Equipment, Training, Maintenance and More: Best Practices for Successful Robotic Welding
The cost to implement welding automation can be substantial, requiring companies to plan out the purchase carefully and to justify the expenditure to the appropriate financial or management personnel. The payback on the investment, however, can be equally beneficial. From productivity increases to quality improvements and cost savings, companies can often position themselves for greater competitiveness in the marketplace by adding robotic welding systems to their welding operation or by replacing manual welding cells altogether.
Unlike companies that employ semi-automatic welding, those with robotic welding systems have the added responsibility of protecting the large capital investment in the equipment. But no two robotic welding systems are the same and likewise, there is no single step to ensure a successful outcome. Rather, a combination of the appropriate planning, equipment purchases and personnel training — among many other things — provides the best results. Paying close attention to the daily occurrences in a robotic welding cell and engaging regularly in some of the best practices discussed here can also help provide high quality results.
Manage parts and workflow
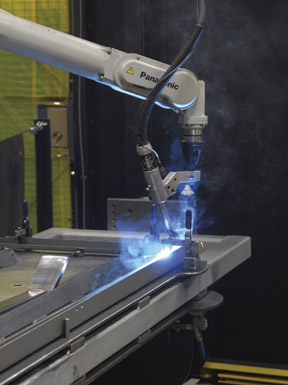
Companies typically invest in welding automation to expedite the welding process, gain more consistent weld quality and/or to reduce costs. The process can also set companies apart from the competition by allowing for faster completion and delivery of products. For companies with high-volume demands and low-variation parts, robotic welding can become an important part of their production plans. Smaller companies with lower-volume, high-variety parts can also benefit, but they may require more flexible tooling and more programming time to accommodate for several types of products.
The important consideration for both high- and low-volume production is to ensure that the parts to be welded lend themselves appropriately to an automated welding process. Robotic welding systems rely on consistent parts to provide consistent results. Companies that have or are planning to implement a robotic welding system need to be certain that parts are simple and repeatable. The presence of gaps, poor fit-up or poor joint access can have a detrimental impact on the high quality sought with robotic welding systems.
Similar to a semi-automatic welding application, consistent workflow is also important for a successful robotic welding operation, with the main difference being the speed at which parts are delivered and welded since a robotic system is so much faster. The parts need to enter and leave the cell at a quicker and steadier rate — without bottlenecks — to gain optimal throughput.
Companies should assess each activity leading up to the part entering the cell, making sure that the supply of parts matches the robot’s cycle time, and also assess the steps for handling the part after it leaves. In some cases, it may be necessary to change how the parts are fabricated upstream and completed downstream (e.g., finishing, painting, etc.) to establish good workflow. Companies should also look to eliminate non-value added activities, including excessive lifting or handling of parts, and avoid multiple trips to stack products or other similar activities.
Protect against premature component failures
Robotic welding systems typically operate at higher amperages and longer duty cycles than semi-automatic welding operations — the robots can withstand the greater arc-on time and heat compared to a human operator. While those increases are excellent for supporting high productivity, the additional heat and welding duration can be especially harsh on consumables — nozzles, contact tips and gas diffusers (or retaining heads).
Companies need to take steps to avoid the pitfall of excessive consumable changeover. Entering the weld cell for purposes other than part changeover or routine pauses in the operation can add unnecessarily to downtime, which can easily add up per shift, day, month and year, resulting in lost productivity. Excessive consumable changeover is also costly, as it increases inventory and inventory management.
There are two key steps companies can take steps to increase consumable life in their robotic applications and reduce downtime. One, install consumables properly and maintain tight connections throughout the course of welding. Loose connections increase electrical resistance, causing the consumables to generate additional heat that can shorten their lifespan and/or cause them to perform poorly. Follow the manufacturer’s instructions for proper consumable installation, taking care to tighten the consumables appropriately. It’s also a good idea to check the consumables periodically during routine pauses in welding, as they can loosen throughout a shift.
Two, install the robotic MIG gun liner properly, as this helps prevent downtime to address wire feeding issues or to correct a burnback, in which the wire “burns back” into the contact tip. Follow the manufacturer’s instructions for trimming and installation, using a liner gauge to confirm the correct liner length.
Preventing premature power cable failure, which can occur in both through-arm robotic welding systems (where the cable feeds through the arm of the robot) or in standard robotic welding systems (also referred to as over-the-arm) is also important. Be mindful of the path the robot has been programmed to follow, the speed at which it moves and the cable length. The power cable should clear the robotic arm and tooling to prevent it from catching or rubbing against either part. Also, the robot should be programmed not to move too fast or abruptly. Aggressive movements can cause the power cable to snap. Make sure that the cable is the appropriate length — too short of a cable can stretch beyond its capacity during routine robotic movements, leading to greater wear. If the power cable is too long, it may be prone to kinking or becoming pinched by the robot’s arm.
Don’t neglect maintenance?
Preventive maintenance (PM) programs are among the most effective best practices a company can instill for a robotic welding system. Ideally, PM programs should cover every aspect of the system — from the robot to the contact tip. Proper PM activities can help prevent unscheduled downtime, low quality parts, costly repairs and/or equipment replacements.
Companies will need to assess their PM needs on an individual basis and engage a maintenance team or other personnel to carry out the activities at the appropriate times and intervals. As a general rule, companies that weld thick materials or have applications with long, continuous welds common in welding automation can benefit from more frequent PM activities, as the rework for quality issues can generate much more costly rework compared to an application producing multiple smaller parts. Several PM activities can occur during routine pauses in production, including:
• Cleaning the robot and fixturing to prevent the buildup of dirt, debris or anti-spatter compound, which could affect part fit-up.
• Checking for tight consumables connections.
• Confirming tool center point or TCP (discussed in more detail later).
• Checking for power cable wear and replacing as needed.
Other activities that happen less frequently like greasing the robots joints can be completed during a longer scheduled stop.
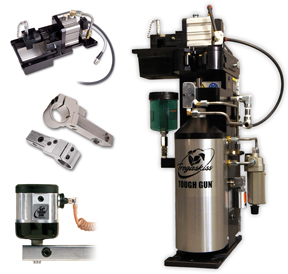
Always consider peripherals and robotic MIG gun extras
Peripherals are often an overlooked part of the robotic welding system. The added cost of this equipment, which includes nozzle cleaning stations (also called reamers or spatter cleaners), is frequently considered an unnecessary expense. In reality, this equipment can maximize robotic welding performance and help companies gain a better return on investment (ROI) from their robotic welding system.
As its name suggests, a nozzle cleaning station cleans the nozzle of dirt, debris and spatter, typically during routine pauses in the robotic welding operation. The goal of this cleaning action is to help ensure consistent shielding gas coverage, and with it, reduce weld defects, expensive rework and lost productivity. A nozzle cleaning station also helps extend the life of consumables, minimizing the downtime and expense for changeover.
For the best results, the nozzle cleaning station should be mounted in close proximity to the robot to reduce the amount of time necessary for its arm to reach it. Companies can mount the peripheral overhead if need be. The robot should be programmed to clamp onto the nozzle cleaning station at a taught position exactly perpendicular to the cutting blade that clears out the spatter or other debris. Any misalignment to the position of the nozzle could lead to partial cleaning of the nozzle and excessive spatter build-up. Program the robot to go to the nozzle cleaning station as often as possible; the cleaner the consumables are, generally the better performing and longer lasting they will be.
For companies who choose to attach an anti-spatter sprayer, it’s important to locate the spray in the appropriate position so it completely coats the inside of the nozzle. Ideally the outside should be covered to within three-quarters of an inch from the bottom of the nozzle.
Other peripherals that companies can integrate into their robotic welding system include a wire cutter and a neck inspection tool (discussed in the next section). A wire cutter cuts the welding wire to a specified length, removing any inconsistencies at the end, providing for more reliable and smoother arc starts and better seam tracking for robots featuring that technology. For companies using touch sensing software, using a wire cutter in conjunction with a robotic MIG gun featuring a wire brake can help prevent problems with seam tracking. Touch sensing allows the robot to store position data and send electrical impulses back to the controller once it has located the joint. For applications that have slight variations in parts, touch sensing helps maintain weld consistency. It is also more cost-effective than investing in new tooling and fixturing to hold a part in a precise location; if the part moves slightly, the robot can still locate the joint and weld accurately, as long as the joint has well-defined edges. Using a wire cutter can ensure the wire is cut to a consistent length; the wire brake holds the wire in a set position as the robot articulates and searches for the weld joint, ensuring more accurate touch sensing readings for more consistent weld quality.
Stay on target
For a robot to be repeatable and provide consistent welds, it is important for the system to maintain its tool center point or TCP, which is the focal point of the robotic MIG gun and its relationship with the position of the welding wire in the joint (gun-to-work distance).
Typically, but not always, TCP issues occur after a collision, during which the neck of the robotic MIG gun becomes bent. To rectify the issue, welding operators can employ a peripheral called a neck inspection tool (or neck-checking tool) to bend the neck back to the proper angle. Most neck inspection tools are designed to accommodate standard necks for a particular brand of robotic gun. To use this peripheral, the welding operator or maintenance personnel needs to determine the tolerances for the robotic welding program and adjust the bent neck to meet the correct specifications.
To maintain TCP, it is also important to install the robotic MIG gun neck properly, making sure it is fully seated. If not, it will extend too far and can cause TCP to be compromised. Programming the robot for a TCP check to verify proper position can also help prevent against quality issues and potential downtime.
Another best practice to help ensure on-location welds is to check that fixturing is in the correct place, that it doesn’t allow the parts to move and that the base of the robot is securely in place. Periodically check that part variation hasn’t changed, as well.
Find the right people
Designing parts for automation, managing workflow, selecting the right equipment and implementing a consistent PM program mean nothing if companies don’t have the right personnel in place to work with and/or oversee the robotic welding system. Investing in the people who are responsible for interacting with the robotic welding system should always be a priority.
Skilled welding operators or employees with previous robotic welding experience are often a good choice for overseeing a robotic welding system. The personnel should undergo the proper up-front training before taking on the responsibility of working with the robotic welding system — loading and unloading parts and programming the robot for instance. Robotic welding integrators and robot manufacturers can often provide OEM-based training and continuing education. The goal is to instill the skills necessary not only to work with the robot on a daily basis, but also to be able to hone troubleshooting skills that can promote the maximum uptime in the robotic welding cell. These individuals can also be part of the PM programs mentioned earlier.
Protecting the investment
As with any capital investment, companies need to take the appropriate steps to protect their robotic welding system. Whether it’s the addition of peripherals or implementing additional training, engaging in a few best practices can help companies gain a solid payback on the equipment, empower employees to be part of the company’s success and establish the robotic welding system as a profitable part of their business. The items discussed here are by no means exhaustive. Companies can seek out ideas for improving their operation from other, non-competitive companies, or work with a trusted welding distributor or robotic integrator for further options.