer’s warranty, and use all guns and consumables as intended so as not to void the terms and conditions. Keeping these simple tips in mind can help reduce the downtime spent on maintenance and MIG gun or consumable changeover, so welding operators can get back to welding faster, get equipment back into service sooner and save money.
When it comes to welding, no two applications are alike. Just as it’s important to select a power source that is right for the job, it is also essential to select a MIG gun that will deliver the appropriate amperage and cooling capabilities. There are four main MIG gun categories to consider when making the selection: light-duty, heavy-duty, air-cooled and water-cooled. Like any welding equipment, each has its advantages and disadvantages, as well as applications for which it is best suited. Depending on the amount of arc-on time required for an application and the amperage needed, a light- or heavy-duty MIG gun may be the best choice. The key is to make sure that the gun provides the necessary amperage to avoid overheating and premature failure. As a general rule, light-duty MIG guns work well for welding on thin materials, like sheet metal, for tacking or for other applications that require short arc-on times. These guns tend to be smaller and lighter than heavy-duty guns, making them more comfortable for the welding operator, and most MIG gun manufacturers offer them in models ranging from 100 to 300 amps. Light-duty MIG guns also tend to be less expensive than heavy-duty ones and use light- or standard-duty consumables (nozzles, contact tips and gas diffusers) that are also less expensive. There are some limitations to consider when using light-duty MIG guns, too. Despite the lower purchase price, these guns may need to be replaced more frequently due to the lighter-duty components. For example, the strain relief on light-duty guns is often made from a flexible rubber component or absent all together, which can sometimes lead to kinking and cause poor wire feeding and/or shielding gas flow. Also, some unicables on light-duty MIG guns have crimped connections and may not be able to be repaired, requiring replacement of the cable or possibly the entire gun. Heavy-duty MIG guns are typically the best option for applications requiring multiple passes on thick sections of material or for long durations of welding. They are available in the marketplace in both air- and water-cooled models (discussed below) ranging from 400 to 600 amps. The necks on these guns are often longer, which creates more distance between the welding operator and the high heat from the arc, and the handles on these guns are usually larger, too. While the handle size is vital to accommodate the larger cables necessary for higher amperage output, it can make the gun more cumbersome for the welding operator to maneuver. These guns frequently also use heavy-duty front-end consumables that are capable of withstanding high amperages and longer arc-on times, but they are more expensive. Choosing between a water- or air-cooled model for high-amperage, heavier-duty applications depends on several factors, including the amperage required, cost and operator preference. As with the considerations for a light-duty gun, applications that involve welding at lower amperages for less amount of time are best suited to air-cooled MIG guns. These guns rely on the ambient air and shielding gas to dissipate the heat that builds up along the length of the welding circuit. These systems, which range from 150 to 600 amps, use much thicker copper cabling than water-cooled systems so the guns are generally larger. Water-cooled MIG guns are best suited for applications that require long, continuous welds and are typically available in a range from 300 to 600 amps. These guns operate via a water-cooled MIG welding system that pumps cooling solution from a radiator unit, usually integrated inside or near the power source. This coolant passes through hoses inside the cable bundle and into the gun handle and neck. The coolant returns to the radiator where a baffling system releases the heat absorbed by the coolant. The ambient air and shielding gas further disperses the heat from the welding arc. Each MIG gun has its advantages and disadvantages. Water-cooled MIG guns are more expensive up-front and can require more maintenance and operational costs. However, water-cooled guns also are much smaller and lighter than air-cooled guns, so they can provide productivity advantages by reducing welding operator fatigue. Also, because water-cooled guns require more equipment, they can be impractical for applications that require portability. The goal when selecting between air- or water-cooled guns, as well as light- or heavy-duty models, is to weigh out pros and cons like these and always make the selection that will provide the capacity to prevent downtime and drive productivity. Outdoor jobsites can be harsh environments for welding equipment, including guns and consumables. When it comes to MIG or flux-cored (FCAW) welding on the jobsite, selecting the right gun for the application, and following some basic maintenance and preparation tips can help make guns and consumables last longer — factors that can help reduce costs, increase productivity and improve weld quality. Keeping this equipment up and running also helps minimize unscheduled downtime, which is key to meeting contract deadlines and keeping the business moving. This article discusses tips for protecting and maintaining MIG guns and consumables on the jobsite. Welding guns often take a lot of abuse on jobsites and in job shops, so it’s important to look for a durable gun that meets the demands of a specific application. Variables to keep in mind when selecting the gun include the material type and thickness to be welded, and how much welding will be required (if welding makes up one hour versus seven hours of each workday, for example). Additional challenges on outdoor jobsites are the weather and wind, which can blow the shielding gas away from the weld puddle, causing porosity in the completed weld. For this reason, a popular option for many outside contractors is a flux-cored welding gun, which can be used with self-shielded wire that generates its own shielding gas to reduce problems caused by wind. Whether using a MIG gun or a flux-cored gun, it’s important to select a gun with a rigid strain relief. A good strain relief (which refers to the connection between the power cable and power pin) helps minimize kinking, which can lead to poor wire feeding, an unstable arc and poor weld quality. Some additional issues to consider when selecting a gun include: • The gun should have enough amperage to meet the needs of the application. To determine the necessary amperage, consider the material type and thickness and wire size being used. • The power cable must have enough copper content to handle the amperage that will be put through it. When possible, use shorter power cables on the MIG gun to minimize costs and downtime further. As a general rule, shorter power cables are less expensive and offer better maneuverability. Shorter power cables also can help minimize wire-feeding problems associated with kinking and coiling. • The handle of the gun often is what takes the most abuse, so make sure to select a handle durable enough for the application, as some handles are designed for more light-duty applications. Choosing a handle that is comfortable for the welding operator also is important, so consider using the smallest handle that can still meet amperage needs to help minimize fatigue. • MIG gun triggers come in various styles and designs, such as standard, locking and dual schedule, and selecting the trigger often comes down to operator preference. Select a trigger that’s comfortable to use and easy to access for servicing. Some applications may be well suited for a dual-pull trigger, which allows the operator to easily switch between settings without stopping and walking back to the power source to make changes. Reducing those trips to the power source also helps improve safety by eliminating the need to navigate through cluttered jobsites and with it the potential for slips or falls. Regularly inspecting the MIG gun can be an important part of reducing costs and ensuring good welding performance, impacting productivity and efficiency. Preventive maintenance for MIG guns and flux-cored guns doesn’t have to be time-consuming or difficult. Often, the fundamental principles are the same, whether the welding is being done on a jobsite outside or in a shop. Here are some key tips for maintaining a welding gun on the jobsite: • Make sure all connections are tight. Inspect the connections between the contact tip, gas diffuser, nozzle and power pin. The wire feeder connection (where the power pin plugs into the feeder) must be tightened properly and should be free of dirt and debris. Loose or dirty wire feeder connections can cause heat to build up, leading to voltage drops that adversely affect the welding arc and may cause premature gun failure. Tighten the connection according to the manufacturer’s specification or replace the direct plug if necessary to obtain a secure fit. • Properly care for the gun liner. Make sure to install only a clean gun liner. Dragging a liner through the dirt while installing it can allow dirt and debris to accumulate on it, causing wire feeding issues. Having the proper cut length on the liner is also extremely important to help prevent birdnesting. It’s not uncommon during the course of welding for the gun liner to become clogged with debris. This accumulation of debris can, over time, lead to poor wire feeding, bird-nesting and burnbacks that require downtime to fix. Spraying compressed air through the liner can help clear out potential blockages. • Visually inspect the power cable. Look for any damage such as nicks or cuts in the power cable, which can affect wire feeding or conductivity. Power cable maintenance is an important part of eliminating unnecessary equipment costs and improving jobsite safety. Cuts in the cable can expose copper wire and lead to a potential shock hazard, while kinking obstructs gas flow and wire feeding, which can result in weld defects and arc instability. • Inspect the handle and trigger. Typically these components require little maintenance beyond visual inspection, but be sure to regularly look for cracks on the handle or missing screws. Check that the gun trigger is not sticking or otherwise malfunctioning, and replace these components as necessary. • Check the gun neck. Loose connections at either end of the neck can cause electrical resistance that leads to poor weld quality and/or consumable failures. Also, visually inspect the insulators on the neck and replace them if damaged. These insulators prevent electrically live components from exposure, ensuring operator safety and longevity of equipment. • Be mindful of consumables. Frequently inspect the nozzle and contact tip for spatter build-up, which can obstruct shielding gas flow and cause weld defects that will need to be reworked, costing time and money. Spatter build-up also can cause consumables to fail prematurely. Replace the nozzle and contact tip when necessary. • Store the gun and consumables properly. Welding equipment performs best when it’s properly stored, such as in a box or cabinet, and kept out of the elements. Liners can become corroded from exposure to the environment, which impacts the conductivity and performance of the gun. Care and maintenance can reduce costs
The MIG welding process offers many benefits for various applications and industries, including fabrication, manufacturing and general maintenance. It’s one of the easiest welding processes to learn and offers good control on thin metals. Because MIG welding uses a spool to constantly feed a wire through a welding gun, it doesn’t require frequent stopping as with stick welding. This feature makes it an efficient process that offers faster travel speeds and productivity benefits. The versatility and speed of MIG welding also make it a good option for all-position welding on various metals, including mild and stainless steels and aluminum, in a range of thicknesses. In addition, it produces a cleaner weld that requires less cleanup than stick or flux-cored welding. Selecting the right gun for the job is important to achieving good results and realizing all of the benefits MIG welding can provide. The choice of gun can have a significant impact on productivity, downtime, weld quality and operating costs, not to mention welding operator comfort. This article discusses the options to consider in selecting the appropriate MIG gun for the job. Amperage and duty cycle rating are both important considerations, but keep in mind that when it comes to amperage, bigger isn’t always better. Selecting a larger amperage gun than necessary for an application can cost money upfront and cause operator discomfort due to the increased weight, which can result in unnecessary downtime. Welding operators are often better off selecting the smallest amperage gun possible for the application, to provide them with a lighter-weight, more flexible gun that can reduce fatigue and associated downtime. Lower amperage guns also typically cost less. Duty cycle refers to the number of minutes in a 10-minute period that a gun can be operated at its full capacity without overheating. For example, a 60 percent duty cycle means six minutes of arc-on time in a 10-minute span. Because most welding operators don’t weld 100 percent of the time, it is often possible to use a lower amperage gun for a welding procedure that calls for a higher amperage one. A lower amperage MIG gun should still be capable of operating at the necessary capacity, while also offering the benefit of being easier to maneuver. That improved maneuverability can help improve weld quality and reduce the need for rework. While a lower amperage gun is appropriate for some applications, be sure the gun offers the necessary welding capacity for the job. Overworking a light-duty MIG gun can lead to premature failure. It’s also important to consider if a facility has multiple applications that make it necessary to have a gun that can handle various amperage needs. A light-duty MIG gun is often the best choice for applications that require short arc-on times, such as tacking parts or welding sheet metal. Light-duty guns typically provide 100 to 300 amps of capacity, and they tend to be smaller and weigh less than higher duty guns. Most light-duty MIG guns have small, compact handles as well, making them more comfortable for the welding operator. Light-duty MIG guns offer standard features at a lower price but typically need to be replaced more frequently. They also often use light or standard duty consumables (nozzles, contact tips and retaining heads), which have less mass and are less expensive than their heavy-duty counterparts. The strain relief on light-duty guns is usually composed of a flexible rubber component and in some cases may be absent, causing the opportunity for kinking that may lead to poor wire feeding and gas flow. Also, some unicables on light-duty MIG guns have crimped connections and may not be able to be repaired, requiring replacement of the cable or possibly the entire gun. Welding operators should watch for these potential issues. At the other end of the spectrum, heavy-duty MIG guns are often the best choice for jobs that require long arc-on times or multiple passes on thick sections of material, including many applications found in heavy equipment manufacturing and other demanding welding jobs. These guns generally range from 400 to 600 amps and are available in air- and water-cooled models. They often have larger handles to accommodate the larger cables necessary to provide the higher amperages. The guns frequently use heavy-duty front-end consumables that are capable of withstanding high amperages and longer arc-on times. The necks often are longer as well, to put more distance between the welding operator and the high heat output from the arc. When using a heavy-duty MIG gun, choosing between a water- or air-cooled model depends largely on the application and amperage requirements, operator preference and cost considerations. Applications that involve welding sheet metal for only a few minutes every hour have little need for the benefits a water-cooled system can provide. Whereas shops with stationary equipment that repeatedly weld at 600 amps likely will need a water-cooled system to handle the heat of the application. A water-cooled MIG welding system pumps cooling solution from a radiator unit, usually integrated inside or near the power source, through hoses inside the cable bundle and into the gun handle and neck. The coolant returns to the radiator where a baffling system releases the heat absorbed by the coolant. The ambient air and shielding gas further disperses the heat from the welding arc. Water-cooled guns range from 300 to 600 amps. An air-cooled system relies on the ambient air and shielding gas to dissipate the heat that builds up along the length of the welding circuit. These systems, which range from 150 to 600 amps, use much thicker copper cabling than water-cooled systems. Each system has advantages and disadvantages. Water-cooled guns are more expensive up-front and can require more maintenance and operational costs. However, water-cooled guns also are much smaller and lighter than air-cooled guns, so they can provide productivity advantages due to reduced operator fatigue. Because water-cooled guns require more equipment, they can be impractical for applications that require portability. A MIG gun’s handle, neck and power cable design can all impact how long an operator can weld without experiencing fatigue. Handle options include straight or curved — both of which come in vented styles — and the choice often boils down to welding operator preference. A straight handle is the best choice for operators who prefer a trigger on top, since curved handles for the most part do not offer this option. With a straight handle, the neck can be rotated to place the trigger on top or on bottom. In heavy-duty applications, some welding operators drape the power cable over their shoulder, and in those cases a trigger on top is more accessible. When it comes to cable selection, smaller, shorter and lighter power cables can offer greater flexibility, making it easier to maneuver the equipment and avoid clutter in the workspace. Manufacturers offer cables ranging from 8 to 25 feet long, and shorter cables often contribute to better feedability of the wire. The longer the cable, the more chance it can get coiled around things in the weld cell or looped on the floor and possibly disrupt wire feeding. However, sometimes a longer cable is necessary if the part being welding is very large. Other options to consider are the addition of a heat shield, which protects the welding operator from the heat output of a high amperage MIG gun and allows for longer arc-on time. Adding a unicable cover can protect the power cable from a harsh environment. Just as with standard MIG welding, self-shielded flux-cored welding (FCAW-SS) can offer high productivity and quality advantages in certain fabrication applications, while also providing easier training and operation. Many of the considerations for selecting a FCAW-SS gun are similar to those for selecting a standard MIG gun. Amperage and duty cycle ratings and the application requirements remain among the most important elements to consider in selecting either type of gun. Here are some issues to keep in mind for self-shielded FCAW-SS gun selection: • Operators can choose between a fixed liner and a replaceable liner, which (as the name suggests) can be replaced if it becomes clogged or damaged. • Guns with fixed liners typically have external trigger leads, while guns with replaceable liners commonly have trigger leads internal to the power cable, which prevents catching on surrounding equipment. This can be a consideration for applications that require welding around hard corners or fixtures. • Trigger options include standard or dual-schedule to allow welding operators to increase or decrease wire feed speed at the gun with the flip of a switch. Minimizing fatigue, reducing repetitive motion and decreasing overall physical stress are key factors that contribute to a safer, more comfortable and more productive environment. Choosing a MIG gun that offers the best comfort and operates at the coolest temperature allowed by the application can help improve productivity and, ultimately, the profitability of the welding operation by increasing arc-on time.
Taking into account the heat, the repetitive motions and the sometimes cumbersome equipment, gas metal arc welding (GMAW) can sometimes take a toll on welding operators in the form of aches, fatigue, and physical and mental stress. But there are tools and accessories that promote a more comfortable environment and minimize downtime. A welding gun’s handle, neck and power cable design all can significantly impact the duration of time a welding operator can weld without experiencing fatigue or stress. This article discusses some things to consider that can help optimize comfort and productivity and, ultimately, the profitability of the welding operation by allowing for greater arc-on time. One of the easiest and most important things welding operators can do to minimize fatigue and stress on the wrists and hands is to scale back on the amperage of the welding gun when possible. A lot of welding operators automatically use a 400 amp welding gun when a 250 or 300 amp model will do just fine for the job. Typically the higher the amperage, the larger the size of the gun handle and the more it weighs. MIG gun amperages reflect the temperatures above which the handle or the cable on the gun becomes uncomfortable. Using an underrated MIG gun for a higher amperage application can cause damage. Look at the application’s duty cycle requirements and how much of the time the welding operator actually spends welding, and consider using a lower-amperage welding gun if the job allows. Duty cycle is defined by the amount of arc-on time in a 10-minute period that the equipment can be operated at maximum capacity. Some welding guns offer 100 percent duty cycle, while others are rated 60 percent or below. In some cases, MIG guns offering 100 percent duty cycle may list a 60 percent duty cycle rating, as well. Regardless of the MIG gun manufacturer lists the rating, it is unlikely that a welding operator will be operating the gun at full amperage and full duty cycle at all times. That makes it feasible to use a lower amperage model for many applications. Often, the higher amperage rating is needed only if the welding operator is running the power source continuously. In that case, it is also important to ensure that the gun is capable of running at the higher duty cycle to avoid failures. In a shop setting, another option to gain greater comfort and productivity is using a water-cooled welding gun for GMAW applications. These guns can offer several benefits in production environments requiring extremely high heat applications. Water-cooled guns are generally smaller, lighter and easier for welding operators to manage for longer periods of time in high heat. However, they do come with more maintenance considerations and a higher price tag. GMAW gun manufacturers offer multiple handle and trigger options to increase welding operator comfort. Handles typically come in curved and straight designs, one or the other of which may be more comfortable for a given welding operator to hold and control. Some processes also may be more suited to a certain handle type, depending on what the work requires. But the choice between straight handle and curved handle often comes down to welding operator preference, so experiment to determine the preferred design. Usually, a smaller handle is easier for the welding operator to maneuver and many are available in the marketplace. Some manufacturers offer vented handles, which can be beneficial in that they cool down faster after the welding operator stops welding, so they may be slightly cooler when the gun is picked up again. Locking triggers are offered on some guns and can help alleviate “trigger finger,” which can occur from repetitive grasping and gripping of the gun trigger. When running a long, continuous weld, a locking trigger eliminates the necessity to squeeze the trigger throughout the whole weld, easing hand fatigue. Welding operators also can look for triggers that don’t have as much pull pressure or pull force required to maintain the arc. Many GMAW and flux-cored arc welding (FCAW) guns are available with rotatable and flexible necks in various lengths and angles. These options allow the welding operator to select one that best suits the joint access required for an application, and they help minimize unnecessary movement. If the weld requires a long reach or access at a tight corner, having a longer neck or an angled neck can improve comfort in that welding position. Flexible necks can be easily adjusted to fit different welding angles, and rotatable necks allow welding operators to rotate the neck as needed, making them a good option for welding out of position, including overhead. Neck couplers are tools that allow welding operators to combine two necks when a longer one is needed. A longer neck also can help the welding operator stay further away from the heat of the welding arc. Many manufacturers make custom necks, as well, but these generally cost much more than a neck coupler and take time for welding gun manufacturers to develop. If a welding operator needs a more immediate and less expensive solution, the neck coupler may be the better option. Another option to improve operator comfort are smaller, tapered nozzles. These can help the welding operator reach restricted joints, though remember that spatter build-up can be an issue since the opening to the nozzle is smaller and can become more easily clogged. All of these neck and nozzle features can help minimize a welding operator straining to reach a weld joint, which reduces the opportunity for fatigue or injury. Another accessory that can help with comfort and heat issues is a neck grip, typically high-temperature silicone rubber sleeves designed to reduce heat exposure and help the welding operator hold the neck in a steady position. They also allow the welding operator to rest the neck on his or her hand or forearm, using it as a pivot point to maneuver the GMAW gun more comfortably. When selecting power cables, choose the smallest and shortest power cable possible that can still meet the needs of an application. Smaller and shorter power cables are lighter and more flexible, making it easier to maneuver these components without excess stress on the wrists or hands. They also can minimize clutter in the workspace, prevent excessive coiling and reduce tripping hazards. Less clutter and coiling also cuts down on the chance of poor wire feeding that could cause downtime and hinder productivity. Another advantage: Smaller and shorter cables tend to be less expensive. Selecting standard-weight consumables can potentially ease forearm strain if the job does not call for heavy-duty consumables, as these are heavier. If the application calls for higher amperages, however, the welding operator may have to use the latter, as heavy-duty consumables dissipate more heat to prevent consumable damage and they can increase comfort in that manner — that is, by reducing heat stress. Weld position is another way to maximize comfort on the job. Place the workpiece flat and move it into the most comfortable position whenever possible. Maintaining a clean working environment is important. In some cases, a fume extraction gun paired with the proper portable fume extraction system can be a viable option to replace wearing a powered air purifying respirator, for example, and lessen the amount of equipment the welding operator has to wear. To maintain compliance and safety, it’s always a good idea to consult an industrial hygienist to be certain that’s an appropriate step. Having equipment that is easy to operate during the welding process is a good step in achieving a comfortable, safe work environment. Lightweight welding guns with appropriate handle and neck designs for the job and for the welding operator can help achieve safe and productive results. The reduction of heat stress, wrist and neck fatigue and repetitive motions can also help decrease overall physical and mental stress for welding operators.
When 90 percent of your business focuses on boat fabrication and repairs that require you to meet specific deadlines and codes, having the right welding equipment to manage the job isn’t just ideal, it’s essential. The welding operators and supervisors at Hike Metal Products Ltd. are no strangers to this fact. They know that the equipment they use needs to produce quality results, and it has to be easy to maintain. Downtime for weld repairs or MIG gun and consumable replacements simply isn’t an option. “We’re pretty well-known worldwide in the boat building industry for the quality of the vessels we build,” explains Frank Baptista, plant manager, Hike Metal Products. “We can relate that back to the equipment we use to make our boats.” The boats to which Baptista refers include those for the Canadian Coast Guard, the popular Maid of the Mist at Niagara Falls and police boats throughout Abu Dhabi. They have also fabricated boats for areas ranging from Florida to California and Venezuela, and recently finished an $8.5 million fireboat for the Chicago Fire Department. Hike Metal Products also tackles tough fabrication and repairs for other non-marine applications ranging from water treatment plants and oil recovery to agriculture. For the last several years, Hike Metal Products has relied on Bernard T-Gun™ Semi-Automatic Air-Cooled MIG Guns (formerly Tregaskiss TOUGH GUN™ Semi-Automatic Air-Cooled MIG Guns) and TOUGH LOCK™ Consumables to meet the quality and productivity goals on its marine applications in particular. Local welding distributor, Ron Latrielle of Praxair in Chatham, Ontario introduced the products to the company. Praxair has worked with Hike Metal Products for the last 20 years, providing their welding supervisors and operators with new solutions to help them improve their welding performance and keep their competitive edge. Also involved with Hike Metal Products and their equipment is Kevin Cole, a representative from Bernard sister company, Miller Electric Mfg. Co. Along with Latrielle, Cole introduced the company to Miller XMT® 350 Multi-Process Inverters and Suitcase RC wire feeders that they have paired with their T-Gun MIG Guns to gain greater remote access to projects. Hike Metal Products, located in Wheatley, Ontario, Canada, has been serving the boat industry since 1958, designing and fabricating ferries, research vessels and patrol boats, as well as hovercrafts and icebreakers. The commission for the recent Chicago Fire Department fireboat arose, in part, from the company’s successful completion of a similar boat for the city of Baltimore, along with the company’s industry-wide reputation for quality and punctuality. Completing such a massive project, however, was no easy task. Nor was it a leisurely one. Hike Metal Products completed the job — from the day they received the raw materials for the project until they delivered the final product — in 16 months. It’s an impressive feat when you consider the fireboat is 90 feet long and capable of pumping 14,000 gallons of water a minute. It’s among the largest boats the company has fabricated and delivered in recent years. It also has a special name: the Christopher Wheatley, named in honor of a Chicago firefighter who died in the line of duty in 2010. As with most of the company’s projects, this one required welding thick portions of mild steel (up to 3/4 inch) using flux-cored wire and relatively high amperages (up to 400 amps) — often for long periods of time. The company used 1/16-inch welding wire and completed all welds to code according to the Canadian Welding Bureau (CWB). According to Latrielle, such applications very often require a water-cooled MIG gun in order to withstand the heat; however, he was able to outfit Hike Metal Products with 400-amp air-cooled models of the T-Gun MIG Gun instead — with no problems of overheating. That’s important considering that welding operators at Hike Metal Products can weld up to 60 feet of welds in a single day. “We were really pleased that we could get away with not using a water-cooled system, which just has more parts and more things to go wrong with it,” explains Latrielle. “The air-cooled T-Gun MIG Guns have been able to handle the amperage that they are pushing and get the job done.” Baptista adds that the previous MIG guns he and his team used couldn’t boast the same durability. “Because of the heat we weld with, the triggers on our old guns just wouldn’t last. We had to change them every other week,” he says. “Now if something goes wrong with our T-Gun MIG Guns, it’s almost time to change the entire gun anyway.” In addition to their durable triggers, the T-Gun MIG Guns feature a sturdy cable strain relief on the front and back ends to prevent kinking and abrasion. This feature also helps minimize the time and cost for cable replacement. The guns have the Double-Life MIG Gun System, as well: identical connections on the front and back ends. When the front end or cable becomes worn, welding operators at Hike Metal Products can double the life of their gun by removing the trigger switch and gooseneck and flip-flopping them to the back end. The guns also feature a Lifetime Warranty on handles and switches. If either component breaks, Bernard will replace them for free. “The features on the 400-amp gun are just so durable that the guns just go and go and go,” says Baptista. “That’s good, because if you’re not fixing the gun, you’re welding, right?” Hike Metal Products Quality Manager Dave Hewstone, along with Latrielle, like too that the guns have simplified the process of searching for welding equipment and maintaining inventory. The guys (welding operators) like them and they do such a good job, I don’t have to be out there looking for another product to meet the challenges of our projects all the time. What I like is that the guns perform for my customers. They do the job. We don’t hear a lot of complaints Adding to their arsenal of welding equipment is the TOUGH LOCK Consumable System that Latrielle introduced along with the Bernard T-Gun MIG Gun. This consumable system consists of TOUGH LOCK Contact Tips and Retaining Heads with Dual Taper Technology, a second rear taper between the gooseneck and the contact tip that helps improve electrical conductivity and extend the life of the TOUGH LOCK consumables. It’s a benefit that Baptista has noticed firsthand. “With our previous consumables, we changed out our contact tips anywhere from three to four times a day,” he says. “Now, in the morning, we just get rid of the old tip and put in a new one.” These contact tips also feature a dual-lead thread design that allows the tips to be rotated 180 degrees to create a new wear position and extend the tip life even further. According to Hewstone, Hike Metal Products has enjoyed a 25 percent increase in its productivity since converting to the Bernard T-Gun MIG Gun and TOUGH LOCK Consumable System. That productivity increase has resulted from the company reducing downtime for MIG gun maintenance and consumable changeover. And, jokes Hewstone, the productivity also comes from the company’s top-secret planning and fabrication. “No, really, there are no real top secrets to our success,” Hewstone says. “Just hard work, to be honest with you.”
The Occupational Safety and Health Administration (OSHA) and other safety regulatory bodies set the allowable exposure limits for weld fumes and other particulates, including hexavalent chromium, with the aim of protecting employees against potential health hazards in the workplace. Providing welding operators with proper ventilation during the welding process is an important step companies can take to help meet the standards — and to help provide a safe and comfortable work environment. Companies may opt to invest in centralized fume extraction systems, which are designed to protect the entire shop area. These systems involve the installation of new ductwork and fans to remove fumes and are highly effective, but they are also more expensive than other options. A viable alternative for some companies is a fume extraction gun used in conjunction with a fume extraction device or localized filtration system. Fume extraction guns are available in a variety of amperages (typically 300 to 600), cable styles and handle designs. As with any welding equipment, they have their best applications, advantages and limitations, as well as recommended techniques for achieving the best results. Fume extraction guns operate by capturing the fume generated by the welding process right at the source, over and around the weld pool. The weld fumes removed by these guns are composed of a combination of the filler metal and base material. Various manufacturers have proprietary means of constructing guns to conduct this action, but at a basic level they all operate similarly: by mass flow, or the movement of material. A vacuum chamber suctions the fumes through the handle of the gun, into the gun’s hose and through to a port on the filtration system (sometimes informally referred to as a vacuum box). Typically, fume extraction guns are larger than regular welding guns, and include the vacuum and hose that are necessary to extract the fumes. Some manufacturers offer fume extraction guns with a vacuum hose swivel on the rear of the handle to make them easier to maneuver. Also, design advancements have minimized the handle weight and size to make the guns as light as possible for operator comfort, while still offering consistent fume extraction benefits. Fume extraction guns are especially well-suited for applications using solid welding wire and for those in confined spaces, where the goal is to capture fumes immediately at the source, in the welding operator’s breathing zone. Industries where these applications often occur include shipbuilding and heavy equipment manufacturing, as well as general manufacturing and fabrication applications utilizing mild or carbon steel. Petrochemical or other applications where stainless steel welding and greater hexavalent chromium levels are prominent may also present the opportunity to use a fume extraction gun. The guns work well on high amperage and high deposition rate applications. For the best results, fume extraction guns should be used for in-position welding, such as on flat butt welds. In this position, they can most effectively capture fume particles as they rise from the weld pool. It’s more difficult for a fume extraction gun to draw fume particles downward and through the vacuum hose in out-of-position welds, because the fume particles rise at a high rate in those cases. Techniques to maximize performance?The operation of fume extraction guns is similar to that of standard MIG guns, with many of the same recommended best practices. However, there are some techniques that welding operators can follow to help get the best performance from a fume extraction gun. Here are some things to remember: Perhaps the most important tip for maximizing performance is using the appropriate degree of angle. With solid wire — the most common filler metal used with fume extraction guns — use a push technique and an angle of 0 to 15 degrees, which is optimal for fume capture. For flux-cored wire (which generates more fume), use a drag technique with a 0 to 15-degree angle. If the parts are set up at a 0 to 30-degree angle and the gun is kept straight (vertical) during the welding process, the fume rises, allowing the fume extraction of the gun to be maximized. Travel speed during either of these welding processes will typically be dictated by the base metal and the wire size used. Because flux-cored wire produces a slag, it generates more weld fume. However, one benefit of using self-shielded flux-cored wire, for example, is it allows the ability to increase the vacuum level of the gun. Welding operators can close off all the vents and extend the shroud as far as possible. This action maximizes the vacuum at the front end of the gun without concern for disturbing the shielding gas, since there is none generates with self-shielded flux-cored wire. When using gas-shielded flux-cored wire, a 0 to 15-degree angle will help maximize fume collection. At the end of the weld, welding operators can pause for 10 to 15 seconds, holding the fume extraction gun in place without depositing weld metal. This action allows the gun to capture residual fumes as the weld bead is cooling. The contact tip to work distance can be longer — about 1/2 inch to 3/4 inch — when welding with flux-cored wire and a fume extraction gun. With solid wire, welding operators should try to keep the stickout to 1/2 inch or less to maximize fume capture. These lengths are comparable to the stickout lengths used with standard MIG guns. Some fume extraction guns feature adjustable extraction control regulators at the front of the gun handle, while other guns include this function internally. These regulators allow welding operators to increase suction as needed without affecting shielding gas coverage. The ability to balance between the downward flow of shielding gas and the upward flow of the suctioned air is important. Fume extraction guns need to provide the appropriate amount of shielding gas to protect the weld from defects such as porosity without sacrificing the ability to suction fumes efficiently enough to protect the welding operator. Adjusting the air control regulator to the appropriate level can be a matter of trial and error, so welding operators may want to test it on scrap material to optimize the suction rate before welding on a product. As with any piece of welding equipment, fume extraction guns benefit from preventive maintenance. Caring for them is similar to caring for a standard MIG gun. Also note that using flux-cored wire with these guns requires more frequent gun maintenance than solid wire because of the slag and fumes it generates. Regular maintenance is important to help prevent a clog or spatter buildup, which can limit the fume capture rate. Inspecting and maintaining the front end of the gun is key to optimizing fume extraction. Frequently inspect the nozzle and contact tip for signs of spatter buildup, which along with blocking the fume extraction can also obstruct shielding gas flow and cause weld defects. Spatter buildup also can cause consumables to fail prematurely. Replace the consumables if spatter buildup appears, or clean them according to the manufacturer’s recommendations. Also, inspect the vacuum hose regularly for damage such as cuts or kinks, which can lead to loss of suction. Replace a damaged vacuum hose as necessary. Regarding consumables, using the manufacturer’s recommended consumables package with a fume extraction gun helps optimize performance, as the guns are engineered to get the best results with specific consumables. When in doubt about maintenance or any other aspect of using a fume extraction gun, consider working with a trusted welding distributor, certified industrial hygienist and/or the gun manufacturer to address any questions or concerns. In combination with many other variables in the welding operation — wire selection, specific transfer methods and welding processes, welding operator technique, and base material selection — fume extraction guns can help companies maintain compliance with safety regulations and create a cleaner, more comfortable welding environment. Proper use and maintenance of the equipment is important to get optimal results.
When your company is responsible for rebuilding, repairing and up-fitting vehicles that deploy to firefighting and rescue situations day in and day out, quality is non-negotiable. Every component must be precisely tooled, every weld precisely placed. The employees at True North Emergency Equipment can certainly attest to that fact. They are a premier service provider for custom fire engines, water tenders, and rescue and emergency vehicles used across the United States, and especially in the Northwest. “Our people understand and believe that our vehicles need to be serviced to complete their mission. They are lifesaving vehicles,” explains Russ Sheldon, operations manager at True North Emergency Equipment. “We don’t just inspect quality into our products. It has to be built in there.” That philosophy spans every aspect of the Hillsboro, Ore.-based company. According to Sheldon, almost every vehicle the company works on is unique, which means it requires the right equipment to work on it – regardless if the job is rebuilt, repaired or upfitted. Recently, True North Emergency Equipment added new MIG welding guns and consumables from Bernard to their welding operation. They found that the products didn’t just stand up to the tough demands of their applications, but that the MIG guns also proved more versatile and comfortable for the welding operators. Plus, the consumables helped reduce their inventory and costs. Not surprisingly, these are benefits that the fabricators and management alike welcomed. In a typical day at True North Emergency Equipment, there are no typical applications. The company could be welding 1/8-inch-thick sheet metal compartments or working on 1/2-inch steel mounting brackets. Most days, fabricators also tackle the nuances of aluminum welding for good measure. Adding to the challenge of welding multiple materials, these same fabricators also find themselves working at awkward angles on a regular basis. According to Sheldon, “Fabricators here weld overhead, vertical and horizontal, and a lot of the components we fixture. So to say we have a standard welding position or a set position … no, that would not be the norm here.” Despite those challenges, the welds have to look, in Sheldon’s words, “sharp.” “Anything exposed has to look top notch. The care in the detail basically has our fabricators’ artistic signature on it,” he adds. Kyle Plock, a True North Emergency Equipment fabricator, has noticed that the company’s new Bernard Q-Gun™ (400 amp) series MIG guns help make that quality easier to achieve — even on out-of-position welds. The gun features a rotatable neck that users can change the position of without any tools. They simply unscrew the durable plastic ring at the base of the neck, rotate the neck to the desired angle and tighten the ring. “With the Q-Gun MIG gun, all you have to do is loosen the neck, turn it and tighten it back up where you want it,” says Plock. “With the old guns, we had to get an Allen wrench, loosen the socket head cap screws, then turn the neck and tighten it back up. So this [gun] is a lot quicker and easier.” Plock adds that this feature comes in handy especially when he’s working on an application that doesn’t allow him a lot of room to maneuver or reach for tools (as would be needed to change neck angles on the older style guns True North Emergency Equipment used). “If we’re inside of a truck in the pump house welding a structure, I often have to turn from one direction to another,” he explains. “If I want this neck to go a different way to fit in a tighter spot, I can turn it without having to twist my hands around.” The addition of a dual schedule switch on the Bernard Q-Gun series MIG guns that the company uses adds to its versatility for fabricators like Plock and the other fabricators. The dual schedule switch allows them to change wire feed settings (without having to go back to the power source) when they alternate between welding thinner and thicker materials. “Personally, I like that if I’m at the top of a truck and need to make an adjustment [to the wire feed speed], I don’t have to climb all the way down to the machine, make the adjustment and then climb all the way back to where we were working,” says Plock. “With this setup here, we don’t have to do that. I just make my adjustment and keep on going. It’s a lot more efficient.” Mitch James, plant manager and field trainer for True North Emergency Equipment agrees that these features and the versatility that his team gets from the new MIG guns is an asset. “The features have made a big difference in comfort and in improving throughput time. There’s just no messing around and adjustment with them,” James explains. True North Emergency Equipment paired its new Bernard Q-Gun series MIG guns with the Centerfire™ consumables system, also from Bernard. These consumables feature a “drop-in,” threadless contact tip that fabricators can change back quickly after a burnback to help reduce downtime and get them back to work faster. The contact tips also have a large diameter tip base and tapered seat that, combined with the gas diffuser, provides better electrical conductivity and heat transfer. For True North Emergency Equipment, those features translate to one single benefit: The consumables last longer than their previous brand. “There was a time when we would have to buy our welding tips 25 or 50 in a bag,” says James. “I actually had team members come to me [before Centerfire] and say they were running through three, four, five, six, eight tips in a matter of just a few hours from burnbacks and such things.” Since the conversion to the Centerfire consumables system, James says that their consumable usage has dropped tremendously. “We don’t have to stock nearly as much anymore. We’re stocking about 75 percent less or about 25 percent of what we used to stock in consumables,” he explains. “That’s saving us quite a bit of money.” It’s all about quality at True North Emergency Equipment — and quality is what keeps the company’s customers and employees happy. The fabricators and management all take pride in knowing that they are helping rebuild, repair and refurbish the best, safest and most durable fire and rescue vehicles for their customers. “Every customer has exacting spec and we suit that need. That’s our niche. That’s who we are,” says Sheldon. “And cater to the high end of the market — always.” That the company has found the right tools to help its employees reach that goal isn’t lost on them, says James. “In the end, it’s all about attitude; emotions; how people feel about what they’re doing. If you feel good, you’re going to do good. So that’s the whole ball of wax right there.”
Your welding operation, just like any other portion of your business, offers opportunities to conserve resources. Consider these 10 money-saving tips for MIG gun care and maintenance as a good first step. And don’t be surprised when you find these tips improve your welding performance along the way! Keep your nozzles, gas diffusers and contact tips in the original package in which they were shipped until you are ready to use them. Doing so prevents scratches and/or dents where spatter can accumulate and cause the consumables to fail prematurely. It also prevents dirt, oil or other debris from adhering to the consumables and inadvertently entering the weld puddle. Remember, proper storage and handling doesn’t just lower your actual costs for consumables, it can also prevent weld defects that require costly rework. Choose the most appropriate neck for your MIG welding application in order to increase comfort and control, and save money. Rotatable necks, for example, adjust without tools so that you can quickly change neck angles by loosening a plastic ring and tightening it once you’ve determined your desired position. These types of necks are especially useful if you find yourself welding on many different applications and angles throughout the day, and they minimize costs for inventory and changeover. For hard-to-reach areas, you may also want to consider a neck coupler, which allows you to connect two existing necks together to extend your reach — again without the cost of purchasing a new or specialized neck. Flex necks are also a good option for saving money, and gaining greater comfort and control, particularly for applications with tighter joints. You can bend these necks to multiple angles to work around corners or get into small spaces without the expense of stocking different neck angles. Regularly perform a visual inspection of your nozzle — inside and outside — to look for spatter build-up. If there is accumulation, either clean the nozzle with a tool designed specifically for the job or replace the nozzle if necessary. During your inspection, also check that the nozzle, contact tip and retaining head are tightened properly, as these components can naturally loosen during welding. Inspecting and tightening your consumables regularly (several times during a welding shift is ideal) help ensure good shielding gas coverage, reliable electrical conductivity and consistent weld quality. Always trim your MIG gun liner according to the manufacturer’s recommendations, using the proper tools and cutting it to the correct length. Too long of a liner can cause kinking, while cutting it too short allows debris to build up between the liner and the gas diffuser. Either way, the wrong liner length can cause poor wire feeding and premature failure of both the liner and the contact tip. When possible, use a liner gauge to determine the proper length for your particular liner and be certain that there are no burrs or sharp edges after you cut it. Also, keep the liner away from contaminants (e.g., don’t let it drag on the floor) during installation and be sure your hands or gloves are clean. These precautions help prevent contaminants from entering the weld puddle and causing costly weld quality issues. Consider using a front-loading MIG gun liner to ease and speed liner replacement. This type of liner cuts installation time nearly in half compared to using a rear-loading liner, saving you downtime and unnecessary labor costs for changeover. Some manufacturers offer a spring-loaded module that works in conjunction with a front-load liner to help minimize issues if you accidentally trim the liner to an incorrect length. These modules are housed in the power pin and put forward pressure on the liner after installing it from the front of the gun. The modules allow up to 1 inch of forgiveness if the liner is too short. There are also jump liners available. These replace only the most commonly worn and clogged liner area — from the neck to the contact tip — to reduce the amount of time a gun is offline and minimize inventory for full-length liners. These jump liners enable quick and easy neck change-out so the MIG gun can be easily adapted to fit multiple applications. When appropriate, switching from heavy-duty contact tips to standard-duty ones can help lower your overall consumable costs, while still providing you with reliable welding performance. If you have lower heat applications, brief arc-on times for short welds or tacks, or if you are using mixed shielding gases and small diameter wires, standard-duty contact tips may be a better option and they cost less. You can also use these types of contact tips if you have applications with restricted access, as the smaller outside diameter can help increase gas coverage and reduce the nozzle’s bore size, making it easier to reach tough joints. Look for non-threaded contact tips that connect or seat securely with the gas diffuser. This type of design provides consistent electrical conductivity and helps dissipate heat more readily. That’s important, since cooler running consumables last longer and provide more consistent performance. A nozzle with a thread-on design helps keep the contact tip centered for better weld placement and it can minimize the opportunity for spatter. This type of design can also withstand demanding jobsite use and abuse. As an additional defense against spatter accumulation, purchase nozzles that have a smooth, non-porous surface. Be sure that the nozzles are free of any sharp edges or flat spots that would further allow spatter to adhere. As when handling the liner, be sure you have clean hands or gloves when you are handling or installing your nozzle. Dirt, oil, grease or other debris can easily adhere to nozzles and later enter the weld puddle, causing weld defects. These contaminants can also cause premature failure of the component. Use the shortest length MIG gun cable possible for your welding application, as it helps prevent kinking and premature wear of both the cable and the MIG gun liner. It also helps prevent wire-feeding problems that could lead to an erratic arc, poor weld quality and unnecessary downtime for rework or consumable replacement. Steel monocoil cables are also an excellent means to prevent kinking. Also, remember to choose the correct diameter liner and contact tip for your welding wire, as this prevents similar problems and helps extend the life of these consumables. Whenever possible, purchase MIG guns and consumables that are backed by a reliable manufacturer’s warranty, and use all guns and consumables as intended so as not to void the terms and conditions. Also, consider the up-front cost versus the long-term savings of purchasing sturdier and more expensive consumables. They will likely last longer, reducing downtime associated with changeover and the cost of the consumables themselves. Keep these tips in mind and you can get back to welding faster… and keep conserving your resources.
New industry standards from the Occupational Safety and Health Administration (OSHA) and other safety regulatory bodies have been developed in recent years with one specific objective in mind: to help protect employees against potential health hazards in the workplace. These regulations, which dictate allowable exposure limits of welding fumes and other particulates (including hexavalent chromium), have led many companies to invest in fume extraction equipment. An increased desire to maintain optimal welding operator safety and to attract new skilled welding operators to the field is also a consideration in investing in this equipment — companies want to create the most comfortable and healthy work environment possible. Some companies may opt for centralized fume extraction systems, which are designed to protect the entire shop area. These systems involve the installation of new ductwork Fume extraction guns are available in a variety of amperages, cable styles and handle designs. As with any welding equipment, they have their advantages and limitations, best applications, maintenance requirements and more. In combination with many other variables in the welding operation — welding wire selection, specific transfer methods and welding processes, welding operator behavior and base material selection — fume extraction guns can help companies maintain compliance with safety regulations and create a cleaner, more comfortable welding environment. Fume extraction guns operate by capturing the fume generated by the welding process right at the source, over and around the weld pool. Various manufacturers have proprietary means of constructing guns to conduct this action, but at a basic level they all operate similarly: by mass flow, or the movement of material. This movement occurs by way of a vacuum chamber that suctions the fumes through the handle of the gun, into the gun’s hose through to a port on the filtration system (sometimes informally referred to as a vacuum box). The welding fumes that these guns remove are composed of a combination of the filler metal and base material.Some fume extraction guns feature adjustable extraction control regulators at the front of the gun handle, which allow welding operators to increase suction as needed (without affecting shielding gas coverage), while others provide this function internally. Regardless of the manner, the ability to balance between the downward flow of shielding gas and the upward flow of the suctioned air is critical. The fume extraction gun needs to provide the appropriate amount of shielding gas to protect the weld from defects such as porosity, without sacrificing the ability to suction fumes efficiently enough to protect the welding operator. The balance allows the weld pool time to react and solidify, and gives the fume particles time to decelerate so they are easier to extract. Typically, fume extraction guns are larger than regular welding guns and tend to be bulky due to the vacuum and hose necessary to extract the fumes. For that reason, some manufacturers create fume extraction guns with a vacuum hose swivel on the rear of the handle to make them easier to maneuver. Manufacturers have also, since fume extraction guns were first introduced (in the late 1960s and early 1970s), found ways to engineer internal components to minimize the handle weight in order to reduce operator fatigue. Fume extraction guns are well-suited for applications using solid welding wire and those in confined spaces. These include, but are not limited to applications in the shipbuilding and heavy equipment manufacturing industries, as well as general manufacturing and fabrication. They are also ideal for welding on stainless steel applications, as this material generates greater levels of hexavalent chromium, and on mild and carbon steel applications. The guns also work well on high amperage and high deposition rate applications and are available, typically, in 300 to 600 amp ranges. For the best results, fume extraction guns should be used for in-position welding, such as on flat butt welds. In this position, they can most effectively capture fume particles as they rise from the weld pool. In out-of-position welds, the energy of the fume particles causes them to rise at a high rate, making it more difficult for the fume extraction gun to draw them downward and through the vacuum hose. One distinct advantage to fume extraction guns is that they remove the fumes at the source, minimizing the amount that enters the welding operator’s immediate breathing zone. However, because welding operators typically move the gun away from the weld pool after completing a pass, the fume extraction gun is not as able to control residual fume as well as a fume extraction hood can. As with any piece of welding equipment, fume extraction guns benefit from preventive maintenance. Caring for them is similar to caring for a standard GMAW gun. Regularly check for tight connections throughout the length of the fume extraction gun to ensure good electrical flow. Minimizing electrical resistance helps ensure consistent weld quality and prevent premature failure of the front-end consumables — contact tip, nozzle and diffuser. Frequently inspect the nozzle and contact tip for signs of spatter build-up, too, as such build-up can obstruct shielding gas flow and cause weld defects that ultimately will need to be reworked. Spatter build-up can also cause consumables to fail prematurely. Replace the consumables if spatter build-up appears or clean them according to the manufacturer’s recommendation. In some cases the shroud that surrounds the nozzle may also have to be replaced or cleaned free of spatter. To ensure optimal fume extraction capabilities, inspect the vacuum hose regularly for damage, including cuts or kinks that could lead to loss of suction. Replace a damaged vacuum hose as necessary and dispose of it according to the manufacturer’s and/or an industrial hygienist’s directions. Visually inspect the handle for cracks or missing screws, and also check that the gun’s trigger is not sticking or otherwise malfunctioning. Replace or repair these components as necessary. Finally, maintenance on the liner is also important. As with the vacuum hose, use compressed air to clear out any potential blockages during welding wire changeovers or when removing the wire from the gun. Spending an extra few minutes clearing out any debris from the liner can save considerably more time than troubleshooting the weld defects and equipment problems that can result from blockages. Also, track the amount of time that it takes for a liner to wear during the course of the welding operation. Replace the liner prior to that in the future to prevent downtime for replacement during shifts or problems with wire feeding or quality. When in doubt about maintenance or any other aspect of using a fume extraction gun, consider working with a trusted welding distributor, certified industrial hygienist and/or the fume extraction gun manufacturer to address any questions or concerns. Proper use of this equipment can help provide optimal results, and improve the safety and comfort of the welding environment.
The term “ergonomics” has become increasingly common in the workplace as companies strive to improve safety and efficiency among employees — whether in the office or on the plant floor. At its most basic level, ergonomics refers to the discipline or science of designing equipment and arranging the work environment for optimal worker comfort and productivity. Minimizing fatigue, reducing repetitive motion, and decreasing overall physical and mental stress are some of the key factors at the heart of it. For welding operators who spend their time maneuvering around difficult weld joints with a MIG, flux-cored or fume extraction welding gun and facing a hot arc, the term takes on an especially important meaning. A welding gun’s handle, neck and power cable design can significantly impact the duration of time a welding operator can weld without experiencing fatigue or stress. So too can the heat generated in the process. Excessive heat, just like musculoskeletal strain, can contribute negatively to the welding operator’s health and efficiency. In the long run, choosing a welding gun that offers greater comfort and operates at a cooler temperature can help increase productivity and, ultimately, the profitability of the welding operation by allowing for greater arc-on time. When welding, the first factor in good ergonomics is to select a welding gun with the appropriate handle design. Typically, manufacturers offer handles in curved and straight designs, one or the other of which may be more comfortable for a given welding operator to hold and control. The preference is individual and a welding operator may need to experiment to determine which design best suits him or her. If possible, a welding operator may want to consider using a slightly lower-amperage welding gun to gain greater comfort and minimize fatigue and/or stress on the wrists and hands. Typically, as a welding gun’s amperage decreases, so too does the size of the gun handle, which makes the equipment lighter and easier to maneuver for longer periods of time. It is important, however, that in selecting a smaller and lighter-weight handle, the welding operator still has a gun that meets the application’s amperage and duty cycle requirements. Duty cycle is defined by the amount of arc-on time in a 10-minute period that the equipment can be operated at maximum capacity. Some welding guns will offer 100 percent duty cycle, while others are rated 60 percent or below. In many cases, a welding gun rated at 300 amps, for example, may suffice for a 400-amp application considering that welding operators rarely weld continuously enough to exceed the gun’s duty cycle. In a shop setting, another option to gain greater comfort and productivity would be to convert to a water-cooled welding gun for MIG applications, as these guns are generally smaller, lighter and easier for welding operators to manage for longer periods of time. Smaller, shorter and lighter power cables offer greater flexibility to welding operators, making it easier to maneuver the equipment without excess stress on the wrists or hands. A good rule of thumb is to select the smallest and shortest power cable possible that can still meet the needs of the application. Smaller, shorter power cables can also minimize clutter in the weld cell by preventing excessive coiling and minimizing tripping hazards. Less clutter and coiling also reduces the chance of poor wire feeding that could cause downtime and hinder productivity. On fume extraction guns, look for vacuum hose swivel on rear of handle, as this feature improves flexibility and reduces welding operator fatigue. Many MIG and flux-cored guns are available with rotatable and flexible necks in various lengths and angles. These types of necks allow the welding operator to select one that will best suit the joint access required for an application. For example, rotatable necks are a good option for welding out of position, even overhead. They do not require the welding operator to change the welding gun handle or position, so he or she can hold the gun in a way that is most comfortable, while also gaining access to the weld joint. Similarly, flexible necks can be easily adjusted to fit different welding angles and reach difficult joints that may be restricted or otherwise awkward to reach. This feature also helps minimize straining to reach a particular weld joint, and with it reduces the opportunity for fatigue or injury. Some welding gun manufacturers also offer neck couplers. These accessories allow the welding operator to connect multiple necks together to reach especially difficult joints more comfortably. Increasing productivity in a welding operation by way of improved ergonomics is a matter of more than just having lightweight, easy-to-control equipment. It’s also a matter of minimizing heat stress in the work environment. When welding materials such as aluminum or stainless steel, there is an opportunity for greater radiant heat — heat that reflects from the welding arc and base metal back to the handle. Welding operators can use a longer neck on the welding gun to place the handle further back from the arc when welding on such applications. Also, the addition of a neck grip on a MIG gun can protect the welding operator from heat exposure and related fatigue. These high-temperature silicon rubber grips slide over the neck and offer the added benefit of increased control. They allow welding operators to rest the neck on their hand or forearm, using it as a pivot point to maneuver the MIG gun more comfortably. In the end, having equipment that is easy to operate during the welding process is the first step in achieving good ergonomics, a safe work environment and greater productivity. After all, a more comfortable welding operator is a more content one. And more content employees can help companies generate greater throughput on a day-to-day basis. Start the process by finding welding guns that are lightweight, offer an appropriate handle and neck design, and feature the right neck and power cable for the job and for the welding operator.
Rapid growth is a problem many companies would love to have. Those that experience it, however, must properly manage that growth in order to maintain profitability and avoid the potential pitfalls of taking on more work than they are equipped to handle. Communications systems, training protocols, material flow and inventory management are just a few of the areas that Miller Welding and Machine Co., Brookville, Penn., has refined over the last 1 1/2 years as its workforce nearly doubled and it expanded from one to three manufacturing facilities. As a subassembly fabricator for top-tier OEM manufacturers of cranes, aerial work platforms, mining and other heavy equipment, Miller produces dozens of different components across 140 semi-automatic welding cells and 10 robotic cells. From an inventory management perspective, fabricating and welding such a wide variety of products has required Miller to standardize their applications as much as possible on the same tools and equipment. Minimizing operator downtime and maintenance costs has also been essential to managing their rapid growth. Miller addressed all of those challenges with the help of Bernard Centerfire™ consumables and Q-Gun™ MIG guns. Centerfire consumables have reduced operator downtime and allowed the company to standardize all of its welding guns, regardless of brand, on one set of consumables. Bernard’s Q-Gun line of MIG guns also has reduced operator downtime and lowered the company’s maintenance costs through a combination of durability and time saving technology. Founded in 1962 as a small welding and machining shop serving the needs of the Pennsylvania steel industry, Miller Welding and Machine has grown into a major component fabricator with nearly 500 employees and state-of-the-art manufacturing facilities. “Taking advantage of technological advances has been one of the keys to our success,” explains Dave Miller Sr. “Not long after I started the business, a welding distributor told me about a new technology called wire welding. It seemed to be a natural fit for some large welds we were doing, so we jumped into the wire feeding business and never looked back.” Today, Miller’s son, Dave Miller Jr., serves as company president and continues his father’s tradition of using technology to achieve process and product improvements. One of the technologies heralded by Dave Miller Jr. has been the addition of vending machine-style inventory management systems from which nearly all of the company’s consumables are distributed. The use of these systems, combined with standardizing the company’s operations on Centerfire consumables, has reduced inventory costs and simplified the company’s inventory control procedures. The vending system requires employees to enter a unique employee number and then the part number of the consumable they need. The machine then records the information and dispenses the products. Miller uses nine of these vending machines throughout its three plants, each of which is linked in to a mainframe computer that tracks nearly all of its consumable products, including fasteners, batteries, grinding wheels and more. To further simplify the stocking, tracking and ordering system, Miller also sought to reduce as much as possible the number of welding consumables they carried. Bernard’s Centerfire consumables fit perfectly with this goal. Because Centerfire consumables — diffusers, contact tips and nozzles — are able to be installed on most major brands of MIG guns through the use of conversion parts, Miller was able to stock one set of welding consumables in the vending systems for the three different brands of MIG guns used throughout the plant. Standardizing on one brand of welding consumables has reduced the potential for operators to select the wrong consumable for their gun, simplified the purchasing department’s inventory tracking and ordering processes and reduced the amount of space that their welding consumables consumed in the vending system by 66 percent. “It keeps everything simple,” explained Production Manager Dave Moore. “We’re in the welding and fabrication business, not inventory management, so anything we can do to reduce the amount of time and money spent managing our welding consumables inventory is time and money we can devote to our core competencies.” The key to managing Miller’s growth has been the Centerfire system’s unique design, which has reduced operator downtime, increased consumable service life and offered excellent weld quality and consistency. The Centerfire system features non-threaded contact tips that fit securely in the diffuser and lock into place without the use of tools. This allows operators to change contact tips in about half the time it takes to change out a threaded tip. At an average of 1 minute per tip change, and 2.5 tip changes per welding cell per month, Miller saves roughly six man-hours each month just in the time it takes to change the contact tips. The Centefire system further reduces operator downtime by requiring fewer changeovers. Miller averages over 240 man-hours per contact tip, compared to most brands, which need to be changed an average of every 24 – 48 man hours. “At one of our facilities we have about 80 arcs running two 10-hour shifts plus an eight-hour shift on Saturdays. They weld material anywhere from 1/4-in. — 2-in. and they put down over 30,000 pounds of wire a month. For all that, they usually go through about 200 contact tips per month,” Moore said, “so we’re very satisfied with the performance and durability of the Centerfire tips.” Like all of its equipment and tools, Miller’s use of Bernard Q-Guns is a decision based on what works rather than brand loyalty. The company initially received the guns as part of a package with their wire feeder purchases, so, as Moore puts it, “we weren’t about to throw them in the trash and put something else on.” If the Q-Guns hadn’t performed up to the company’s standards, however, “we’d have run them until they died, trashed them and replaced them with something else,” Moore said. But they did perform well, and the company has converted nearly all of its hand-held MIG welding to Bernard Q-Guns. The company has been very satisfied with a different brand of guns for its robotic applications, and there are still a few hand-held guns of a third brand that are still in service, but will be replaced with Q-Guns once they wear out. “These guns have been very cost effective for us,” Moore said. “They hold up well, the repair and replacement costs are very reasonable and they offer a wide variety of configurations, so we can get the exact gun that we need for all of our applications.” Miller uses 400-amp Q-Guns with a short neck angled at 45 degrees and mostly 15-foot cables, which the company is able to customize 24 hours a day through Bernard’s online Configurator. The Configurator can then be used to order the customized gun through the company’s preferred welding distributor. They also take advantage of the available Bernard Jumpliner™, which allows operators to reduce the time it takes to replace a worn liner from an average of about 20 minutes down to around 90-seconds. The Jumpliner is a replacement liner that allows operators to only replace the most frequently worn out portion of the liner — the section leading from the consumables back through to the gun’s handle — rather than replacing then entire liner when only a small section is worn out. Just as importantly, Miller encountered virtually no resistance from its welders. “There wasn’t really an adjustment period in getting used to the new guns,” Turntable Welder Brody Speer said. “The guns are lighter and more maneuverable than other products we’ve used, so they were well received right from the start.” With a welding system in place that allows Miller Welding and Machine to handle nearly any type of welding job without changing the guns, consumables, wire or processes they use, the company has used technological advancements to position itself to manage the growth they’ve already experienced, and also to continue growing into the future.
Time spent maintaining a MIG gun can be considered downtime, but that doesn’t mean it is time wasted. Proper gun maintenance can substantially extend the service life of the equipment and reduce the even greater cost of weld rework. Diagnosing and correcting minor problems, such as loose connections, can avert more serious equipment failures and weld defects. Below are some recommended maintenance tips for most brands of MIG guns. Always follow the gun manufacturers recommended safety precautions, including disconnecting the gun from the feeder and allowing it to cool before performing any maintenance that could expose live electrical circuits. Feeder Connection – A loose or dirty wire feeder connection often causes electrical resistance and heat to build up at the point of the connection, leading to drops in voltage, an erratic arc and premature equipment failure. You should manually check the connection on a weekly basis or whenever you install the gun to the feeder to ensure that it is clean and fits tightly to the wire feeder. If the connection is loose and cannot be tightened according to the manufacturer’s specifications, it is best to replace the direct plug with one that fits securely. Clean a dirty direct plug as needed with electrical contact cleaner. Another area of the feeder connection that can fail are the O-rings that provide an airtight seal through which the shielding gas enters the cable hose. These O-rings can become dry and crack over time, and they can also be cut or damaged when the gun is installed. Gas leaks caused by faulty O-rings can cause porosity, excessive spatter and create other defects that require rework and waste gas. They should be checked and coated with a silicone lubricant whenever the gun is removed from the feeder. Cable – The cable is usually the only part of the MIG gun that requires full gun replacement when it becomes damaged. For that reason, cable maintenance is very important to avoiding unnecessary equipment costs. Gun cables should be visually inspected on a daily basis for cuts, kinks and other damage. Cuts in the cable could expose the internal copper wiring and create a potential safety hazard. The cable should also be routed from the feeder to the welding location as straight as possible. Severe bends in the cable can obstruct the gas flow and wire feeding, leading to porosity, an erratic arc and other weld deformities that take valuable time to remedy. Liner – The liner is often both the most difficult part of the gun to inspect and maintain, and one of the most frequent sources of weld troubles. Fragments of the welding wire often chip off and accumulate as it travels through the liner. Over time, these accumulations can cause poor wire feeding, birdnesting and burnback. These problems can also occur if the liner becomes kinked or if the cable is bent at too much of an angle. Removing the liner for a full inspection and cleaning it is time consuming and unnecessary if there aren’t any existing problems. Instead, to maintain an unclogged liner, use compressed air to clear out any potential blockages during wire changeovers or whenever you remove the wire from the gun. Spending an extra few minutes clearing out any debris from the liner can save considerably more time than troubleshooting the weld defects and equipment problems that can result from blockages. Handle and Trigger – The handle and trigger generally require very little maintenance beyond visual inspection. Check that there are no missing screws or damage to the handle and test the trigger to make sure it is not sticking or otherwise malfunctioning. These inspections take only seconds and should be done every time you use the gun. A damaged handle runs the risk of causing electrical shock if there is any exposed copper from the weld cable. A dirty, damaged or simply worn out trigger can cause a number of weld problems and should be replaced with a new trigger. Neck – The neck carries the electrical current from the welding cable to the consumables. Loose connections at either end of it can cause poor electrical conductivity, which can lead to weld defects and further equipment failures due to the heat generated by electrical resistance. Check to ensure tight neck connections on a daily basis. MIG gun necks also feature external insulators that protect the electrically live components from being exposed. Exposed electrical components near the handle can create a safety risk, and exposed components near the consumables could arc to the work piece and damage both the gun and the work piece. The insulators should be checked on at least a weekly basis and replaced as needed. Consumables – Because of their exposure to heat, spatter and general abuse, the consumables require frequent replacement. That doesn’t mean, however, that you can’t save time and money through some simple maintenance. In addition to providing gas flow to the weld pool, the gas diffuser connects to the neck and carries the electrical current to the contact tip. Loose connections between the diffuser and the neck or the diffuser and the contact tip can cause gas leaks or weld quality and equipment problems related to poor conductivity and built up electrical resistance. These should be checked during nozzle changes and tightened to the manufacturer’s specifications using the recommended tools. Most diffusers also use O-rings to seal in the shielding gas, and like their counterparts at the back end of the gun, you should check these for cracks, cuts or other damage and replace them as necessary whenever you remove the nozzle. The nozzle’s main role is to focus the shielding gas around the weld pool. Spatter can build up inside the nozzle and obstruct the gas flow, resulting in porosity, excessive spatter and other problems related to inadequate shielding gas coverage. The nozzle and nozzle insulator can also become damaged from cleaning out the built-up spatter. Depending on the amount of spatter created while welding, you should check and clean the nozzle several times per day. A pair of welding pliers is the most common tool for cleaning nozzles, but there are other specialized tools designed specifically for reaming out spatter from the nozzles. The nozzle insulator keeps the copper or brass nozzle body separate from the electrically live consumable components, so a damaged insulator could cause the nozzle to arc to the workpiece. A visual inspection of the nozzle insulator is usually sufficient to determine proper condition, and damaged insulators require replacing the entire nozzle. The contact tip is the final piece of the consumables set, and the last point of contact between the welding equipment and the welding wire. As the wire passes through the contact tip, it can erode the inside of the tip bore, leading to interruptions in the electrical current and poor arc control. The tip can also become covered with spatter and cause inadequate gas coverage. Welding operators often wait to change the contact tip until a weld problem develops, however, the time it takes to correct a weld problem can be considerably greater than the time it takes to visually inspect and replace the contact tip on a regular basis as a standard maintenance procedure. Industrial grade welding equipment is built with productivity in mind, but even the best equipment will eventually breakdown. Whether you catch the equipment malfunction in its early stages or after serious problems develop is up to you, however. Through the implementation of the simple, proactive maintenance steps outlined above, you can greatly extend the service life of your equipment and avoid the costly correction of weld defects in the event of equipment breakdown.
When it comes choosing welding equipment, welding operators may find themselves first and foremost contemplating which power source to use. And rightly so. The power source has a significant impact on weld quality, productivity and the overall cost of the welding operation. But having the right semi-automatic MIG gun for the job is equally important. From short arc-on times for tacking parts to completing long continuous welds on thick plate, the MIG gun needs to offer the appropriate welding capacity for the job. For example, welding operators may not need a MIG gun that is the same amperage as the power source. That is because often they weld only 30 to 50 percent of the time, making the use of a lower amperage gun an appropriate option. Conversely, when welding operators overwork a light-duty MIG gun it could lead to premature failure. Or, in some cases, the welding operation may have multiple applications, making it necessary to have a MIG gun that can address the needs of several applications within one facility. For welding applications that require short arc-on times, such as tacking parts or completing welds on small parts, a light-duty MIG gun may be the best choice. A light-duty MIG gun is typically considered one that provides from 100 to 300 amps of welding capacity. Like all MIG guns, light-duty ones are rated according to their duty cycle, or the number of minutes in a 10-minute period that the gun can be operated at its full capacity without overheating. Generally, MIG gun manufacturers rate their products at 60 to 100-percent duty cycle. In the case of light-duty applications, including welding sheet metal, general hobbyist projects, or auto repair and auto body applications, a light-duty MIG gun would work well. Because light-duty MIG guns typically offer low amperage capacity, they also tend to be smaller and weigh less than higher duty ones, making them easy to maneuver even in tight areas. Most have small, compact handles as well, so they are comfortable for the welding operator to use. Light-duty MIG guns often use light or standard duty consumables—nozzles, contact tips and retaining heads (or gas diffusers). These consumables generally have less mass and are less expensive than their heavy-duty counterparts. Similarly, because they are designed for short arc times, the necks (or goosenecks) on light-duty MIG guns are made of lightweight materials, including polymer, rubber or light aluminum armor. The strain relief and connections on light-duty guns are also unique. In particular, the strain relief is usually composed of a flexible rubber component and in some cases may be absent all together. These features help maintain the gun’s light weight, but they can allow for kinking that may lead to poor wire feeding and gas flow. As a rule, light-duty MIG guns offer standard features at a lower price and typically need to be replaced more frequently. On the opposite end of the spectrum from the light-duty applications and MIG guns previously described are jobs that require long arc-on times and/or multiple-passes on thick sections of material. These applications include ones found in heavy equipment manufacturing for the agriculture, construction and mining industries, over-the-road trailers and trucks, and other similarly demanding welding jobs. For these applications, heavy-duty MIG guns are the best choice, as they can be used for continuous welding on one inch or thicker material and in harsh environments typical to such industries. Heavy-duty MIG guns generally range from 400 to 600 amps and are available in both air- and water-cooled models. Choosing between a water- or air-cooled heavy-duty MIG gun largely depends on welding application, operator preference and cost considerations. Water-cooled systems are more expensive and often require more maintenance. Specially treated coolant solution, rather than tap water, is necessary for a radiator cooling system because tap water can cause algae growth or scale (mineral buildup) on the internal gun surfaces and cable assembly. In addition, over time water can leak from hoses, the gun neck or heads, requiring immediate repair to prevent weld discontinuities and gun failure. However, despite the additional cost, when welding on very thick plate that requires high deposition and good weld penetration, a water-cooled heavy-duty MIG gun may be required. Heavy-duty MIG guns—both air- and water-cooled models—often have larger handles than their light-duty counterparts in order to accommodate the guns’ larger cables (due to the higher amperage being provided). Heavy-duty MIG guns often use heavy-duty front-end consumables that are capable of withstanding high amperages and longer arc-on times. The goosenecks on these guns are often longer as well, which puts more distance between the welding operator and the high heat output from the arc. Most goosenecks for heavy-duty guns are generally comprised of aluminum armor that protects it from damage from the high temperatures, plus day-to-day wear and tear. The addition of a heat shield is an option to protect the welding operator from the heat output of a high amperage MIG gun and longer arc-on time. This heat shield provides a barrier between the arc and the welding operator’s hand. Adding a unicable cover can help protect the power cable from a harsh environment, too. Heavy-duty MIG guns often feature locking triggers, as welding operators use these guns for multiple weld passes and/or long continuous welds and these types of triggers help prevent fatigue. Other heavy-duty MIG guns feature dual- or multi-schedule triggers that can be mounted on the top or the bottom of the MIG gun according to the position that the welding operator finds most comfortable. Heavy-duty MIG guns can also, in many cases, be customized to meet the needs of the application at hand. Some MIG gun manufacturers allow welding operators to configure a heavy-duty MIG gun according to their preferred handle style, gooseneck length and angle, and unicable length. Remember, just like any part of the welding process, MIG guns play an important part in obtaining the quality and performance desired for a given application. Overusing a light-duty MIG gun can easily result in poor performance, while using a heavy-duty MIG gun without cause can increase the cost of the welding operation unnecessarily. If a company has multiple power sources guns can be standardized to fit them through the addition of a feeder adapter. Doing so allows for one common MIG gun to be used throughout the operation, lessening the need to inventory multiple styles of guns and consumables. Ultimately the goal is to accommodate both the amperage and duty cycle of the application in the best way possible. And even more so, the selection can also conserve the resources of the welding operation and aid in achieving high productivity. The economy is in bad shape right now, but when it improves, the graduates of San Diego Continuing Education’s welding program will be well positioned to fulfill the need for skilled welders. Now in its 35th year, the school focuses on adult education for unemployed and underemployed San Diego-area residents. Its curriculum is narrowly tailored to the needs of local industries — specifically shipbuilding, construction and manufacturing. The school provides free training to any California resident and currently has 96 students and a waiting list of an additional 58 people. “Our program is set up to provide the student with experience on the same types of joint configurations, metal types and welding processes that they’re going to need when they enter the workforce,” explains welding instructor Bill Borinski. The program, which spans a minimum of 600 hours over 24 weeks, also prepares the students with the skills to obtain an AWS D1.1 (American Welding Society) Unlimited Certification by passing a visual and x-ray weld evaluation. Even with the school’s focused, industry-driven curriculum, there is still a vast amount of knowledge and skills to impart to the students, and the school strives to make every minute count. That, explains Borinski, is why it is so important for the school to have durable, time-saving welding equipment. “Downtime in business costs money — for us it costs knowledge,” he says. “If a student’s equipment is down, then he’s not learning. Our students have enough to concentrate on as it is, they shouldn’t have to worry about whether their equipment is working properly or not.” The school recently converted its welding labs to Bernard™ Q-Gun™ and Dura-Flux™ MIG Guns and Centerfire™ Consumables to prevent such problems. The guns and consumables came packaged with the school’s new power sources and wire feeders, and Borinski said he’s been very satisfied with the results. The program has been running the guns for 12 hours a day, four days a week, and there hasn’t been a single malfunction. The Centerfire consumables system has reduced student downtime and frustration, while also improving weld quality. In this open-enrollment program, students work on the material at their own pace until they master the skills required to graduate. New classes, which meet for 6.25 hours a day, four days a week, begin every month, and students can stop and start the program at their discretion. Students learn an AWS-certified curriculum in self-shielded and gas-shielded flux-cored welding on 3/8- to 1-inch mild steel using E70T-1 and E71T-8 welding wire. Students briefly learn the GMAW process, but the program spends the majority of its time providing specific skills that are needed immediately in local industries. They focus on building proficiency in all welding positions on butt, corner and T-joints. The school uses Bernard Q-Gun MIG Guns for its gas-shielded flux-cored and MIG training. Borinski noted that the gun’s curved handle reduces his students’ muscle fatigue after welding for long periods of time, and that the guns also improve their mechanical leverage, making it easier for the students to hold the guns in flat and horizontal welding positions. “What my students and I love about the Q-Gun handle is that when you put it in your hand, it’s already in a position to weld,” Borinski said. “If the MIG gun is putting strain on my students’ wrists, they’re going to be sore and miserable by the end of the day and they’ll probably lose some of their enthusiasm for a career in welding.” The Centerfire system further reduces his students’ educational downtime and frustration levels, Borinski said. By using a threadless contact tip with a large diameter tapered base that fits snugly into the diffuser and is locked in place by the nozzle, the Centerfire consumables make it nearly impossible for students to set incorrect contact tip recesses or for the tip to come loose inside the nozzle. “With our old brand of consumables, if we didn’t screw the contact tips in properly they would come loose and literally fly out of the end of the gun. That can really add to the frustration of a beginning welder,” Borinski said. While he is pleased with the guns and consumables, Borinski noted that it’s Bernard’s customer service that will keep him as a customer when their equipment eventually needs to be replaced. “To us, a gun is a gun,” Borinski said. “We can figure out on our own how it operates. Still, we were really impressed when a Bernard representative came out and offered to exchange any of our guns for free if the stock model didn’t perfectly fit our lab set ups.” Bernard’s Gun Exchange Program allows any one who receives a standard Q-Gun or Dura-Flux MIG Gun as part of a power source or wire feeder package to exchange the unused gun for a new gun with different cable length, neck, handle or trigger configurations. Bernard also provided Borinski with product information and support prior to and following his purchase to ensure the guns and consumables he ordered would meet his needs. “Sometimes the educational community gets sheltered from a lot of the outside activities that are going on. We don’t get exposure to the different equipment options that are out there,” Borinski said. “When Heidi Ewoldt, Bernard’s Inside Technical Sales Manager, called us and spent time explaining all of the equipment options and configurations available, it told us that Bernard wanted more than a quick sale. They were committed to our success.” “We’re running some pretty hot, high-amperage applications here,” Borinski said, “and we have had zero failures — zero internal issues, zero electrical issues. We haven’t even needed to change the liners on some of the guns.” Like Bernard, San Diego Continuing Education understands the value of strong partnerships and adapting its products to its customers’ needs. In order to meet the evolving demands of area industries, Borinski meets annually with an advisory committee composed of business and union leaders to discuss the skills and knowledge they look for in new employees. “If we taught what we wanted to teach and not what the employers in the area need, then we’re sending them people they can’t use and wasting our students’ time,” Borinski continued. “We must have our pulse on the industry in order to be a relevant educational institution.” In the last few years, Borinski said, the advisory committee has been asking for employees with “soft skills,” such as blueprint reading, teamwork training, lean manufacturing processes and other skills that go beyond laying a weld bead. “The job market is very competitive now,” Borinski said, “and those students with additional skills, who can add value to the organization, are going to have a significant advantage during the interview process.” That’s why the school partnered with the AWS to form a curriculum that provides students with the knowledge and skills they need to become AWS Certified Unlimited in FCAW upon graduation. The unlimited designation is a guarantee that the student can perform code-quality welds in the 1-G, 2-G, 3-G and 4-G positions using the FCAW process. This certification, combined with the schools blue print reading and teamwork curriculum, gives graduates a strong advantage when applying to one of the area unions, Borinski said. The school’s approach to welder training has resulted in numerous opportunities for its graduates in area businesses. One example is the school’s partnership with General Dynamics NASSCO, one of the San Diego’s largest employers. Through the partnership, General Dynamics NASSCO has hired over 400 of the program’s graduates in recent years. The main reason San Diego Continuing Education tried the Bernard guns and consumables was that they came packaged with the wire feeders and power sources the school purchased. Still, after using them without a single failure for the last 18 months, Borinski said one of the first questions he will ask when purchasing new equipment will be whether they accept Bernard guns and consumables. Luckily for him, Bernard’s products are adaptable to almost all major power source and wire feeder brands.
Tips for Maximizing Welding Operator Comfort and Productivity
Tips for Maximizing Welding Operator Comfort and Productivity
Selecting the right gas metal arc welding (GMAW) gun
Consider gun balance
Customize for the job
Use correct positioning and form
Maximizing comfort
Understanding Gun Ratings: What You Need to Know to Select Your MIG Gun
Understanding Gun Ratings: What You Need to Know to Select Your MIG Gun
Gun ratings explained
How do you operate?
Understanding the impact of heat
As an air-cooled MIG gun increases in amperage, the size of the cable, connections and handles also increases. Therefore, a MIG gun with a higher rated capacity almost always has greater mass. If you are an occasional welder, that weight and size increase may not bother you; however, if you weld all day, every day, it is better to find a lighter and smaller MIG gun suited to your application. In some cases, that may mean switching to a water-cooled MIG gun, which is smaller and lighter, but can also provide the same welding capacity. Deciding between air- and water-cooled
Final thoughts to keep you comfortable
Customizing Your GMAW Gun for the Job
Customizing Your GMAW Gun for the Job
This article has been published as a web-exclusive on thefabricator.com. To read the entire story, please click here.
Common Causes and Solutions to GMAW Gun Overheating
Common Causes and Solutions to GMAW Gun Overheating
This article has been published as an exclusive with Practical Welding Today on thefabricator.com. To read the entire story, please click here.
Preventive Maintenance Helps Optimize MIG Gun Performance
Preventive Maintenance Helps Optimize MIG Gun Performance
Proper inspection
Liner
Consumables
Final thoughts
Criteria for Selecting a MIG Gun
Criteria for Selecting a MIG Gun
What’s the right amperage?
Water- versus air-cooled
Heavy- versus light-duty
Fume extraction guns
Other considerations: Cables and handles
Conclusion
Proper Storage of MIG Guns and Consumables
Proper Storage of MIG Guns and Consumables
Common mistakes
Tips for MIG gun storage
Consumables storage and handling
Small steps for success
What’s Changing? Trends in Semi-Automatic MIG Guns
What’s Changing? Trends in Semi-Automatic MIG Guns
Building in features
Reducing fume
Configuring a MIG gun
Other trends
Money-Saving Tips for MIG Guns
Money-Saving Tips for MIG Guns
Tip No. 1: Protect the assets
Tip No. 2: Select the right neck
Tip No. 3: Perform regular inspections
Tip No. 4: Trim the liner properly
Tip No. 5: Select the best cable length for the job
Tip No. 6: Invest in consumables
Which is the Right MIG Gun? Tips for Making the Selection
Which is the Right MIG Gun? Tips for Making the Selection
Light- versus heavy-duty MIG guns
Air- versus Water-Cooled
Tips for Making a MIG Gun Last on the Jobsite
Tips for Making a MIG Gun Last on the Jobsite
Choose a gun to fit the application
Maintaining the gun
Regular and basic care and maintenance can help extend welding equipment life on a jobsite. Simple steps such as ensuring all connections are tight and in good working order and that the weld ground is good can help produce results every day. Inspection of the MIG or flux-cored gun, equipment and consumables every time the machine is started can keep things running smoothly and reduce unplanned downtime, which helps reduce costs, extend consumable life and improve welding performance. Selecting the Right Gun for MIG Welding Is Key to Achieving the Best Results
Selecting the Right Gun for MIG Welding Is Key to Achieving the Best Results
Selecting the right amperage
Choosing between light- and heavy-duty guns
Cooling options: air vs. water
Options for handles and cable selection
A side note on self-shielded flux-cored guns
The value of comfort
Gain Comfort, Productivity with the Right Welding Equipment
Gain Comfort, Productivity with the Right Welding Equipment
Don’t overdo the amperage
Picking the right handle
Reduce strain with the right neck
Benefits of shorter power cables
Other helpful tips
Parting thoughts
Premier Boat Fabricator Improves Productivity 25 Percent with New MIG Guns and Consumables
Premier Boat Fabricator Improves Productivity 25 Percent with New MIG Guns and Consumables
Gaining greater productivity
The Results
Attacking Weld Fume at the Source
Attacking Weld Fume at the Source
maintain compliance with safety regulations
and create a cleaner, more comfortable welding
environment. Proper use and maintenance of the
equipment is important to get optimal results.The basics
Benefits of fume extraction guns
Watch the degree of angle
the welding process right at the source, over and around the weld
pool. As with any piece of welding equipment, fume extraction
guns benefit from preventive maintenance.Flux-cored wire allows vacuum adjustment
Pause at the end
Wire type determines stickout
Experiment with the air control regulator
Proper maintenance and consumable usage
Fume extraction guns can provide results
Emergency Vehicle Service Provider Gains Versatility, Comfort and More from New Welding MIG Guns
Emergency Vehicle Service Provider Gains Versatility, Comfort and More from New Welding MIG Guns
New guns offer greater versatility and comfort
The added benefits of new consumables
Keeping the customer happy is priority No. 1
10 Money Saving Tips for Your Semi-Automatic MIG Guns
10 Money Saving Tips for Your Semi-Automatic MIG Guns
Tip No. 1: Protect Your Assets
Tip No. 2: Get a Neck Up
Tip No. 3: Inspect, Clean and Tighten Regularly
Tip No. 4: Trim It Properly
Tip No. 5: Line It Up
Tip No. 6: Lighten Up
Tip No. 7: Stay Connected
Tip No. 8: Keep It Smooth and Clean
Tip No. 9: Size It Right
Tip No. 10: Think Long Term
Fume Extraction Guns: Understanding the Basics
Fume Extraction Guns: Understanding the Basics
The basics of fume extraction guns
Applications, advantages and limitations
Maintenance tips
The Value of Comfort: Gaining Productivity with the Right Welding Gun
The Value of Comfort: Gaining Productivity with the Right Welding Gun
Minimize fatigue with the right handle
Keep power cables short, small
Reduce strain with the right neck
Staying comfortable by staying cool
Miller Welding and Machine Turns to Bernard for MIG Guns and Consumables
Partners In Growth
Miller Welding and Machine Turns to Bernard for MIG Guns and Consumables
From Humble Beginnings
Inventory Management
Reduced Downtime, Improved Quality
Guns that Stick
Simple Tips for Getting the Most from Your MIG Equipment
Maintain Your MIG Gun
Simple Tips for Getting the Most from your MIG Equipment
Which Semi-Automatic MIG Gun is Right for the Job?
Light- or Heavy-Duty? Which Semi-Automatic MIG Gun is Right for the Job?
On the Lighter Side
Finally, some unicables on light-duty MIG guns have crimped connections and may not be able to be repaired. If a crimped cable becomes damaged, the cable or possibly the entire gun may need to be replaced.For the Tougher Jobs
Parting Thoughts
Strong Bond and Strong Community at San Diego Continuing Education
Strong Bond and Strong Community at San Diego Continuing Education
Partnering for Success
Reaching out to the Community