How to Choose the Right MIG Gun Liner
MIG gun consumables, including the liner, can make significant difference in gun performance and weld quality. A MIG gun liner spans from the front of the gun through to the power pin and is the conduit through which the welding wire feeds. Proper installation of the liner is critical to its ability to guide the wire through the welding cable and up to the contact tip — and to help an operation avoid the many problems that can result from improper liner installation, such as birdnesting, wire feeding issues and increased debris in the liner.
Various types of liners for the job
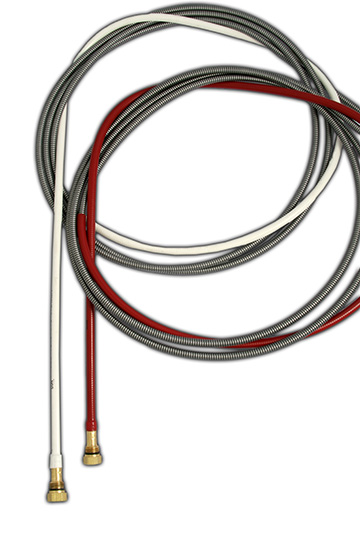
There are numerous liner types available that are usable for both semi-automatic and robotic applications. Choosing one is often up to the preference of the welding operator or maintenance personnel. Each type has advantages and disadvantages for specific applications in robotic and semi-automatic welding and can offer compatibility with varying gun styles and sizes.
The three main categories of liner types are conventional liners, front-loading liners and front-loading liners that have a spring-loaded module to accommodate for up to 1 inch of forgiveness for improperly trimmed liners.
Conventional liners are installed through the back of the gun and are longer than the cable, often up to 25 feet long. These are frequently used in the industry; so many welding operators are familiar and comfortable installing this type of liner.
A disadvantage of conventional liners is the lengthy changeover process. In the cases of liner replacement, this may require the welding operator to climb over robotic tooling or transfer systems to remove the gun from the wire feeder. In the case of semi-automatic MIG guns that are connected to boom-mounted feeders, the welding operator may need to climb several feet into the air to change liners. Another disadvantage of conventional liners is that they can’t account for changes in length as the cable grows and shrinks with twisting (due to the fact that MIG gun cables are wound in a helix pattern). This can lead to the liner not being seated properly inside the retaining head.
Front-loading liners are, as the name implies, installed from the front of the gun. This offers timesaving advantages, since the welding operator does not have to leave the front of the gun for changeover, which can reduce downtime. Front-loading liners have the same disadvantage as conventional liners, since they can’t grow or shrink with the cable as it twists and moves. Jump liners are a type of front-loading liner-. Whereas standard front-loading liners are full length, jump liners are shorter — often about 1 foot long — and replace only the part of the liner that wears the quickest, typically at the neck of the gun.
The third main category is front-loading liners that have a spring-loaded module inserted into the power pin, allowing for up to 1 inch of motion as the cable twists and springs up and down. This type of liner tends to be more forgiving if the liner is trimmed incorrectly.
Closing thoughts
Choosing the right type of liner for the application can help an operation avoid feeding issues and reduce downtime. While welders may have a preference on liner type, be aware that each type of liner has advantages and disadvantages for specific applications and can offer compatibility with varying gun styles and sizes.