Top Things to Teach a Robotic Welding Supervisor
Whether it’s in a small fabrication shop or a large manufacturing facility, investing in a robotic welding system is no minor expense. In many cases, the welding assigned to a robotic cell could also be performed in a semi-automatic or manual welding cell. However, it’s the potential advantages of the system — greater productivity, higher quality, better consistency and more cost savings — that make the purchase of a robotic welding system such an attractive option.
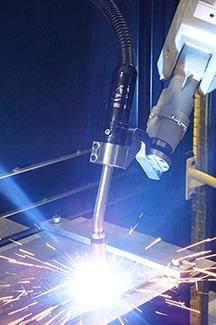
Obtaining those results isn’t a matter of chance. At the end of the day, the robotic system needs to be able to produce more parts at an equal or higher quality and accuracy than a human operator. It’s the job of the robotic welding supervisor to make sure that happens.
To achieve success in a robotic welding application, there are several key factors a robotic welding supervisor — especially one new to the task — must consider. Specifically, he or she must be able to understand the robotic system thoroughly, establish an effective documentation and maintenance routine, and look for ways to improve performance on an ongoing basis. In many cases, that may also mean enlisting the expertise of resources both inside and outside the company.
Tip No. 1: Understand the robotic welding system
Understanding the robotic system might seem like an obvious requirement for a robotic welding supervisor. With all of the administrative and operational duties that often accompany the role, however, it can be easy to simply delegate portions of the daily operation of the robotic welding system to shop floor personnel and/or the maintenance staff instead. That tendency, unfortunately, could lead to pitfalls by distancing the robotic welding supervisor from the ins and outs of the robotic welding operation.
For example, the robotic welding supervisor doesn’t necessarily need to be able to troubleshoot a circuit board malfunction or rewrite the welding program, but it’s important that this individual has a solid knowledge about these components, so if an issue arises he or she can quickly recognize that there is a problem and alert the appropriate personnel to rectify it.
The robotic welding supervisor should also know how the components in a robotic welding system — the robotic GMAW (gas metal arc welding) gun, consumables and cables, to mention a few — relate to each other and the impact they have on weld quality and productivity. Again, having this knowledge makes it easier to identify a potential problem and seek out the best solution.
Tip No. 2: Establish documentation, maintenance and control systems
Gaining robotic welding success depends in part on establishing a rigorous documentation, maintenance and control system. When problems arise, as they undoubtedly will, they never occur without a cause. The best way to start the troubleshooting process is to look back to the last thing that was changed in the welding process — or should have been changed, but was not.
Keeping an accurate and detailed log of everyone who enters the robotic welding cell is key. There should be documentation of everything personnel cleaned, changed or replaced in the cell, including adding new contact tips or other consumables, changing drive rolls or transferring a new drum of wire into the robotic weld cell. This record can help in identifying the source of a problem and getting the system back up and running with as little downtime as possible. Without such documentation, maintenance personnel could spend hours looking for the source of the issue, when in reality, they may only need a few minutes to rectify the situation.
Keeping a log of activities within the robotic welding cell will also assist the supervisor in establishing an effective predictive maintenance schedule, which is the best way to keep unexpected downtime occurrences to a minimum. An activity log can help predict when a gun cable liner will fail, for example, so that maintenance personnel can prevent unplanned downtime and quality problems by changing the liner beforehand.
Keeping traffic in and out of the robotic welding cell to a minimum is also important to reducing change within the operation and keeping documentation accurate. The more people coming and going from the cell, the more difficult it becomes to monitor and record activities that could affect the performance of the robot.
Tip No. 3: Look for continuous improvements
Getting the robotic system running at peak capacity and providing an acceptable return on investment is just the beginning of establishing an effective robotic welding operation. From there, the robotic welding supervisor should look for ways to optimize and improve the robotic welding operation on a continual basis.
A robotic welding cell might be running well enough to meet its daily production demands, but finding ways to improve its performance even more can bring significant advantages to a company. For example, creating greater efficiencies within the system can free up extra capacity that could be used to produce a product from somewhere else in the shop.
Also, it’s important not to settle for “good enough” in the robotic welding operations. Accepting suboptimal circumstances — for instance, that a robotic GMAW gun cable is rubbing on the robot arm and must be replaced every two months or that every two hours the operator must adjust welding parameters to accommodate consumable wear — can hinder the efficiencies sought in automation in the first place.
A robotic welding supervisor should never consider these types of activities as inherent to the production process, but rather seek out ways to rectify them in the name of continuous improvement. After all, a company that continues investing in robotic welding — compared to one who simply accepts and compensates for problems — stands a greater chance of gainining higher productivity and profitability, not to mention a competitive edge.
Tip No. 4: Rely on the available resources
To achieve the goal of continual improvement and optimization of the robotic welding operation, the supervisor should also know the resources available to him or her, both internally and externally.
Internally, everyone from the daily robot operator and the quality technician to the engineering staff and the sales team should be communicating with each other to help improve the existing robotic system. These team members can also play a vital role in helping identify the company’s future robotic welding needs.
The daily robot operators — those who load and unload parts and interact with the tooling — often know the specific robot and its idiosyncrasies better than anyone on the shop floor. As a result, they are often in the best position to alert the robotic welding supervisor about potential or existing problems. They may, for instance, notice that certain joint configurations or positions tend to result in excessive spatter, resulting in unnecessary post-weld clean up. By maintaining open communication with these individuals, the robotic welding supervisor can then employ the proper resources to rectify the problem.
Quality technicians can be another source of valuable information to help the robotic welding supervisor improve the performance of the operation. Quality technicians might notice that welds in a certain area of a part are regularly oversized. The supervisor can then take this information to engineering, which in turn can look for solutions to revise the weld sequence or identify different system components that could further improve productivity and cost savings for the robotic welding system.
Alternatively, an external resource, such as a robotic welding integrator or equipment manufacturer, can often offer insight and expertise gleaned from working with the robotic welding operations at other manufacturers. This knowledge can help companies to not only address issues within the robotic welding system, but it can also put these individuals in a position to offer advice that will make the operation run more efficiently.
In this respect, the robotic welding supervisor should take the role of a communicator. He or she will be the one who understands and gathers the information from the resources available, as well as facilitating the conversations necessary to improve and optimize the robotic welding operation.
Making responsible decisions that lead to growth?
Being responsible for the bottom line success of a robotic welding operation can be a daunting task. It requires a breadth of technical and business experience as well as strong people skills. Plus, as technology continually improves and evolves, the robotic welding supervisor must keep focused on improvement and optimization. They must also maintain open communication with resources both inside and outside of the facility. For those up to the challenge, however, the potential for a robotic welding system to improve quality, productivity and a company’s ultimate success is immeasurable.