The Value of Comfort: Gaining Productivity with the Right Welding Gun
The term “ergonomics” has become increasingly common in the workplace as companies strive to improve safety and efficiency among employees — whether in the office or on the plant floor. At its most basic level, ergonomics refers to the discipline or science of designing equipment and arranging the work environment for optimal worker comfort and productivity. Minimizing fatigue, reducing repetitive motion, and decreasing overall physical and mental stress are some of the key factors at the heart of it.
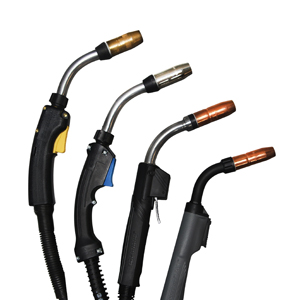
For welding operators who spend their time maneuvering around difficult weld joints with a MIG, flux-cored or fume extraction welding gun and facing a hot arc, the term takes on an especially important meaning.
A welding gun’s handle, neck and power cable design can significantly impact the duration of time a welding operator can weld without experiencing fatigue or stress. So too can the heat generated in the process. Excessive heat, just like musculoskeletal strain, can contribute negatively to the welding operator’s health and efficiency.
In the long run, choosing a welding gun that offers greater comfort and operates at a cooler temperature can help increase productivity and, ultimately, the profitability of the welding operation by allowing for greater arc-on time.
Minimize fatigue with the right handle
When welding, the first factor in good ergonomics is to select a welding gun with the appropriate handle design. Typically, manufacturers offer handles in curved and straight designs, one or the other of which may be more comfortable for a given welding operator to hold and control. The preference is individual and a welding operator may need to experiment to determine which design best suits him or her.
If possible, a welding operator may want to consider using a slightly lower-amperage welding gun to gain greater comfort and minimize fatigue and/or stress on the wrists and hands. Typically, as a welding gun’s amperage decreases, so too does the size of the gun handle, which makes the equipment lighter and easier to maneuver for longer periods of time. It is important, however, that in selecting a smaller and lighter-weight handle, the welding operator still has a gun that meets the application’s amperage and duty cycle requirements.
Duty cycle is defined by the amount of arc-on time in a 10-minute period that the equipment can be operated at maximum capacity. Some welding guns will offer 100 percent duty cycle, while others are rated 60 percent or below.
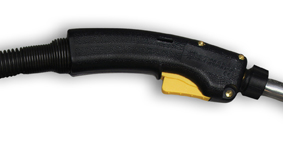
In many cases, a welding gun rated at 300 amps, for example, may suffice for a 400-amp application considering that welding operators rarely weld continuously enough to exceed the gun’s duty cycle.
In a shop setting, another option to gain greater comfort and productivity would be to convert to a water-cooled welding gun for MIG applications, as these guns are generally smaller, lighter and easier for welding operators to manage for longer periods of time.
Keep power cables short, small
Smaller, shorter and lighter power cables offer greater flexibility to welding operators, making it easier to maneuver the equipment without excess stress on the wrists or hands. A good rule of thumb is to select the smallest and shortest power cable possible that can still meet the needs of the application. Smaller, shorter power cables can also minimize clutter in the weld cell by preventing excessive coiling and minimizing tripping hazards. Less clutter and coiling also reduces the chance of poor wire feeding that could cause downtime and hinder productivity.
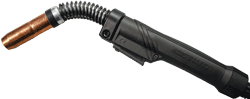
On fume extraction guns, look for vacuum hose swivel on rear of handle, as this feature improves flexibility and reduces welding operator fatigue.
Reduce strain with the right neck
Many MIG and flux-cored guns are available with rotatable and flexible necks in various lengths and angles. These types of necks allow the welding operator to select one that will best suit the joint access required for an application. For example, rotatable necks are a good option for welding out of position, even overhead. They do not require the welding operator to change the welding gun handle or position, so he or she can hold the gun in a way that is most comfortable, while also gaining access to the weld joint.
Similarly, flexible necks can be easily adjusted to fit different welding angles and reach difficult joints that may be restricted or otherwise awkward to reach. This feature also helps minimize straining to reach a particular weld joint, and with it reduces the opportunity for fatigue or injury.
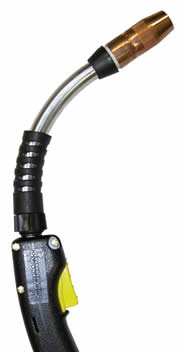
Some welding gun manufacturers also offer neck couplers. These accessories allow the welding operator to connect multiple necks together to reach especially difficult joints more comfortably.
Staying comfortable by staying cool
Increasing productivity in a welding operation by way of improved ergonomics is a matter of more than just having lightweight, easy-to-control equipment. It’s also a matter of minimizing heat stress in the work environment.
When welding materials such as aluminum or stainless steel, there is an opportunity for greater radiant heat — heat that reflects from the welding arc and base metal back to the handle. Welding operators can use a longer neck on the welding gun to place the handle further back from the arc when welding on such applications.
Also, the addition of a neck grip on a MIG gun can protect the welding operator from heat exposure and related fatigue. These high-temperature silicon rubber grips slide over the neck and offer the added benefit of increased control. They allow welding operators to rest the neck on their hand or forearm, using it as a pivot point to maneuver the MIG gun more comfortably.
In the end, having equipment that is easy to operate during the welding process is the first step in achieving good ergonomics, a safe work environment and greater productivity. After all, a more comfortable welding operator is a more content one. And more content employees can help companies generate greater throughput on a day-to-day basis. Start the process by finding welding guns that are lightweight, offer an appropriate handle and neck design, and feature the right neck and power cable for the job and for the welding operator.