Avoid These 5 MIG Gun Myths to Optimize Performance
MIG guns and consumables are sometimes an afterthought when purchasing a welding system, but considering that they are the most handled piece of welding equipment and are exposed to the most environmental and operator abuse, they can have a significant impact on weld quality, productivity and operator downtime.
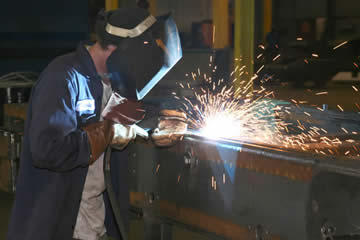
Much of the reason MIG guns and consumables do not receive their fair share of attention within the equipment selection process arises from common misconceptions about their importance in the welding operation.
The following are five of the most common myths surrounding MIG guns and consumables and the corresponding truths that can help you improve productivity, reduce costs and increase operator efficiency.
Myth #1 — MIG guns are all the same, so price should be the deciding factor when purchasing a new gun.
Truth — MIG guns vary substantially in quality, performance and value. Purchasing a quality gun designed with features that minimize downtime, weld quality problems and premature equipment failures can result in significant long-term savings. These efficiencies can save you far more than the price difference between a high performance and inferior quality gun.
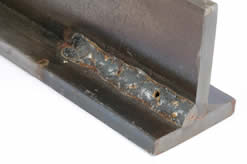
Conversely, a high quality MIG gun will offer features, design elements and construction that allow them to provide reduced operator fatigue and fewer burnbacks, birdnests and other problems.
When evaluating the long term value of a MIG gun and consumables system, you need to consider the service life of the gun, replacement parts costs, the cost of downtime when the gun needs servicing, and the ease with which components can be changed.
First, consider the downtime that can result from choosing MIG guns and consumables without looking into their full long-term cost. If a gun’s only selling point is its price, it could be manufactured with inferior components that don’t last as long as high quality components, are more difficult to replace when they do need replacing and cause the premature failure of other components.
An example of the difference between high and low-quality components can be found in the power cable fittings. Set-screw fittings can loosen over time and result in poor electrical conductivity and increased resistance. On their own, these problems can reduce weld quality and require reworking or scraping parts. Uncorrected, these problems can also lead to increased resistive heat at the point of the fitting. This heat causes additional stress and shortens the service life of the gun and cable. By contrast, a high performance gun often uses compression fittings, which produce a more secure connection between the cable and gun and will be less likely to result in weld defects or cause the deterioration of other components.
Consumables are another component in which trying to save a couple bucks on the purchase price could become very costly in the long run. A high quality consumables system requires fewer tip changeovers and those changeovers are often faster, reducing both equipment costs and operator downtime.
Overall, the cost of operator downtime should be your company’s primary reason to avoid choosing guns and consumables based solely on price. If each of your welders averages three hours a week adjusting and replacing MIG gun components, at an average employee cost of $30/hour, that downtime adds up to $4,680 per year in unnecessary costs (and that’s not even counting the material cost resulting from scrapped work).
Myth #2 — Consumables aren’t very important to weld quality and performance.
Truth — The MIG gun’s consumables — the nozzle, diffuser and contact tip — provide shielding gas and are the last component of the welding system to come into contact with the welding wire before it enters the weld pool. As such, consumables can have a big impact on weld quality and productivity, and selecting high quality ones and properly maintaining them is essential.
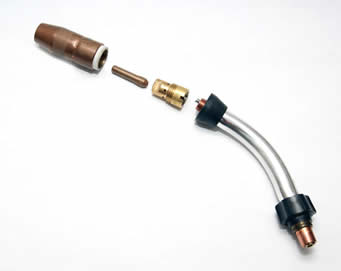
Consumables differ considerably by brand in terms of both design and material quality. Good quality consumables provide a large contact area between the diffuser and the contact tip and feature a secure locking mechanism to keep the contact tip and diffuser fitting tightly together. These features mitigate weld quality problems related to inconsistent electrical transfer, and also the frequency of contact tip burnbacks — a noteworthy source of downtime.
Equally important to selecting the right consumables is maintaining them properly. Good quality consumables resist built-up better than low quality ones, however, no consumables can completely avoid spatter build up. Use a needle nose pliers, nozzle reamer or other device to dislodge built up spatter to prevent interruptions in shielding gas flow and corresponding weld defects. You should inspect the nozzle for spatter build up several times a day and clean it out as needed.
In addition to checking and cleaning out spatter, you should check to ensure the contact tip sits tightly in the diffuser and that the inside bore has not become excessively worn. Non-threaded contact tips can be rotated in place to provide a new contact surface with the welding wire when it becomes worn on one side. Some threaded contact tips allow you to rotate them 180-degrees to also provide extended tip life.
Myth #3 — Preventative gun and consumables maintenance is a waste of valuable time that could be better spent in production.
Truth — Compared to the time spent reworking bad welds and replacing severely damaged components, spending a few minutes each day inspecting and maintaining the MIG gun and consumables is a bargain.
Identifying potential problems early is essential to avoiding the much higher costs that can result from allowing a minor problem to grow into a major headache. For example, a damaged O-ring on the feeder connection is very easy and inexpensive to repair, but left unchecked, it can create very costly weld porosity.
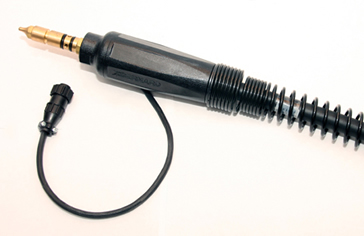
Because MIG guns have few moving parts and are relatively simple to inspect, you should check the connections between the wire feeder, the cable, the gun, the neck and the consumables on a daily basis to ensure they are tight and undamaged. A loose or damaged fitting can create resistive heat build-up, poor weld quality and shortened component life.
Consumables should be checked several times throughout the day to ensure the inside bore of the contact tip is not excessively worn down and that the shielding gas flow is not obstructed by spatter in the nozzle.
The liner is one of the most difficult MIG gun components to inspect, so it’s often best to use compressed air to clean out any metal shavings and debris during each wire changeover.
Routine inspection and maintenance should take up no more than 10 to 15 minutes per day, which averages out to about $1,300 per year in downtime. By contrast, reworking or scrapping bad welds can take up several hours each time it happens. If an operator spends four hours per week fixing weld defects caused by improperly maintained equipment, that non-production time costs his employer roughly $6,240 per year. Even more importantly, it can cause the company to fall behind on product deadlines and threaten their client relationships.
Myth #4 — It’s always better to err on the safe side and overmatch the gun amperage to the application.
Truth — It almost seems contradictory that most companies are making a mistake by purchasing a 400-amp MIG gun when their applications require 375 amps. In truth, the problem with overmatching the gun to the application is that most operators only weld for 30 to 50 percent of the time, which means that they can easily get by with a 300-amp gun and rarely, if ever, exceed its duty cycle in an application requiring 375 amps.
A 400-amp gun could certainly handle the demands of the application, but it is also heavier and bulkier, leading to earlier operator fatigue and reducing productivity.
In order to achieve maximum operator efficiency, companies need to analyze their specific welding demands and purchase a gun that is as small and light as possible while still meeting the amperage requirements of the application.
Another factor you should consider when purchasing a MIG gun is the weight and size differences between brands. In many cases, a gun from one company rated to 400 amps will be considerably heavier and bulkier than a similarly rated gun from another company.
Not all gun manufacturers label and market their guns to a 100 percent duty cycle rating, however, so be sure to verify that you are making an apples-to-apples comparison when evaluating MIG guns from different manufacturers. For example, company A’s 300-amp MIG gun might be able to weld at 300 amps at 100 percent duty cycle, but company B might also make a gun that they call a 300-amp MIG gun that is only rated to 300 amps at 40 percent duty cycle. The amperage to duty-cycle ratings are usually available in the spec sheets from most major MIG gun manufacturers, so check there to make sure the gun is able to handle your applications.
Myth #5 — The MIG gun liner does not have a significant impact on welding performance.
Truth — It’s true, properly functioning MIG gun liners, regardless of brand, do not have a significant impact on welding performance. It’s when the liner is not functioning properly that its importance in the welding operation — and the difference between a high and a low quality liner—becomes clear.
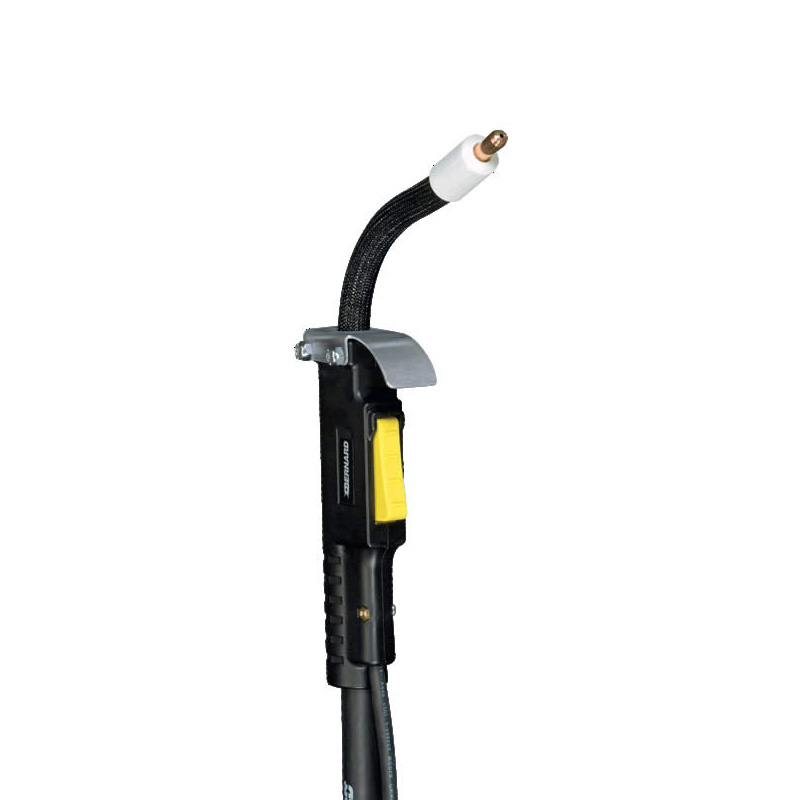
The liner’s main function is to provide unobstructed passage for the welding wire to travel from the feeder, though the cable and gun into the consumables. It’s a very simple role within the welding operation, yet a number of problems can arise in the liner that can lead to weld defects and lost productivity.
A high quality liner can provide a more consistent inside diameter through which the welding wire travels, thereby reducing friction and extending the service life of the liner as well as the time that it takes for wire filings to clog the liner—one of the most frequent sources of liner-related downtime. The liner is most susceptible to this problem when the cable is bent too far and increases the friction between the wire and liner.
Other causes of clogged liners include using an incorrect liner size and trimming it improperly. In both cases, the liner can shave metal filings from the welding wire and become clogged, leading to erratic wire feeding, poor weld quality and birdnests. Because the copper stranding in MIG gun cables is wound in a helix pattern, the cable shrinks when it is twisted. Trimming a new liner to the length of a twisted cable can cause the liner to be too short when the cable is straightened out, leaving an empty space in which the welding wire can become lodged and birdnest.
Additional downtime can be saved by using an easily-replaced partial liner that installs from the front of the gun and only goes through the gun’s neck. The most wire-to-liner friction occurs in the neck, so that part of the liner is usually the first to wear out. Rather than spending 20 minutes replacing the entire liner when only that portion becomes worn, some companies offer partial liners that can be changed in as little as two minutes.
In times of economic uncertainty, it’s understandable that companies would seek to reduce their production costs by purchasing less expensive equipment. However, the true cost of purchasing lower quality equipment — lost productivity, reduced weld quality, increased scrap and excessive downtime — can far outpace the cost of selecting higher quality MIG guns and consumables.