Gain Efficiencies and Extend Consumable Life with Anti-Spatter Compound
When it comes to robotic welding operations, uptime is key. Minimizing air movements and ensuring consistent workflow are just as important as selecting the right robot, power source and robotic gas metal arc welding (GMAW) gun. Everything should work in conjunction to bring about the greatest efficiencies. The result can be higher productivity, better weld quality and an improved bottom line — not to mention, the potential for a competitive edge.
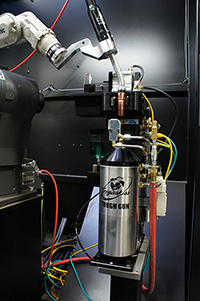
A nozzle cleaning station (also called a reamer), along with a sprayer for delivering anti-spatter compound, can be simple and effective additions to the robotic weld cell — and ones that offer a good return on investment. Anti-spatter compound can also be delivered from a single large drum via a multi-feed system to numerous robotic weld cells.
Anti-spatter compound protects the front-end consumables on a robotic GMAW gun from excessive spatter accumulation, which can restrict shielding gas flow, increasing the risk for porosity. This compound also helps prolong the life of the nozzle, contact tips and gas diffuser, and can reduce downtime for consumable changeover. In addition, it can lower the cost for consumable inventory (and its management), and reduce operating costs by improving weld quality and lessening rework by way of consumables that operate at peak performance. All of these factors contribute to a more productive and profitable welding operation.
The what, when and where of anti-spatter compounds
Although it resembles water in its consistency, anti-spatter compound (when applied correctly and in the appropriate volume), will not drip like water. It simply creates a sacrificial barrier between the nozzle and any spatter generated during the welding process; the spatter easily falls off when the nozzle cleaning station performs the reaming cycle, thereby leaving the nozzle and other front-end consumables clean. The compound must be reapplied frequently to help maintain that barrier. tt
Constant-voltage (CV) applications and those utilizing solid wire and/or the welding of galvanized steel tend to produce high levels of spatter, and therefore, often benefit the most from the use of anti-spatter compound. However, the application of anti-spatter compound is ideal for any high-volume, high-production environment seeking to minimize potential weld quality issues, extend consumable life and also reduce downtime. Its application can easily be programmed so that it is sprayed onto the consumables after each ream cycle, during routine pauses in production for part changeover.
When selecting an anti-spatter compound, be certain that it is capable of providing uniform coverage to protect the entire nozzle, that it cleans up easily and leaves no residue, and that it is compatible with the nozzle cleaning station being used. Water-soluble anti-spatter compound is the most popular option, and is typically non-toxic and eco-friendly. Oil-based anti-spatter compound is also available in the marketplace, but is generally less desirable to use because it is more difficult to clean up if it settles on fixtures or elsewhere in the weld cell. It is also important to note that oil-based anti-spatter compound is not always compatible with all nozzle cleaning stations and it can clog up this equipment.
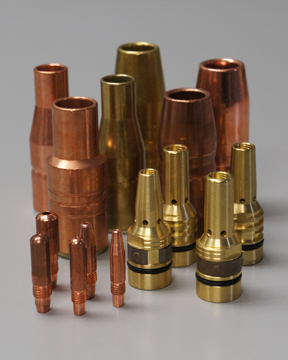
Despite the fact that the more popular water-based anti-spatter compound is non-toxic, welding operators and/or maintenance personnel should still take care when handling and using it. They should avoid breathing in spray mists and always wash their hands after coming in contact with the compound (for example, when filling the sprayer). The use of a NIOSH certified (or equivalent) respirator during spraying is recommended. Also, personnel should wear Nitrile or Butyle gloves and wear chemical safety goggles for the best protection. Local exhaust ventilation near the sprayer is also important. Store anti-spatter compound containers according at the temperatures recommended by the manufacturer.
Best practices for anti-spatter compound use
Positioning the robotic GMAW gun and front-end consumables in the correct location for the ream cycle and anti-spatter application helps the compound to be applied uniformly. To gain optimal spray coverage, always follow the manufacturer’s instructions for proper setup based on the nozzle bore size. If the sprayer is too far away from the nozzle, it will not provide adequate coverage to prevent spatter buildup. If the nozzle and sprayer are too close, too much spray may saturate the nozzle insulator, which can lead to premature failure.
Spraying for about a half-second is the standard recommendation. If a company finds that it is necessary to spray the anti-spatter compound any longer, that usually means the sprayer is too far away. In fact, anti-spatter compound should never be sprayed for three or more seconds. In addition to causing harm to the consumables, excess spraying can leave a residue of the compound in the weld cell that could lead to safety issues, such as slick floors and slipping hazards. Over-application of anti-spatter compound may also damage equipment, such as power sources, by adversely affecting electrical circuits it comes in contact with.
Adding a spray containment unit
Some manufacturers offer a spray containment unit, which can help capture excess anti-spatter compound. This 3 to 4-inch unit fits over the spray head on the anti-spatter compound sprayer. After the spatter has been cleared from the nozzle during the reaming cycle, the nozzle docks on the spray containment unit. An opening at the top of the cylinder allows the anti-spatter to spray onto the nozzle while an O-ring seals the nozzle in place so only the outside edge and inside of the nozzle are sprayed.
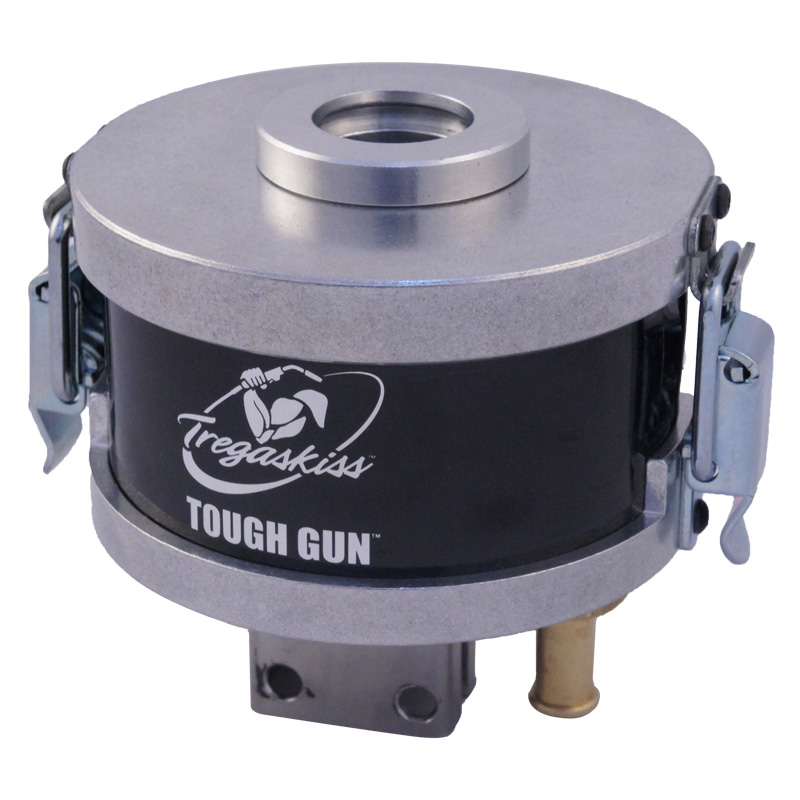
which can help capture excess anti-spatter compound.
This 3- to 4-inch unit fits over the spray head on the
anti-spatter compound sprayer.
The spray containment unit also collects any anti-spatter compound runoff at the bottom of the unit so it can be easily drained into a container and disposed of properly. Anti-spatter compound cannot be reused and should be disposed of in accordance with federal, state and local environmental control regulations.
When employing a spray containment unit, it is important to inspect it regularly, removing any spatter or debris from the bottom that could prevent it from working properly. As part of a preventive maintenance activities, clear the screen or filter inside the unit of contaminants using clean, compressed air. Doing so helps ensure that the screen can continue to fulfill its intended purpose of improving air quality.
As with any part of the robotic welding operation, when employed properly, this unit and the use of anti-spatter compound can yield positive results. Always follow the manufacturer’s recommendation for use and consult with a trusted welding distributor with any questions.
Additional tips for effective nozzle cleaning station operation
In conjunction with anti-spatter compound, a nozzle cleaning station improves quality and productivity in robotic weld cells by helping extend consumable life and reducing downtime for changeover. Here are some tips to get the most out from this equipment.
Correct placement: Place the nozzle cleaning station in close proximity to the robot so it is easily accessible.
Match parts and sizes: Make sure the V-block inside the top of the nozzle cleaning station is the correct size for the nozzle, that the cutter blade is the correct size for the nozzle bore, and that the insertion depth of the nozzle to the reamer is adequate.
Monitor the home signal: Monitor the home signal on the nozzle cleaning station to reduce issues during the cleaning cycle and minimize guesswork regarding whether the equipment is ready for use or done with its cycle.
Clean and scrape parts: Clean the top seal on the spindle under the cutter and make sure all clamp faces are kept clean by scraping the faces and jaws on the V-block to remove debris. Buildup on these parts can push the nozzle out of position, leading to the fit-up no longer being concentric — and, potentially, to broken cutter blades.