7 Things To Know About Robotic Welding Systems
Implementing a robotic welding system isn’t something that happens on a whim — at least not successfully. Converting to this technology can help companies gain greater productivity, improve quality and reduce costs in the welding operation, but the process requires thorough planning to gain those results. Working closely with a robotic integrator is a good step to ensure every aspect of the implementation is carefully orchestrated and that the robotic welding system works properly for the given application — in reality, not just theory. Before adding a robotic welding system, it’s helpful to know some key factors that can maximize the return on investment (ROI) in the technology and also help prevent potential problems.
1. Part repeatability is critical to successful automation
The quality of part produced by a robotic welding system depends on the quality of the part that enters the weld cell. That’s why it’s not uncommon to hear the phrase “garbage in, garbage out” when it comes to robotic welding systems — if the part entering the welding cell is flawed, the subsequent weld will be, too.
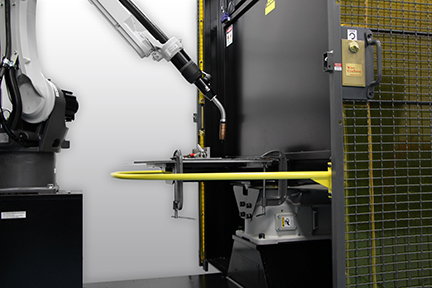
To protect against poor weld quality, it is critical to have simple, consistent parts that allow the robot to execute the weld in the same location, repeatedly. Having a blueprint or electronic CAD drawing is helpful for confirming that repeatability. Robotic integrators can review the blueprint or they may want to create a software simulation that assesses the suitability of the part for the robotic welding system. After the assessment, they can advise of any adjustments that need to be made prior to implementation.
Proper fixturing is also critical to achieving part repeatability, regardless of whether the application is high volume/low variety or low volume/high variety. Parts that meet the exact specifications can easily be welded incorrectly if they are not held in an exact position during the process. Many robot manufacturers offer vision systems to aid in part recognition and to ensure that the weld path can be altered in real time if part fit-up issues exist. These systems usually work very well, but may cost more.
2. Training is essential
Robotic welding systems require a properly trained operator to oversee them. A skilled welding operator or an individual with previous robotic welding management experience is a good candidate for the job. Again, a trusted robotic integrator is an excellent resource to provide the necessary training, which should cover proper programming, troubleshooting and preventive maintenance. As a best practice, companies should also consider ongoing training support to keep the operator’s knowledge of the system up to date. In many cases, robotic OEMs offer online tutorials, troubleshooting information and/or additional on-site training as aftercare support.
3. Additional safety equipment may be necessary
Many facilities already have fume extraction systems in place for manual welding operations, but converting to a robotic welding system may require additional equipment to help maintain a healthy work environment. With the increased production brought forth by a robotic welding system, there is also an increase in fume generation. Given the stringent regulations and recommendations from OSHA (Occupational Safety and Health Administration) and other safety regulatory bodies, proper equipment is necessary to maintain compliance.
For larger facilities with higher production robotic welding applications, a centralized fume extraction system is a good option. These systems involve the installation of ductwork throughout the facility and the placement of fume extraction hoods over the welding cell. Smaller shops with fewer robotic welding cells may want to consider a less expensive portable fume extraction system. Operators can wheel these systems right next to the welding cell and adjust the extendable arm toward the robot to suction the fumes. It is also critical that the proper cage and screens are in place around the robotic welding system to protect employees from the welding arc and moving parts within the cell.
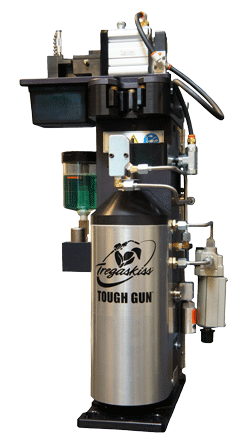
4. Weld data monitoring and/or peripherals can help improve results
Adding weld data monitoring capabilities and/or peripherals into a robotic welding system can help improve weld quality and productivity. Achieving these results, however, requires an additional up-front investment.
Weld data monitoring (whether integrated in a power source or via a third party) allows companies to track the parameters of individual welds, determine the cause of weld defects and identify general inefficiencies in order to rectify those problems and optimize the process for peak quality and productivity. This equipment requires the purchase of software and computers, as well as the establishment and maintenance of an Ethernet network throughout the facility. Companies will also need tech-savvy individuals to review the data and make the necessary adjustments to the robotic welding system according to the data provided.
Similarly, the addition of peripherals — particularly a nozzle cleaning station (also called a reamer or spatter cleaner) can improve weld quality and productivity. By cleaning spatter from the inside of the welding consumables on the front end of the GMAW welding gun, this peripheral helps extend consumable life, reduces downtime for changeover during production and also reduces the cost for replacing consumables. Nozzle cleaning stations also help minimize the loss of shielding gas coverage (due to spatter build-up) that could lead to poor weld quality and rework.
Proper maintenance can help protect the investment in automation
Preventive maintenance of the entire robotic welding system, including the robotic GMAW (gas metal arc welding) gun, consumables and cables is an important step in protecting the investment in this technology. Neglecting maintenance can easily lead to unscheduled downtime, poor quality parts and/or costly repairs. It may even lead to failures that require equipment replacements.
Scheduling time to check connections throughout the system, clean fixturing (to prevent debris that may affect part fit-up) and check TCP (tool center point) helps ensure that the robotic welding system continues to operate within its proper parameters. Certain maintenance can occur in between shifts — cleaning off the robot or changing consumables, for example — while other activities like greasing the robot’s joints may occur less frequently and during a longer scheduled stop. Companies need to assess their individual needs and plan the preventive maintenance schedule accordingly. For larger companies, hiring a maintenance crew to take care of preventive maintenance may be desirable.
6. Communication is key to proper weld quality and cost savings
Retrofitting robotic welding systems is a common practice among many companies, particularly those investing in automation for the first time or for smaller shops requiring only one or two weld cells. It’s significantly less expensive to purchase a used robot than a new one. When retrofitting a robot, however, it is absolutely essential that it is capable of communicating with the selected power source if companies are to have the entire robotic welding system function properly. New power sources feature software that may not be immediately compatible with a robot that is older, or in some cases, the robot may need a specific robotic GMAW gun that isn’t readily available at a welding distributor or possibly even discontinued.
For this reason, it is critical to contact an experienced robotic integrator who can both recommend and help set up all components in the retrofitted robotic welding system. The investment in this assistance can help ensure the proper functioning of the equipment and the long-term cost savings sought by implementing the system. Not to mention, it can also save a lot of frustration and downtime.
7. Robots can do more than just weld
Robots rely on the input of the operator to execute a given task. That task, however, doesn’t have to be limited to just welding or to welding the same part every time. Operators can program the robot to weld multiple parts over the course of a single shift, enhancing the versatility of the robotic welding system and positioning the company to produce additional output. Operators can also program robots to move parts so that a particular unit is not sitting idle when it isn’t tasked with welding; there are components that offer gripping capabilities and can be installed in addition to a welding gun. Companies may even have a tool dock that allows the robot to be fitted with a different tool and proceed with its work. Some companies with multiple robots may also benefit from installing a vision system in order to check on the work of the others, ensuring that part fit-up is optimal and that the robot is correctly placing welds.
Given that the goal of any robotic welding system is uptime, having the versatility to use a robot for multiple tasks can contribute meaningfully to the other advantages of this technology – increased productivity, improved quality, decreased costs — and may help give companies a real competitive edge.