Fume Extraction Gun: Features and Techniques to Improve Performance
Limiting exposure to welding fumes is an increasingly important issue for many welding operations, as it provides a cleaner, more comfortable work environment and helps companies stay compliant with changing regulations.
The Occupational Safety and Health Administration (OSHA) and other safety regulatory bodies set the allowable exposure limits for weld fumes and other particulates, including hexavalent chromium, with the aim of protecting employees against potential health hazards in the workplace.
Some companies may choose a centralized fume extraction system designed to protect the entire shop area. However, these systems can be a substantial investment and often require installation of new ductwork. In some welding applications, they are not a feasible or efficient fume extraction option.
A fume extraction gun is a viable alternative in certain welding applications, including when the welder is in a tight or confined space or must move often to complete welds on a large part. Welding guns with built-in fume extraction are commonly used in heavy industrial welding, such as truck and trailer, rail car and heavy equipment manufacturing.
Fume extraction welding guns capture the fumes generated by the welding process right at the source, over and around the weld pool, and they can be tailored to best meet the needs of a specific application or to welder preferences. Consider these key factors to help choose the right type of fume extraction gun for the job — and learn more about available features that can help improve gun flexibility and performance in certain applications.
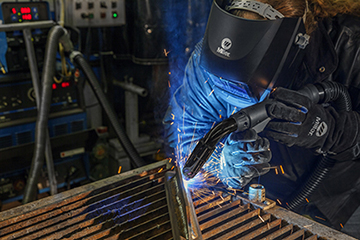
Fume extraction gun options
Fume extraction guns are available in a variety of amperages and handle designs. Common amperages for fume extraction guns range from 300 to 600. Keep in mind that amperage is tied to gun weight. The higher the amperage, the more copper required in the power cable and therefore the heavier the gun will be.
Due to this additional weight, use the lowest amperage gun possible that will still allow the job to be completed. Along with the added weight, higher-amperage guns typically cost more than lower-amperage guns, so it may be a waste of money to buy more gun than necessary for the application.
However, automatically buying the lightest gun available may not provide the amperage or durability needed for the application. Some lighter and more flexible guns aren’t durable enough for heavy industrial applications. Always consider a gun’s duty cycle rating, and keep in mind that it’s a balancing act between gun weight and durability when choosing a fume extraction gun.
Features to consider
Some fume extraction guns on the market offer features and capabilities that help optimize fume capture while also providing benefits for operator comfort and ergonomics, gun performance and ease in producing quality welds. When choosing and configuring a fume extraction gun, consider these options:
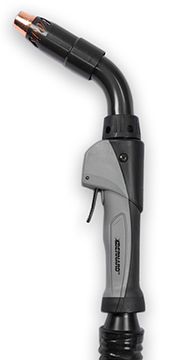
- Adjustable vacuum chamber: The nozzle on the front of most fume extraction guns is covered by a vacuum chamber. While vacuum chambers on some guns are fixed in place and can’t be moved, other guns have adjustable vacuum chambers that can be moved to several positions. This provides better joint access and visibility and helps welders dial in vacuum flow to eliminate porosity. Adjustable vacuum chambers can also improve ergonomics, since they reduce the need for the welder to position his or her body in uncomfortable positions to get a better view of the weld pool. Adjustable vacuum chambers that snap into position also provide greater durability than friction-fit chambers, which can loosen over time and eventually fall off. This can require replacement of the vacuum chamber. Some gun manufacturers also offer various vacuum chamber options, such as a short vacuum chamber that helps increase visibility and access to the weld pool.
- Suction control valve: Most fume extraction guns offer a way for welders to control the vacuum suction and optimize gas flow. Look for a gun with a vacuum regulator — often positioned at the front of the handle — that allows welders to balance suction with shielding gas flow to protect against porosity.
- Flexible, crush- and snag-resistant hose: A vacuum hose designed to be crush- and snag-resistant eliminates the need for a protective hose cover in many applications. This helps reduce overall gun weight and increases flexibility of the hose. However, be aware that some heavy-duty welding applications requiring extremely high heat will always need a leather cover to protect the hose. Note, a gun with a vacuum hose that swivels also improves flexibility, visibility and joint access and helps reduce wrist fatigue.
- Handle and neck options: Tailoring the gun handle and neck to the application and welder preferences can help improve weld access and reduce operator fatigue. Some brands of guns are available in curved and straight handle options. In higher-amperage applications, welders may want to put the gun cable over their shoulder with the gun trigger on the top. Straight handle guns allow for this because they trigger can be positioned on the top. Some fume extraction guns also have additional neck options in a variety of bend angles, such as 30, 45 and 60 degrees. This provides even more ability to tailor a gun to specific needs and improves ergonomics. When choosing a gun with a straight handle, consider one with a rubber overmold on the handle to help reduce vibration and provide a better grip.
Fume extraction gun best practices
As with any fume extraction equipment, proper use and maintenance of fume extraction guns is important to achieve optimal results. Operating a fume extraction gun is similar to using a standard MIG gun, with many of the same recommended best practices. However, there are some techniques that welders can follow to help get the best performance from a fume extraction gun:
- Degree of angle: Perhaps the most important tip for optimizing performance is using the appropriate degree of angle. With solid wire, use a push technique and an angle of 0 to 15 degrees for optimal fume capture. For flux-cored wire, use a drag technique with a 0 to 15-degree angle. If the parts are set up at a 0 to 30-degree angle and the gun is kept straight (vertical) during welding, the fume will rise, allowing optimal fume extraction by the gun.
- Pause at the end: At the end of each weld, pausing for 10 to 15 seconds and holding the fume extraction gun in place without depositing weld metal allows the gun to capture residual fumes as the weld bead is cooling.
- Wire type determines stickout: The contact-tip-to-workpiece distance can be longer — about 1/2 inch to 3/4 inch — when welding with flux-cored wire and a fume extraction gun. With solid wire, stickout should be kept to 1/2 inch or less to maximize fume capture.
- Frequent inspection: Inspecting the front end of the gun is key to optimizing fume extraction. Regularly inspect the nozzle, contact tip and vacuum chamber for signs of spatter buildup, which can block fume extraction and obstruct shielding gas flow. Replace consumables when spatter buildup appears or clean them according to the manufacturer’s recommendations. Also, routinely inspect the vacuum hose for damage, cuts or kinks and replace the hose as necessary.
- Proper maintenance: As with any welding equipment, fume extraction guns benefit from preventive maintenance. More frequent maintenance is required when using the guns with flux-cored wire because of the slag and fumes the wire generates. Regular maintenance helps prevent a clog or spatter buildup, which can limit the gun’s fume capture rate.
Getting results
Some fume extraction guns are designed using a common consumable platform, which means any consumables used on a standard MIG gun or even a robotic MIG gun can also be used on a fume extraction gun. When fume gun replacement parts — nozzles, contact tips and gas diffusers — can be the same as those used on standard MIG guns, this offers greater flexibility and helps reduce a company’s consumables inventory. Additionally, it may be important for some companies to choose a fume extraction gun that is compatible with vacuum systems from most major manufacturers.
In the right applications, fume extraction guns can help companies maintain compliance with safety regulations and create a cleaner, more comfortable welding environment for employees. When choosing fume extraction guns for MIG welding, look for features and accessories that will provide additional flexibility, time savings and advantages for welder comfort.