5 Common Myths About Robotic Welding Systems
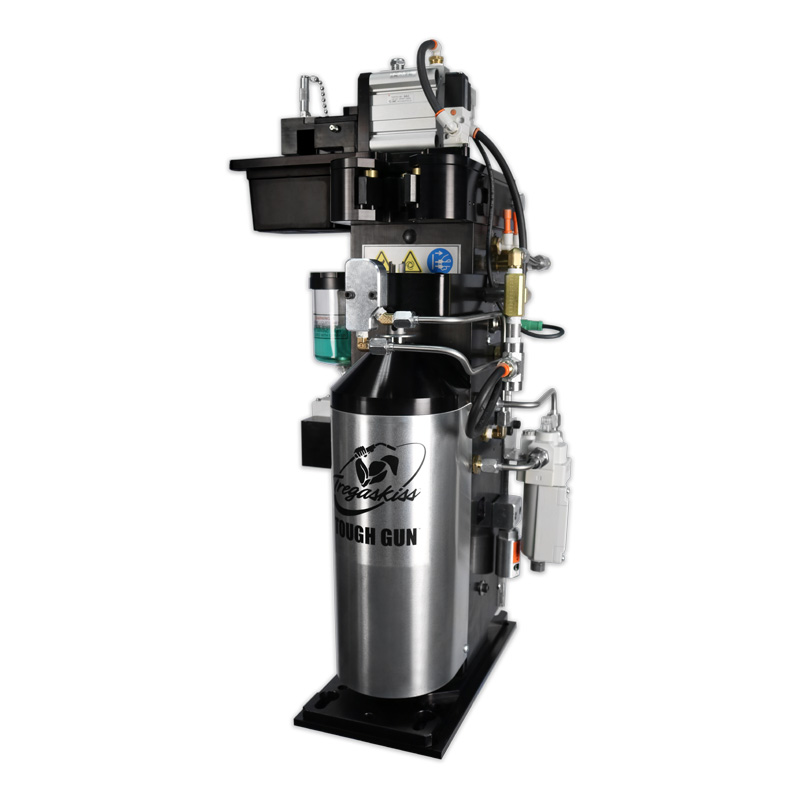
Robotic welding systems provide speed, accuracy and repeatability in many fabrication and manufacturing applications — features that can increase productivity and consistency, and reduce rework. The opportunity for savings due to these quality and efficiency improvements is a primary reason many companies make the investment in automation. There is also an increasing shortage of skilled welders entering the workforce, which makes welding automation an appealing option.
However, it takes more than just installing the system to have a profitable automated welding operation. Neglecting other important steps in the process — preventive maintenance, operator training and the use of complementary equipment called peripherals, for example — can result in a robotic welding system that is not performing as well as it should. A less efficient process can lead to more expenses via rework and downtime in the long run, since a robotic welding system is only as strong as its weakest link.
This article discusses some common myths about robotic welding systems that can keep a company from fully maximizing the return on investment in this technology, and provides advice to address those misconceptions.
This article has been published as a web-exclusive on thefabricator.com. To read the entire story by Tregaskiss product specialist, Vic Lubieniecki, please click here.